Blog
Industry 4.0 fuels lights-out manufacturing [webinar recap]

What is Industry 4.0 and how does it fuel lights-out manufacturing? Is lights-out really possible today or does it remain a far-reaching goal? In our webinar Industrial Robots for Lights-Out Manufacturing, we discuss these questions and more to discover how manufacturers are leveraging new technologies and processes to align with these philosophies.
Industry 4.0 meets lights-out manufacturing
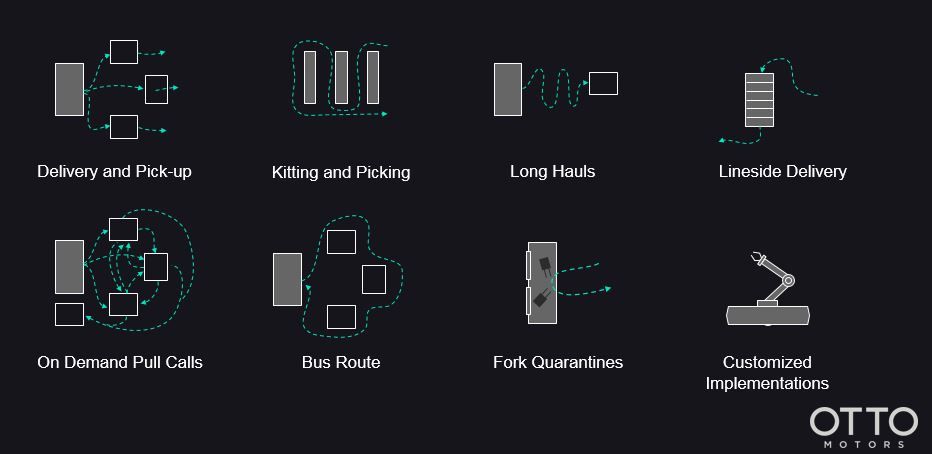
Lights-out manufacturing is the philosophy that factories can run fully automated and require no human assistance on site. Although very few factories are running exclusively lights out today, the current pace of technology development is allowing manufacturers to progress towards this goal faster than ever before.
Fueling this progression is Industry 4.0: the interconnection of industrial equipment that accesses and analyzes centralized operation data, real-time. Advanced capabilities like big data, interoperability, vertical networks, cyber physical systems and the internet of things (IoT) can merge to create a smart factory. The road to lights-out is a long one, but when smart products are tied together with smart processes, unprecedented value can be created for customers, manufacturers and their suppliers.
Q&A with HIROTEC AMERICA
We sat down with HIROTEC AMERICA’s VP of Business Development, Gary Krus, to learn what lights-out manufacturing means to his organization, what goes into the decision-making process when integrating new technology and why the OTTO autonomous mobile robot was selected for their lights-out project. Here is a sample of the discussion that you can listen to on-demand:
Q. WHAT IS THE 2025 LIGHTS-OUT VISION FOR HIROTEC AMERICA?
A. The questions we’ve always asked is “How do we reduce the number of operators? How do we increase efficiency of our plants? And how do we work around the clock, 24/7?” In order to get there, one of the strategies we’ve focused on is lights-out manufacturing. The OTTO autonomous mobile robot brings something unique to this vision. We can allow it to do some of the maintenance of changing out parts, loading parts and transporting them.
We’re always trying to take that next step, which is why we put so much focus into our R&D efforts. With our latest project using OTTO, we’re utilizing new 3D technology for vision, a new mobile platform and a new dual arm robot to test these technologies and determine how we can use them in the future.
Q. WHY IS LIGHTS-OUT MANUFACTURING A CORPORATE PRIORITY?
A. Some of the biggest challenges we experience are shortfalls in manpower to run production and shortfalls in finding skilled trade employees. By establishing lights-out manufacturing, we’re immediately creating jobs that are more technical and higher valued. For example, we may not need a line operator, but we would need someone who programs the robots that deliver to the line. We can let a robot do the mundane jobs - the day to day repetitive work that is difficult to fill either because the workers aren’t skilled in that field or because there simply isn’t a demand or interest for the job.
Q. HOW DO YOU FIND TECHNOLOGIES TO ENABLE YOUR LIGHTS-OUT VISION?
A. Flexibility and adaptability are always important to us, especially since we’re also looking to produce parts as a batch of one. When we research technologies, we look for technologies that can be integrated into our lines and scale with us. We work with not-for-profit laboratories or commercial providers to gain insights on solutions, understand how the technology works and understand its limitations.
We used to have lines that required 6 operators to run it. Today, the those lines have one operator at the front and one quality operator at the back - everything else in between is automated. Parts are delivered to the line automatically, racks are pushed into the line with automation, parts unload automatically with robots, and sensor systems inside the line perform quality checks. At our facility, we have a couple small assembly lines that don’t have operators, but they can’t yet run for 24 hours a day without human intervention. So we continue to research solutions and look at how this technology will integrate into the process.
Typically the research phase needs to link back to how we’ll be using the technology to run the production and, of course, what our customers need in their tooling to help drive costs down. Everything we do has a return on value that’s going to be important in the end.