Blog
The growing digital divide in manufacturing

This is the second blog in our "The Business Case for AMRs" series. You can read the first blog here.
There is a growing consensus that digitization is opening up a chasm in the manufacturing industry.
On one side, there are the innovative, tech-savvy firms that are forging ahead full speed with digital transformation strategies, and reaping the benefits of doing so. On the other side, are businesses that have been slower to embrace the ‘Industry 4.0’ trend and who are at risk of falling behind as a result.
Deloitte reports that early adopters of smart factory initiatives have enjoyed average gains of 10 to 12% in areas such as manufacturing output, factory utilization and labor productivity. Research published in The Harvard Business Review found that digital leaders are 1.5 times more likely to optimize production runs based on demand forecast.
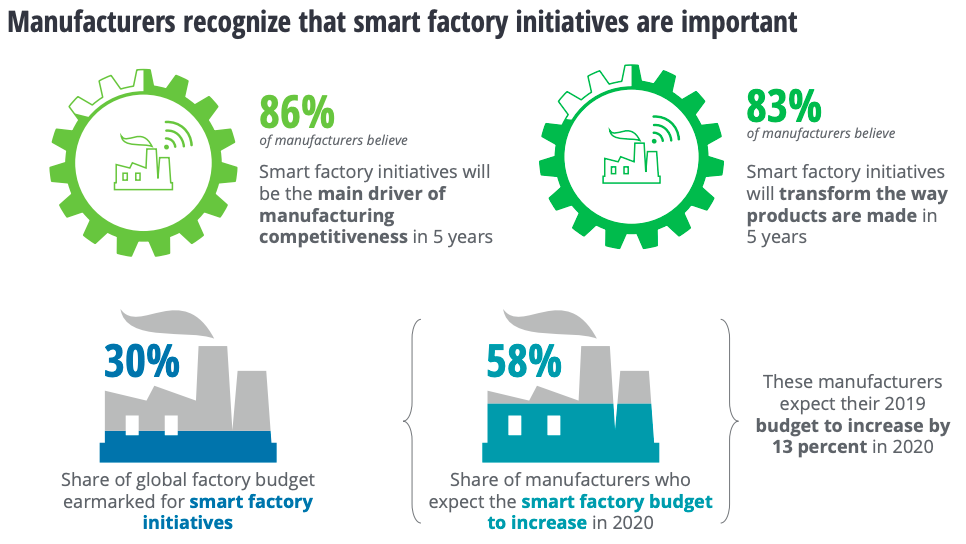
Source: Deloitte analysis of the 2019 Deloitte and MAPI Smart Factory Study data
Moreover, there are fears that COVID-19 could make the divide even greater. According to a survey carried out by L.E.K, 51% of businesses with existing advanced digital capabilities plan to invest more in digitized operations in response to the pandemic, compared to 30% of firms overall.
It isn’t that the benefits of digitization are disputed. According to another study carried out by Deloitte, 69% of decision-makers said switching to a digital supply chain would deliver exponential or significant benefits to their business.
Yet only a third said they were prioritizing this as a strategic objective. Asked what the barriers to digitization were, the most common answer was budgetary constraints. Other issues cited included not knowing where to start, misalignment of competing priorities across the business, and difficulties making the long term business case within a rigid financial reporting framework.
Making good the promise
As far back as 2016, industry bodies were heralding mobile robotics as critical pieces in the jigsaw for achieving agile, efficient “always-on” supply chains. According to Robotics.org, the use of mobile robots as an intralogistics solution would streamline workflows, cut picking errors, boost throughput, consolidate space and offset rising labor shortages and costs.
These are all benefits that the challenges of the COVID-19 pandemic bring into sharp relief. As a result, Interact Analysis has said that it believes the impact of the pandemic will lead to a long-term net rise in mobile robotics adoption.
“We believe that the impact of COVID-19 will lead to a long-term net positive for the mobile robot industry. E-commerce, near-shoring of manufacturing and adoption of robotics and automation to reduce reliance on human labor will all likely accelerate. This remains one of the most resilient and promising industries that we track.”
Ash Sharma
MD & Senior Research Director - UK, Interact Analysis
And yet for all this promise, adoption rates in the robotics sector don’t yet get anywhere near matching the hype. By some estimates, advanced automation only plays a role in around 3% of goods produced.
Low penetration of advanced technologies is a key driver of manufacturing’s digital divide. When you look at the reasons why so many firms say they are yet to adopt - budgetary concerns, competing priorities, difficulties making the business case - a clear picture emerges. Firms don’t need promise, they need hard evidence backed up with numbers that prove the case.
That’s why we set out, in partnership with materials handling specialists PULSE Integration, to undertake what we believe is the world’s first in-depth analysis of automated mobile robots (AMRs) deployed at scale in industrial facilities. To see the analysis, read the next blog in our series: Proving the Case for Autonomous Mobile Robots.