Blog
Pioneering perspectives: “OTTO’s autonomous forklift pushed the boundaries of material handling”
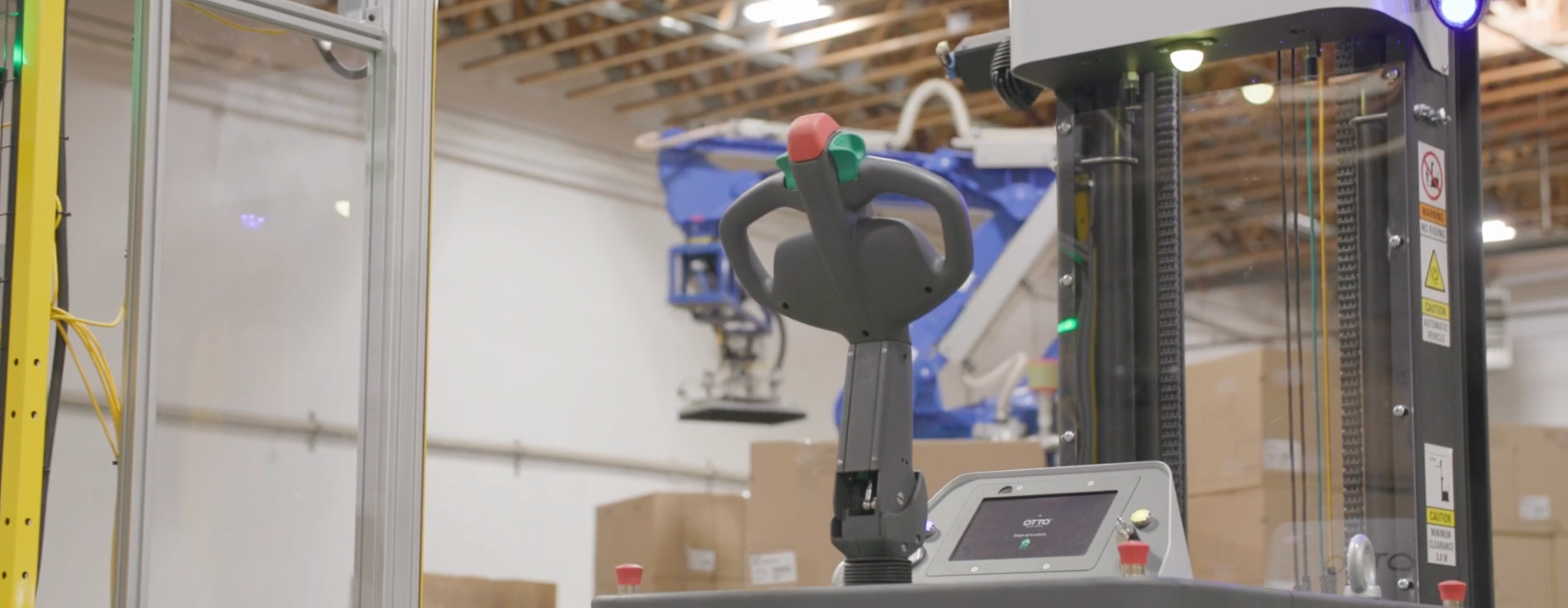
Written by Jacob, Senior Account Executive at OTTO by Rockwell Automation.
As one of the first customers of OTTO Lifter, an autonomous forklift, I saw first hand how customers are pushing the boundaries of OTTO’s solution. First as a customer and now as an employee, I have seen the impact that autonomous forklifts can have on material handling and its safety.
How a Fortune 500 CPG manufacturer began their AMR journey
I was the Director of Equipment Solutions at a $13 billion company in the consumer packaged goods industry. With over 250 facilities worldwide, this Fortune 500 company serves the agricultural, food and beverage, commercial, industrial and personal care customers in the consumer packaging markets. Tasked with evaluating autonomous mobile robot (AMR) solutions, I remember going to OTTO’s headquarters many years ago to see their robots in action and meet with the co-founders, Matt and Ryan. Since then, we have deployed OTTO 100 and OTTO 1500 at four of our facilities, and counting. There was one facility, however, that was looking for a different solution than the others— an injection molding and decorating facility in Henderson, Nevada, USA.
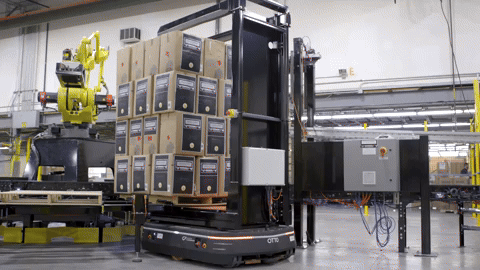
Image 1: OTTO 1500 deployed at one of seven facilities.
How we chose an AMR vendor and autonomous forklift
In 2022, the Henderson facility began evaluating AMR solutions to reduce material handling costs and manage our employees more efficiently, but most importantly, to improve safety, which was the company’s number one priority. Many of our employees were approaching retirement age, and I knew automation could help reduce the physical aspects of the job, improving employee retention and wellbeing. One of the AMR requirements to improve safety was to select a robot that maintained safe, ergonomic working heights for manual material movement.
While other AMRs introduced elevation that could cause ergonomic strain, an autonomous forklift allowed our employees to maximize safety and minimize ergonomic risk by maintaining ideal ergonomic material handling elevations. This repetitive process was required up to 25 times per hour by our operators.
Additionally, we knew that an AMR would eliminate required infrastructure changes and costs associated with fixed and inflexible conveyor systems, rail cars, and transfer systems. The alternative was hundreds of feet of linear conveyor paired with a mobile transfer cart, which would have consumed more floor space, required more maintenance and a difficult implementation, all while costing more and being less flexible.
With a 90% chance of a serious accident occurring during the 8-year average lifespan of a forklift, according to OSHA, OTTO knew that manual forklifts are unsafe. In order to offer a safer solution to the industry that mimicked the capabilities of a manual forklift, OTTO developed a different type of AMR, iterating their existing solution into a new form factor. OTTO Lifter was launched in 2022 to help manufacturers move pallets between stands, machines, and floor locations, bridging an industry gap that opened the door to new material handling workflows that could now be automated.
Having deployed OTTO’s flatbed AMRs in four facilities previously, we already knew that their software was best in class and trusted that it would work well in the Henderson facility simply in a different form factor.
I was excited about Lifter’s ability to transport materials from floor to floor—as a manual forklift would—significantly reducing the risk of ergonomic strain.
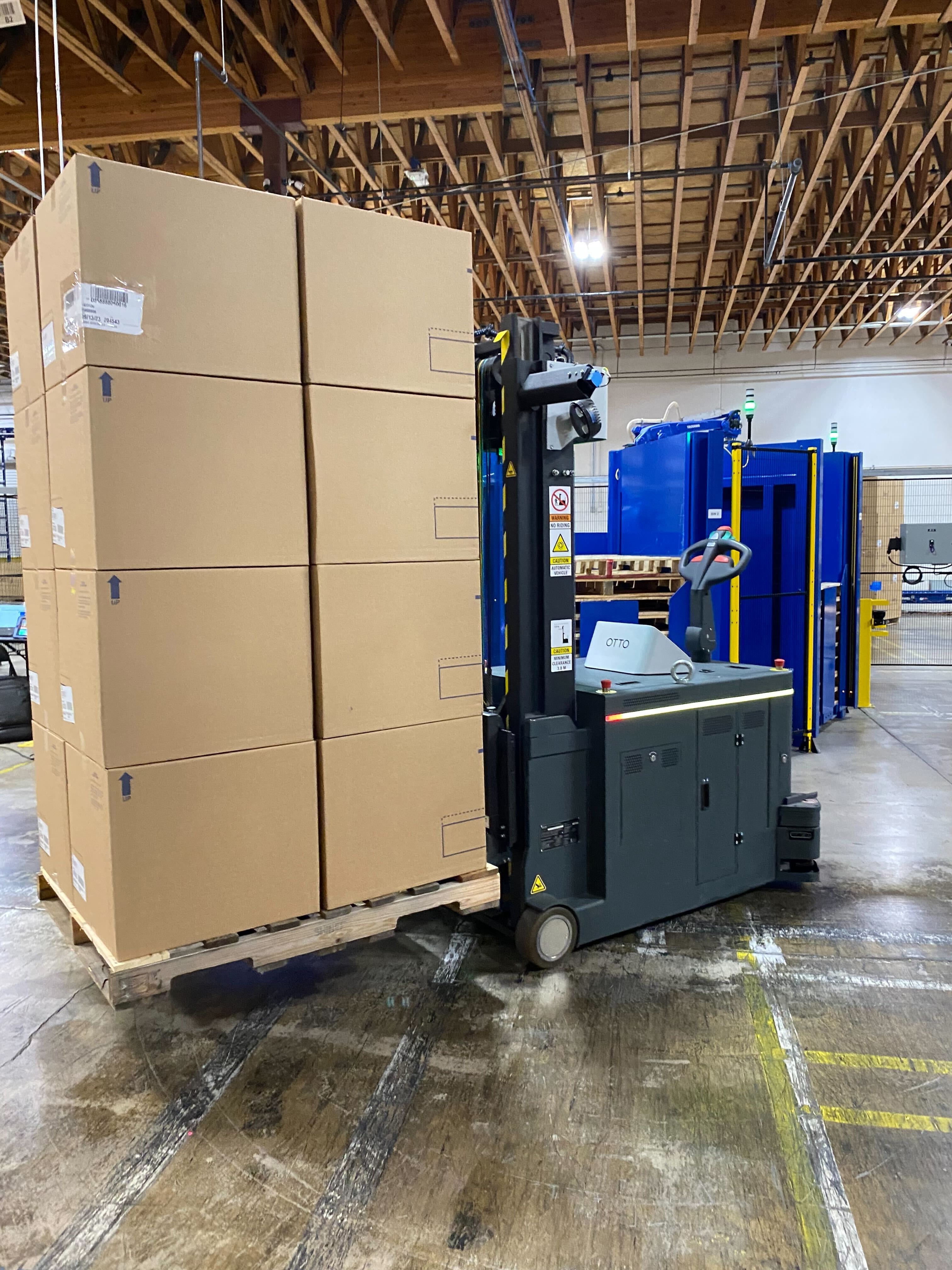
Image 2: OTTO Lifter carrying products through the Henderson, Nevada facility.
We also trusted OTTO’s commitment to safety, and believed it was superior to other AMR providers in the industry. While other providers were willing to sacrifice safety to slightly improve throughput, OTTO aligned with our commitment of safety first. OTTO was only willing to deploy a system that we both knew was safe for our employees. We respected OTTO tremendously for this commitment, and definitively knew they were the best company for the job.
Deployed at the Henderson facility in 2023, OTTO Lifter is already helping improve ergonomics, retain employees, and optimize floor space.
The deployment experience
The Henderson facility was one of the first manufacturing facilities to ever deploy OTTO Lifter, which led to some new and unexpected challenges. Deploying a forked AMR is certainly different from deploying a flatbed, and requires a unique set of considerations. For example, forklifts come with a different level of stability and center of gravity that needs to be considered in the design stage of deployment.
Deployment came with challenges of its own, which OTTO did not shy away from. Our team pushed the boundaries of OTTO’s capabilities and what is possible with their solution. For example, we were focused on the quality of our products, not on the quality of the pallets they are transported on. As long as the pallet could sufficiently hold the product, it was used; however, Lifter requires consistency in the pallets it picks up.
This quickly became a challenge, but OTTO began working on it right away, advancing the product’s capabilities to align with our needs.
We realized very quickly that OTTO was dedicated to our success, and it created a strong relationship between our two companies. OTTO was and always has been focused on their customers and finding solutions to the market’s biggest challenges together. This is ingrained in their culture and their employees, and is ultimately what inspired me to join the OTTO team in 2024. Now, I am excited to help customers achieve their productivity and safety goals with the leading autonomous material handling solution.
Interested in a career at OTTO? Apply today.
Subscribe to our newsletter
Stay in the loop on product news, case studies, upcoming events and more.