Blog
Unlock continuous productivity in automotive factories and warehouses with OTTO 100 and the customizable staging cart
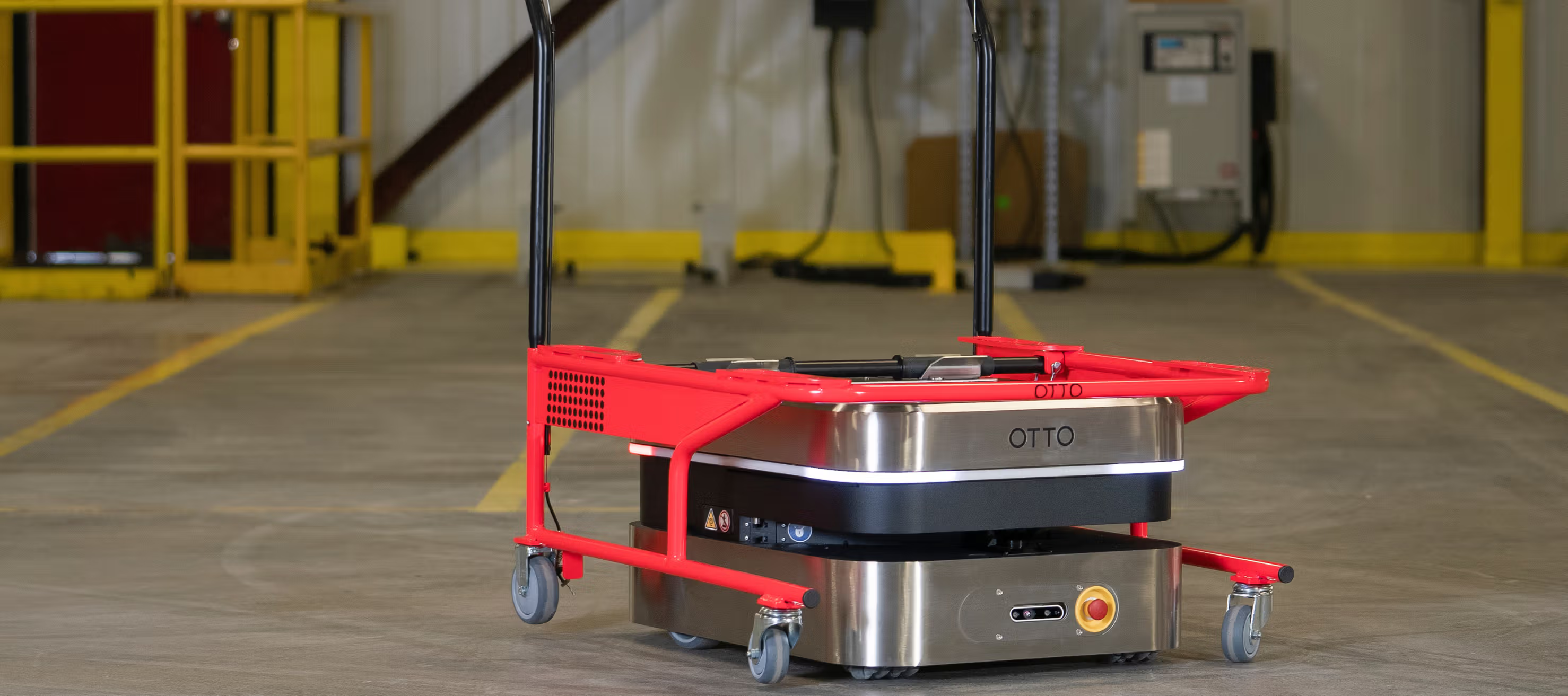
The automotive industry is rapidly changing as the world drives toward a sustainable future. With the rapid rise of battery electric vehicle (BEV) demand, automotive manufacturing facilities can’t keep up. By 2030, every third car sold is predicted to be electric, aligning with the 360% growth in BEV market value from 2021 to 2028.
Alongside this increase in BEV demand comes a decrease in available labor. In fact, while 4.6 million new manufacturing jobs are projected to be created by 2028, over half could go unfilled because of this global labor shortage.
To exacerbate the problem, due to international conflict, increasing trade barriers, the pandemic, and more, automotive OEMs can no longer rely on offshore, fragile supply chains for just-in-time manufacturing. Instead, automotive OEMs are increasingly using automation to onshore operations and combat the labor shortage challenge while keeping up with BEV demand. In 2022, 55% of all robot units ordered went to the automotive industry to help automate operations and heal the supply chain.
Investing in automation is increasingly seen as a necessary step for performing many of the difficult-to-staff tasks that are necessary to complete today.
Jeff Burnstein
President, Association for Advancing Automation (A3)
Automating automotive material handling with OTTO 100 and the staging cart with custom Minomi
Traditionally, automotive OEMs have relied on manual material handling, through the use of carts, pallet jacks, forklifts and tuggers to move automotive components throughout the facility, from lineside delivery to work-in-progress transport. To automate this process, top automotive OEMs and suppliers are replacing this repetitive manual process with flexible, efficient robots, such as the OTTO 100.
The OTTO 100 is an industrial strength autonomous mobile robot (AMR) that safely moves boxes, bins, carts and other payloads up to 150kg. Automotive OEMs and suppliers use OTTO 100 to move a wide variety of parts to lineside such as fuel tanks, brake lines, mirrors, filler necks, fascias, wiring harnesses and more.
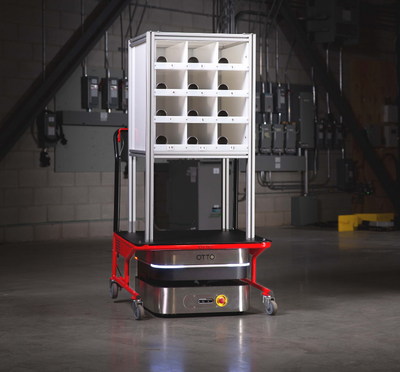
The OTTO 100 with an engaged staging cart carrying exhaust pipe sub components to lineside.
Besides placing boxes onto the OTTO 100 directly, manufacturing facilities are using the OTTO staging cart with custom Minomi’s for more versatile workflows. The staging cart has been specifically designed for OTTO 100 as an attachment that the AMR can effortlessly engage and disengage with to assist in material handling.
While other AMR solutions require automotive OEMs and suppliers to permanently attach a fixture to the robot that can be loaded onto, limiting the robot’s productivity while it waits for the parts to be unloaded, the staging cart is fully independent of OTTO 100. This means OTTO 100 can drop off the staging cart at one workstation, and continue moving materials around the production floor while parts are unloaded, inspected, and utilized. Thus, the OTTO Motors staging cart prioritizes productivity of the robots by increasing their independence from a load.
Variants of the staging cart
The staging carts have been designed in four variations. The first is a flatbed plate, suitable for larger boxes or totes. The second is a pre-configured shelving unit which is more suitable for smaller boxes or parts. Both are intended for use out of the box, with no time needed for set up.
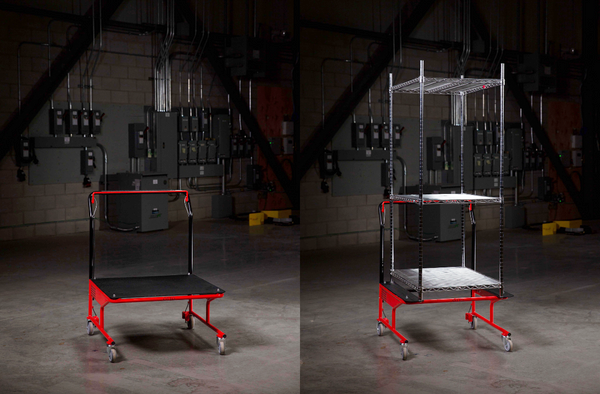
The staging cart with a flatbed plate (left) and an attached shelving unit (right).
The other two variations are more suitable for customization, as automotive OEMs and suppliers can create fixtures that mount on the staging cart that are unique to the particular component, sub assembly, or final assembly that is being transported.
Thus, while the staging cart attachment is customized for the payload, it is still a common interface for the AMR engagement. Since the staging cart is able to be delivered to lineside by OTTO 100, the operator can retrieve the parts directly from the staging cart, eliminating the need for lineside racking for the parts being transported.
Some companies are further optimizing by utilizing a gravity rack or gates that are lowered via push pins. When the OTTO 100 reaches the delivery point, the staging cart is docked precisely to the gravity rack, and a custom engagement device allows the gates to lower, and the components roll off the cart and onto the gravity rack. The OTTO 100 then brings the staging cart back to be refilled.
Top three staging cart applications in the automotive industry
1. Full and empty Minomi delivery to lineside
In this use case, the staging carts are positioned side by side. OTTO 100 brings the first cart full of parts from inventory to the lineside, where the operator removes the parts. While this is ongoing, OTTO 100 is busy bringing a second cart from the supermarket to be positioned beside the cart being emptied.
Once the first cart is empty, the operator uses a simple web interface to change the cart status from full to empty, and OTTO Fleet Manager automatically triggers OTTO 100 to retrieve the empty cart and bring a new full cart. As OTTO is doing this, the operator empties the second cart, and the “now and next” process begins again. This process can be seen with a custom staging cart attachment filled with exhaust sub components in the video below.
This use case is best utilized when the automotive manufacturing facility strives to limit downtime due to container handling, and allows seamless component delivery without influencing the assembly line takt time and throughput.
2. Autonomous cart delivery to lineside from marketplace
In the second use case, the staging carts are positioned front to back, reflecting a marketplace layout where there is not enough space to position the carts side by side. The operator removes parts from the front cart until it is empty, and then manually swaps the carts. When the carts have been swapped, the operator uses that same simple web interface to change the rear cart status from full to empty, and the OTTO Fleet Manager automatically triggers a job to retrieve the empty cart and bring a new full cart for the process to begin again.
This use case is also demonstrated in the video below and is best suited when a facility utilizes a supermarket to sequence components for final line assembly, and operators require the flexibility to move the cart throughout the marketplace for component selection.
3. Lane clearing / FIFO Buffer Management / dolly swap
In this third use case, the staging carts are positioned front to back once again. The difference in this use case, however, is that the operator is not expected to exchange the cart positions manually once the front cart is emptied.
Here, the operator will utilize a FIFO Buffer Management system to remove parts from the front cart until it is empty, and use that simple web interface to change the front cart status. OTTO Fleet Manager then automatically triggers a job to swap the cart positions on the lineside, take away the empty cart, and bring a new full cart, clearing the lane. This way, the operator can continue to work on something else or move between stations while OTTO swaps the carts automatically. Then, the process begins again. This is demonstrated in the video below.
This use case is best utilized when the automotive manufacturing facility has limited space and the operator is either not too busy at that particular station or has to move between stations in the facility. FIFO (First In First Out) buffer management can be handled seamlessly within the OTTO Fleet Management system, to ensure manufacturing throughput and just in time delivery is maintained through the entire operation.
The OTTO 100 and its customizable staging cart are essential components of your automotive facility’s autonomous material handling. The combination of robot and staging cart works across many variations and use cases to deliver unmatched productivity that can help you onshore operations, while fulfilling your increasing demand and combating the labor shortage challenge.
Automotive OEMs and suppliers aren’t stopping at the OTTO 100, though. Our heavier payload AMRs, such as the OTTO 1500 and OTTO Lifter, can be used to transport wheels, rims, engines, battery packs, hoods and more.