Blog
5 considerations for growing your AMR footprint
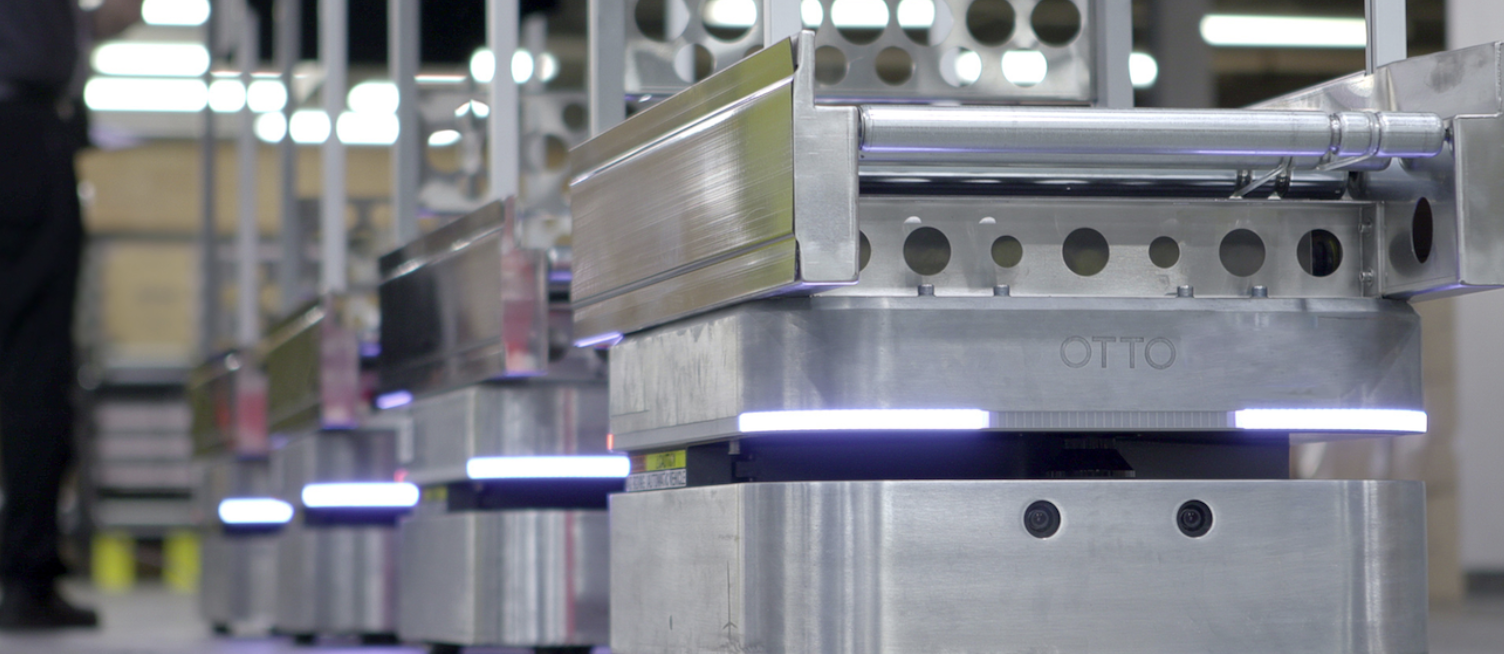
On December 5th, manufacturing professionals from across the globe joined us for a live webinar called “Beyond the Pilot: 5 Principles for Growing Your AMR Footprint.”
The webinar began by discussing the challenges of introducing new technologies, such as automation. Your workforce may ask the following questions as you develop a business case:
- What is the value of this new technology?
- Is it safe?
- Is it difficult to learn and use?
- Do I have to change the way I work?
- How does this impact my role?
The common theme across any of these projects that you’re undertaking is that there will be reluctance to change, and you need to pay close attention to communicating that change well.
Graham Davis
Product Enablement Manager, OTTO Motors by Rockwell Automation
It’s extremely important to help employees navigate this change by communicating the benefits clearly. For example, the factory of yesterday had higher costs, more potential for personal injury and a vulnerability to labor scarcity, while the factory of today lowers costs with automation, enabling improved safety and a reallocation of scarce labor to higher value work.
Before a scaled deployment of autonomous mobile robots (AMRs), many manufacturers begin with a pilot program to help prove value and generate internal excitement for the automation initiative. Some of the pillars you’ll want to address during the pilot stage are:
- Proving ROI and performance: demonstrate the value of a small deployment before investing in a large-scale project
- Creating champions: show staff the clear advantages and intended outcomes of the new solution so that they can vocalize their support
- Utilizing early training opportunities: introduce and train staff on the new technology early on to increase confidence and comfort working with it
- Identifying potential improvements: determine additional pathways or applications for the new solution
Often, a pilot project involves only a few AMRs, and it is very easy to show how one or two robots can move quickly through a facility. However, when you do scale, it’s important to understand how an AMR supplier maximizes productivity with an increasing number of robots. Thus, it’s important to consider the following five principles when growing your AMR footprint:
Design for safety
Safety is priority number one for any installation. While there are many different standards defining safety today, these standards quickly fall a step behind emerging technologies. The standards pertaining to AMRs are outdated and are missing advice on 3D object detection, robot dynamic testing and restrictions, and proper use of machine learning.
As you scale, safety becomes table stakes. The crucial consideration is if the system can maintain safety without compromising productivity. For example, some systems will trigger safety stops too often, resulting in lower average speed. At scale, this may result in significant productivity loss, impacting ROI. Search for a vendor who can achieve high throughput without compromising safety.
Design for capacity
Designing for capacity starts with understanding availability. Every system deployed will have a requirement for uptime. In a traditional fixed system, such as a conveyor, where pieces are linked together serially, a failure in one section can take down the entire line, reducing uptime and throughput. With AMRs, however, if one robot is offline, it can be taken out of service and the rest of the fleet can continue to accomplish the work. Designed correctly, AMRs can give you higher availability than fixed systems.
For example, a desired uptime of 99% means fourteen minutes of downtime per day or between three and four days per year. If you require ten AMRs working 99% of the time, you should consider the failure rate and calculate how much capacity is needed so ten are running at any given time.
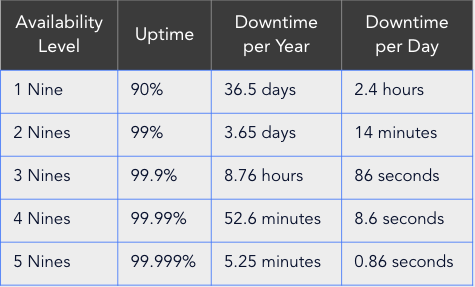
Image 1: Designing for capacity starts with understanding availability.
When planning at scale, you need to design for fleet availability, rather than robot availability. This way, you can still achieve your desired uptime when one or more robots are interrupted — the system can keep running even with a robot down.
Design for security
Manufacturers used to have completely closed off air gapped systems where physical security was all that was needed to protect the operations. With the push toward smart manufacturing, more sophisticated software, and more coordination with the home office, cybersecurity is becoming increasingly important. However, sending data across the internet needs to be done in a very regulated and standardized way.
For the greatest combination of security and optimization, the recommended approach is to:
- Set up your internet connection to be outside managed, maintained and secured by corporate IT
- Have a VPN connection to your AMR over the internet
- Ensure your AMR provider is following best practices like using SSL to further encrypt all communication to their data centers
- Ensure your AMR vendor is not ever storing personally identifiable information in their data centers or cloud deployments
Design for connectivity
The smart factory is connected. An increasing percentage of machines in operations are connecting to the network and need to talk to each other, but Wi-Fi networks weren’t initially crafted for automation.
AMRs collect tremendous amounts of information, and not all Wi-Fi networks are designed to support this, especially at scale. Moving from one or two robots to ten or twenty will increase the demand on your network. You need to consider how many AMRs you can add before your network exhibits failure modes.
When designing a solution at scale, you need to engage the AMR vendor in a discussion about robot bandwidth requirements early, and inquire whether they can conduct boundary tests before the actual implementation. These tests need to incorporate user errors and evaluate how an inconsistent Wi-Fi connection will impact overall fleet performance.
Design for scale
When deploying a pilot project, it’s important to think about scale from the beginning. As your material handling needs inevitably grow over time, the fleet management software needs to scale with it. Scale can be hard to achieve due to traffic volume, routing, space usage and new workflows. If you discover too late that the vendor cannot maintain productivity at scale, the consequences can be costly.
If you’ve only deployed one or two AMRs, changing vendors is simple. However, if you’ve deployed closer to ten or more, switching becomes harder. For example, someone in the company may have become accustomed to the product and well trained on it. Ultimately, you will likely have to start from scratch with a different vendor, lowering ROI. Testing can help combat this challenge early.
Since it wouldn’t be feasible to shut down your facility for weeks of testing, reconfiguration and retesting, your AMR vendor needs to have advanced simulation capabilities to mirror your factory deployment before purchase. The simulation should include a physical simulation to ensure all AMRs can navigate the map properly without getting stuck, and discrete event simulation to ensure the process flows smoothly.
Some questions you can ask your AMR vendor about future scalability include:
- Can additional robots and accessories be seamlessly added to the fleet manager without custom configuration?
- Is the fleet manager algorithm equally efficient in handling work assignments and charging for large fleets compared to fleets with fewer than five robots?
- Can the fleet manager effectively handle traffic at scale, preventing deadlock and jams?
- Most importantly, can you show me a real-world demonstration of scale from one of your customer deployments?
By optimizing processes and layouts, simulations can help you understand how many robots are needed, lowering costs and increasing ROI.
It’s important to consider and design for safety, capacity, security, connectivity and scalability as you grow your AMR footprint. You can find a checklist of what to consider for each principle here.