Blog
4 essential fleet manager capabilities needed for scaling AMR operations
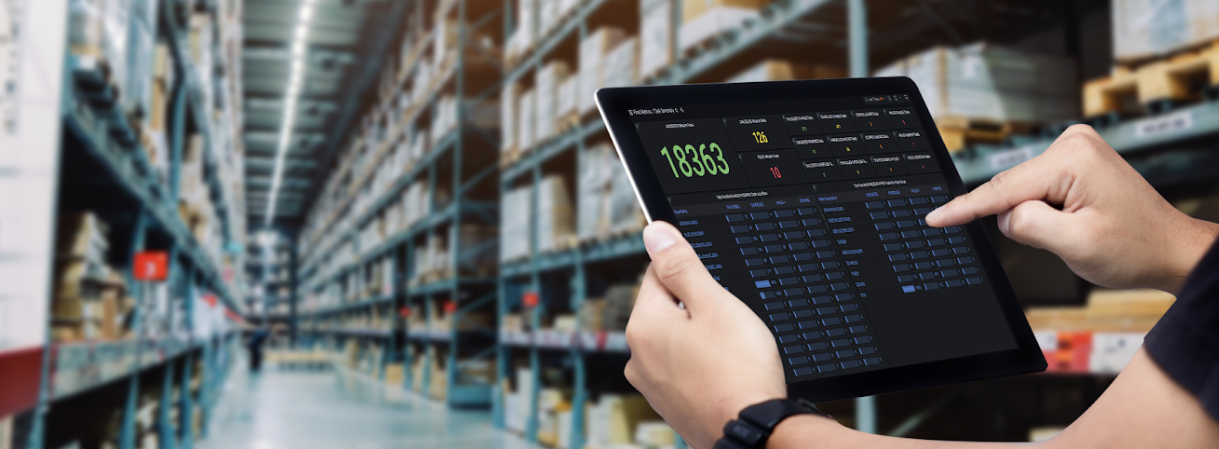
On July 11th, plant managers and automation engineers from across North America joined us for a live webinar called “Deep Dive: The Most Powerful and Scalable AMR Fleet Management Software.”
While AMRs are proven to increase productivity and efficiency within warehouse and factory facilities worldwide, implementing the robots themselves is only half the story. The right fleet management software can either level up your operations—providing powerful insights, building ROI, and unlocking business transformation at scale—or impair your operations.
Scale is about how much work you can do continuously and reliably throughout the day… Scale is when you have 100 robots running as productively at 2:00 p.m. as they were at 9:00 a.m.
Jay Judkowitz
VP of Product, OTTO Motors
When asked what stage of material handling automation they are currently in, approximately 40% of webinar attendees stated that they were in the beginning stages of their journey. While these stages would not involve scaling yet, it is critical to consider scale even in the early stages of material handling automation as the cost of change is too high. Thus, it is essential to select a vendor and a solution that is built to scale with you.
A truly scalable solution incorporates four main capabilities, including traffic management, job creation, facility integration, and ease of management.
Traffic management
When we drive on the road, there are certain rules each driver must follow, just like how AMRs must follow a set of rules as well. For AMRs, those rules fall into three main categories: path planning, robot behavior, and localization. In our most recent Spring 2023 software update, we introduced the ability to apply rules to teams of robots.
Besides setting specific rules, traffic management includes:
- Queuing: This capability of the OTTO Fleet Manager prevents traffic jams by allowing one robot to own a space while the others wait at a queuing point, and when the first is done, it relinquishes ownership to another robot, as displayed in the video below.
- Charge management: OTTO Fleet Manager assigns the right robot to go to charge, optimizing battery lifetime, maximizing material flow, and minimizing the number of chargers needed.
- Custom traffic management: This capability is highly customizable, enabling the configuration of more complex robot behaviors with custom scripting. For example, custom scripting can enable efficient alternating flows of one way traffic.
Job creation and issuing work
There are six main ways that Fleet Manager issues jobs, each applicable for different workflows and operation sizes:
- With workstation: On Fleet Manager, there is a button that an operator can press to call an AMR.
- With scheduler: Fleet Manager can be asked to do the same route all day or at a specific time each day. This option is ideal for predictable and repeatable workflows.
- Based on payload presence prompts: Operators specify on Fleet Manager when a container is empty or full, and the software monitors these payload states, issuing jobs accordingly.
- Based on automated presence detection: The AMR drives around, detecting new work that needs to be done and automatically updating the payload state on Fleet Manager, which then sends the robots to a job.
- After partial job: Here, an operator calls the robot to a nearby staging point when a job is partially done to avoid wasting time traveling. This is particularly important in large facilities.
- With OTTO APIs: Here, third party software is given control to determine which jobs are issued.
Once a job has been issued, Fleet Manager picks the best robot for the job. A robot is assigned to a job based on what they are currently doing, what their charge status is, and how close they are to the start of a job. Robots can also be assigned to teams based on attachment type, payload capacity, or sections of the factory, and jobs can be dispatched only to specific teams.
Efficient robot selection is critical to keeping takt time down and ROI high.
Jay Judkowitz
VP of Product, OTTO Motors
Facility integration
The robots also need to interact with the facility and control material handling attachments, including safely and reliably pulling payloads from machinery and pushing payloads onto machinery. For material transfer to happen, the AMR system needs to seamlessly:
- Dock up close to the factory equipment and know exactly where it is.
- Talk to the factory side PLC to do handshakes with interlocks.
- Activate the attachment for material transfer.
- Communicate with everyone once a transfer is complete.
The video below demonstrates facility integration at Amway’s Michigan facility. Amway has automated the palletizer to stretch wrapper workflow, where AMRs connect to integrated conveyors safely and reliably.
The growing industry desire for standard interfaces and open source management solutions has also led us to lead the market in interoperability as an early adopter of the standard VDA5050 through the creation of an open sourced VDA5050 to ROS connector.
Ease of management
While the above three main capabilities of a fleet management software are related to deploying safe and reliable automation of material handling at scale, what happens if there is a problem? When a deployment has one or two robots, very occasional downtime isn’t as big of a concern. However, when 100 robots aren’t meeting expectations at different times, productivity is negatively impacted.
There are three main ways to navigate the management of challenges at scale:
- Event notification: When a job is set up, certain expectations can be set; for example, expected duration. If a job takes longer than the expected duration, important personnel at the facility can be notified via Slack, SMS, or email.
- Troubleshooting: When someone is notified, troubleshooting is all about forensically figuring out what happened to prevent it from happening again. All job data, including sensor hits and what the robot saw, is snapshotted for the particular time of the exception. This snapshot can either be sent back to OTTO Motors for troubleshooting, or it can be solved directly in the facility.
- Fleet Analytics: OTTO Fleet Manager has a module called OTTO Fleet Analytics that enables manufacturers to work with data interactively to analyze the system, identify risks, optimize material flow, and ultimately improve ROI.
Fleet Analytics gives you a big picture view of how your deployment is doing and lets you find concentrations of problems and correlate data about failures or slownesses with particular robots, jobs, tasks, places, and time of day or day of the week, so that you can figure out exactly where problems are most frequent and focus your process engineering.
Jay Judkowitz
VP of Product, OTTO Motors
Any fleet management system should be able to effectively manage a few robots in a facility. However, a good solution should result in scaling, which means manufacturers need to select a vendor that is capable of scale from the beginning.
When evaluating vendors, ensure you ask about scale, specifically, “what is the largest deployment you have managed under a single fleet manager and how do you manage scale?” By asking this question, you should gain a better understanding of the vendor's solution. To learn more about our answer to this question, watch the webinar “Deep Dive: The Most Powerful and Scalable AMR Fleet Management Software.”