Blog
Automated material handling is the secret to one piece flow for lean production
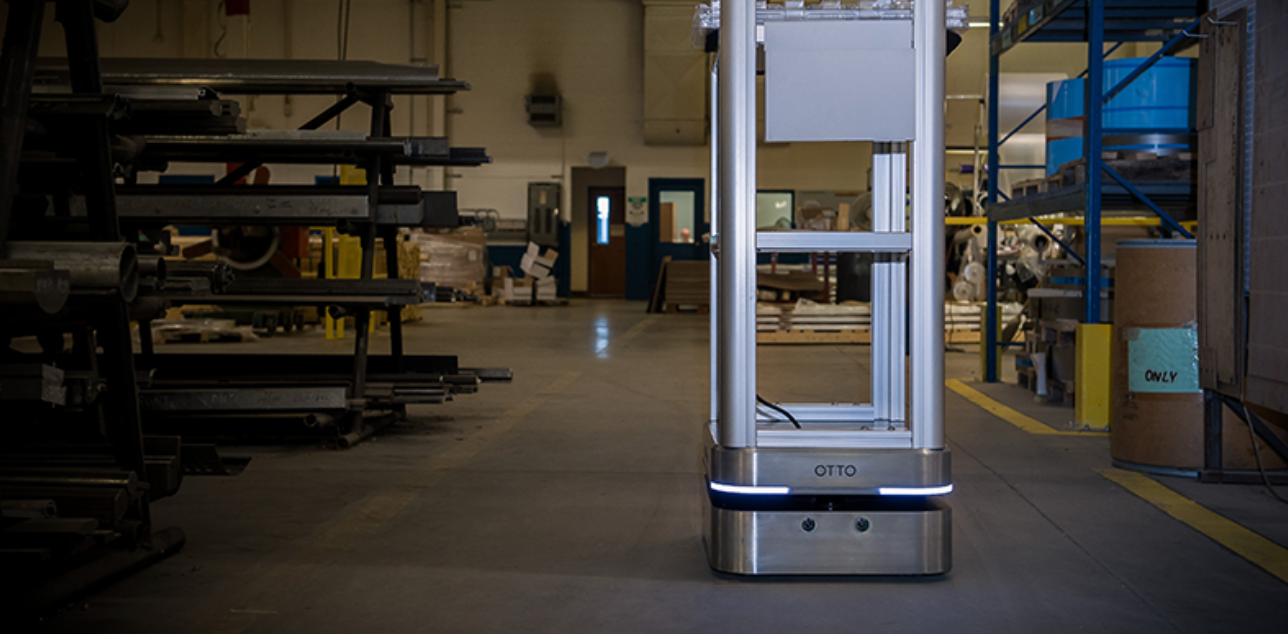
Whether you’re running a mid-sized enterprise or a multinational conglomerate, a lean manufacturing system can be integrated in manufacturing and assembly cells that drive a variety of advantages within the operation. One of the biggest benefits to a cellular manufacturing process is the gradual removal of inventory between cells, where operators carefully control stock on hand. This concept is ‘piece of one flow’; it is the ultimate goal of lean systems. Its potential, however, is limited if the material handling to and from (and between) workcells neglects to level production with an on-demand delivery. One piece flow is only truly successful if the operators within the cells adhere to the on-demand process; it’s imperative there is a material handling solution in place that provides operators with the required parts in time for the downstream operator. Failure to do so will lead to the lean waste of waiting.
One piece flow is on-demand, isn't it?
In theory, yes. But let’s look at the classic case: The operator in workcell 1 is a highly skilled, multifunctional employee. She can perform tasks in addition to handling the material and operating the equipment, including quality control, inspection for defects, machine tool maintenance, setup reduction, and problem solving. To start the day, she receives her single piece and completes the task at hand. The second piece arrives before she has a chance to manually transport the first to the next station. As she is a high performer and focused at the task at hand, she thinks “I’m on a roll. Why not do one more?” And so, the one piece flow is interrupted and the operator in workcell 2, although occupied with one of his multiple tasks, neglects to receive the next order on demand. The production of said piece becomes delayed.
By the time materials are moved, workcell 2 then receives multiple pieces, slowing the reception and adding time for sorting. That, in turn, delays QA, which creates a bottleneck of materials that are being prepared for invoicing; the likelihood of defects goes up when QA is rushed. Invoicing is hit with multiple orders at the end of the day and cannot process them all before the truck needs to leave and adds to work at the start of the next before the next day's materials can be received. The real cost is not just slowed production, but added overtime labour, higher defect rate, direct costs for expedited shipping, added labour in shipping and receiving for busy periods.
Using automated material handling for lean production
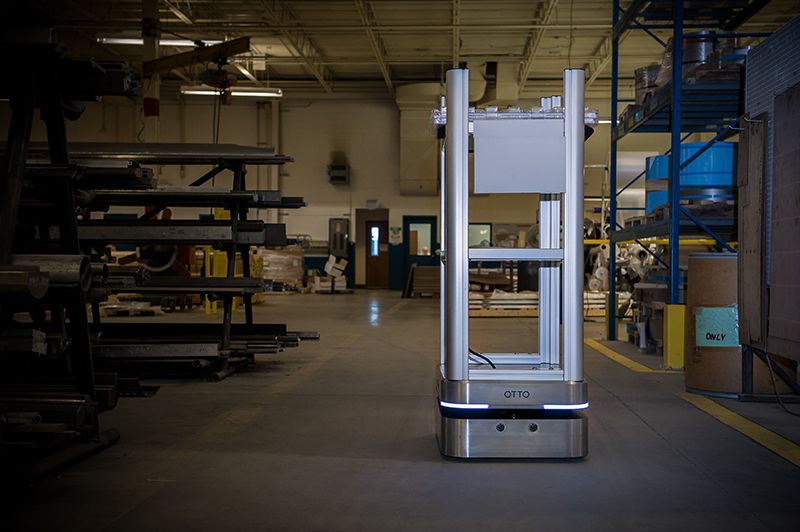
A mobile robot can take on a variety of form factors, but those that can support one piece flow production offer flexible, intelligent, on-demand delivery of parts. The material handling can be triggered by the workcell operator, but the actual transportation of parts between cells occurs autonomously. That is to say, the automated material handling system understands where it needs to go and moves dynamically through the layout to bring the part to the next operator.
An automated material handling solution addresses the delivery of material within a known and consistent time that is not subject to breaks, distractions, sick days, etc. ...or operator in workcell 1 getting caught up on building just one more unit. It improves the ability of the lean team to plan with the knowledge of the exact time it takes to deliver parts.