Blog
Embracing the digital mindset: Top takeaways from MHI’s 2020 industry report
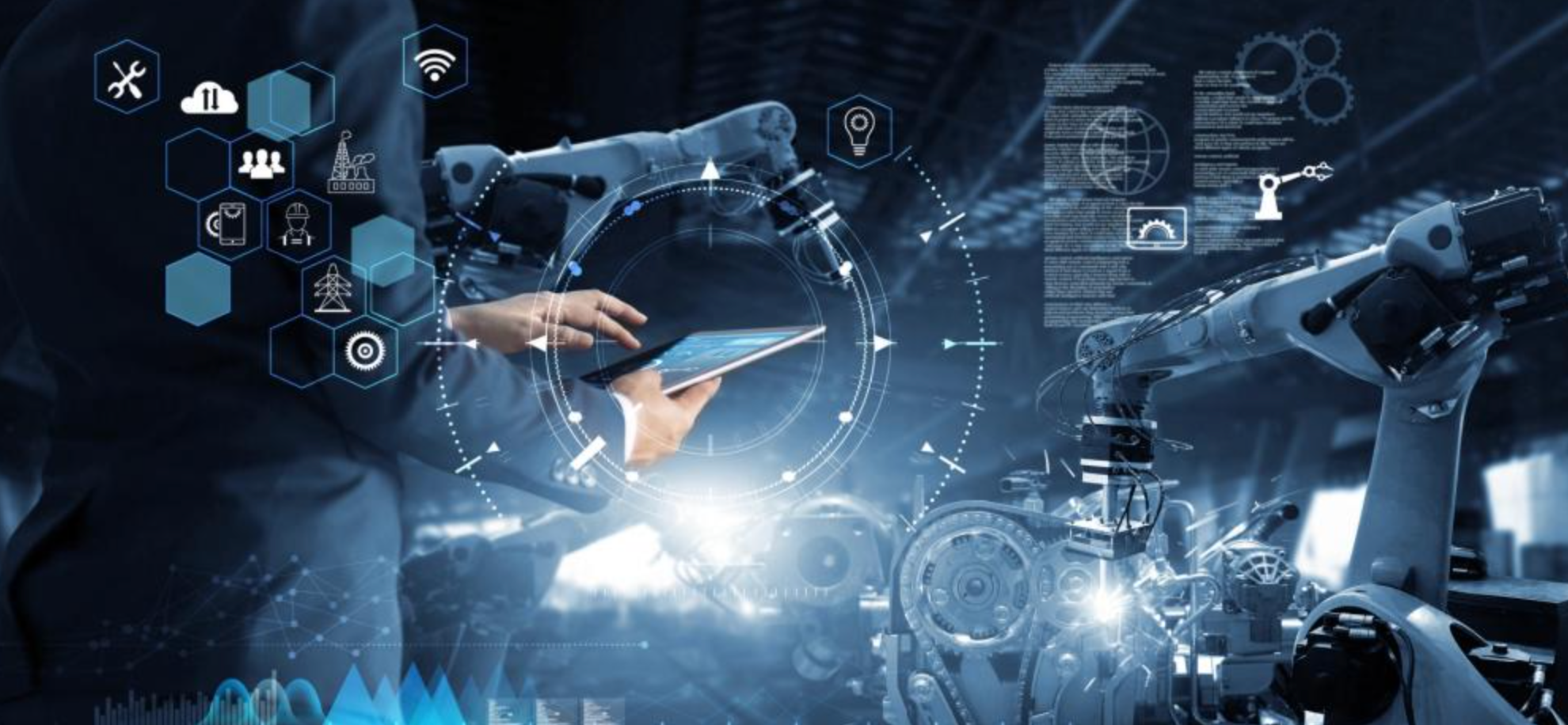
The 2020 MHI Industry Report provides a wealth of data, analysis and recommendations for your company’s investment plans. Since all five of the top company challenges have remained the same since 2019’s report, it is important that companies understand how to combat these challenges through Industry 4.0 technologies.
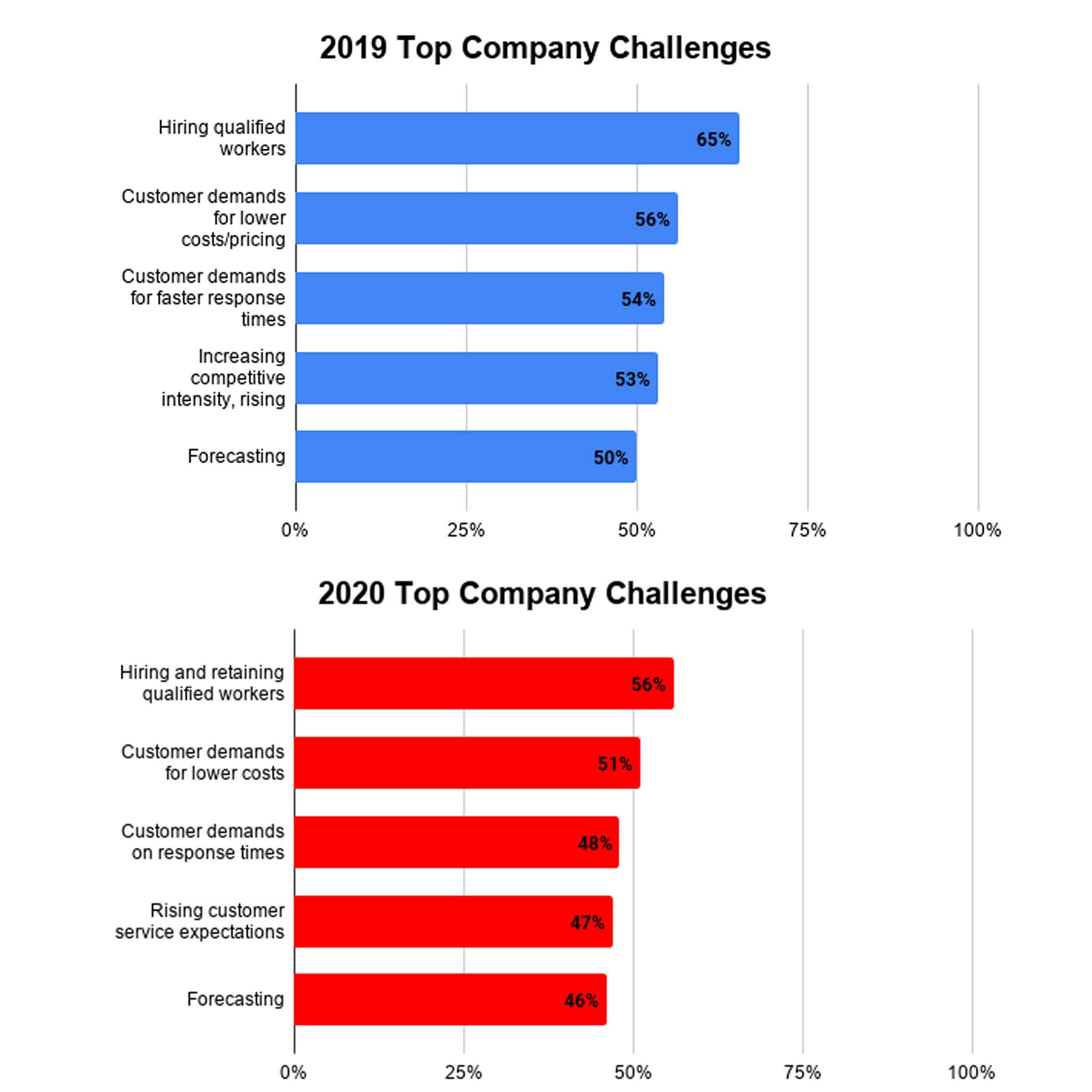
Chart 1: MHI’s top company challenges from 2019 to 2020. Hiring qualified workers remains the industry's top challenge.
With these company challenges in mind, here are the top three 2020 report takeaways you need to know:
1. Data is the world’s most valuable resource – and it can (and should) be at your fingertips
Global supply chains are becoming increasingly linked and data-dependent. Companies no longer settle for hardware alone, and technology providers recognize that, focusing on software capabilities instead.
With the need for constant supply chain improvement, autonomous collection and analysis of data are the most valuable resources available to supply chain managers, especially since 84% of supply chain managers are not good at capturing, processing and integrating data streams on their own.
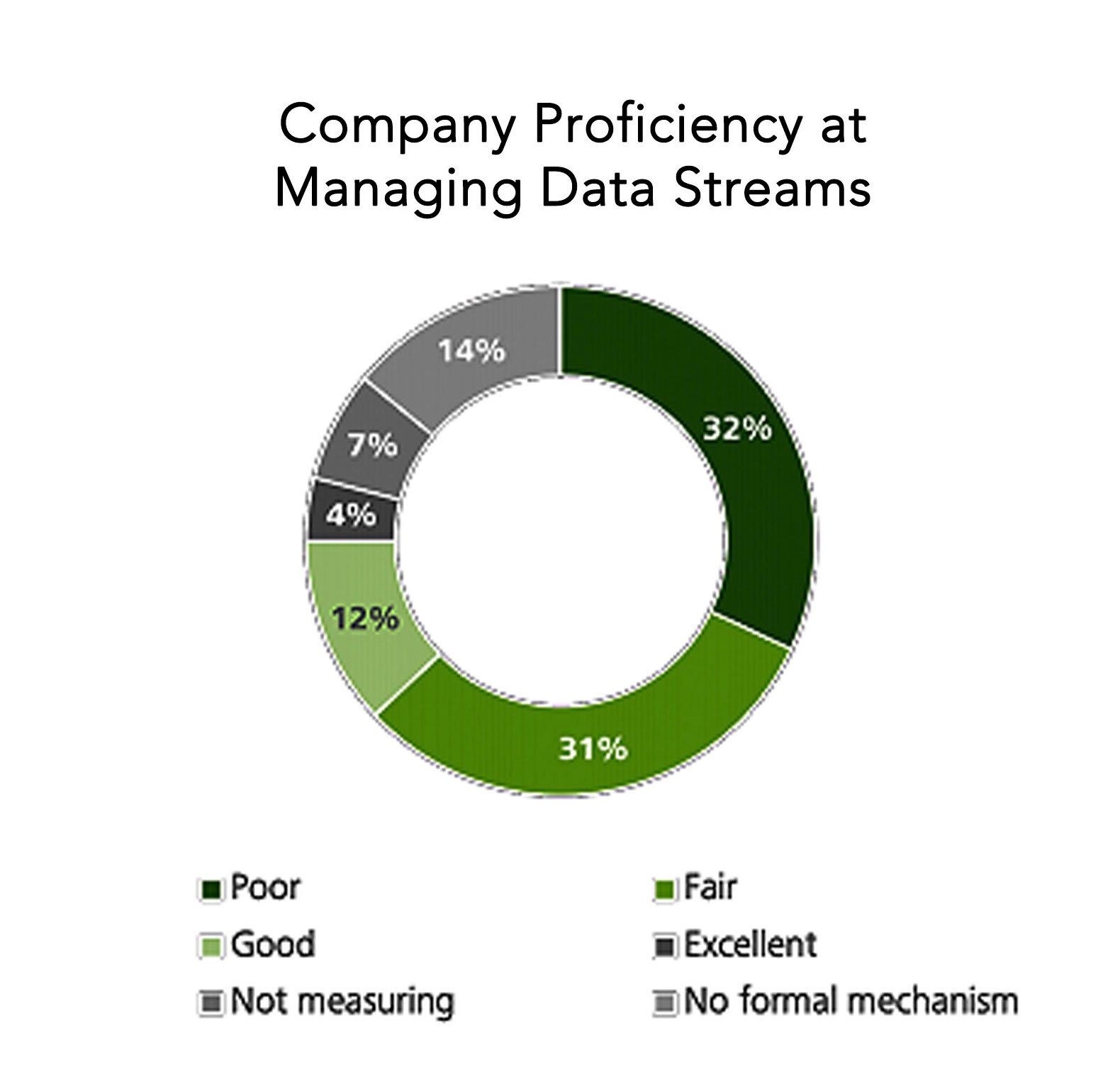
Chart 2: Company proficiency at managing data streams is limited, with only 4% considering themselves “excellent”.
A lack of visibility into supply chains:
- Is a key contributor to product shortages and counterfeits
- Will cause companies to fall behind their competition
- Makes it difficult to identify cost-reducing opportunities and organizational inefficiencies
Data is the life’s blood of the emerging digital supply chain. Companies that recognize the value of this data and engineer approaches to collect, filter and synthesize it into customer and market insights will flourish. Those who do not will drown in the wave of exponential data proliferation.
Thomas Boykin
Deloitte Consulting, LLP
With 20% of supply chain leaders believing the digital supply chain is already the prominent model, and 80% expecting it to become predominant within 5 years, it is important to invest in data-collecting technologies now, such as Autonomous Mobile Robots (AMRs), to reap the benefits of current industry-driving technology.
Action steps for your business:
- Invest in Industry 4.0 technologies with data collection capabilities
- Assemble a team that is responsible for analyzing and recommending actions based on the data collected
- Consider additional investments in data-collecting technologies as your budget allows. The more data-collecting technologies at your facility, the more your operation will consistently progress
2. Reskill your current workforce to maintain a competitive advantage
With finding talent considered extremely or somewhat challenging by 71% of respondents, many companies have become victims of the skilled-labor shortage impacting supply chains around the world. In fact, 73% of respondents say it takes more than 30 days to fill open positions, and 78% say there is high competition for prospective employees with the skills needed in today’s workplace.
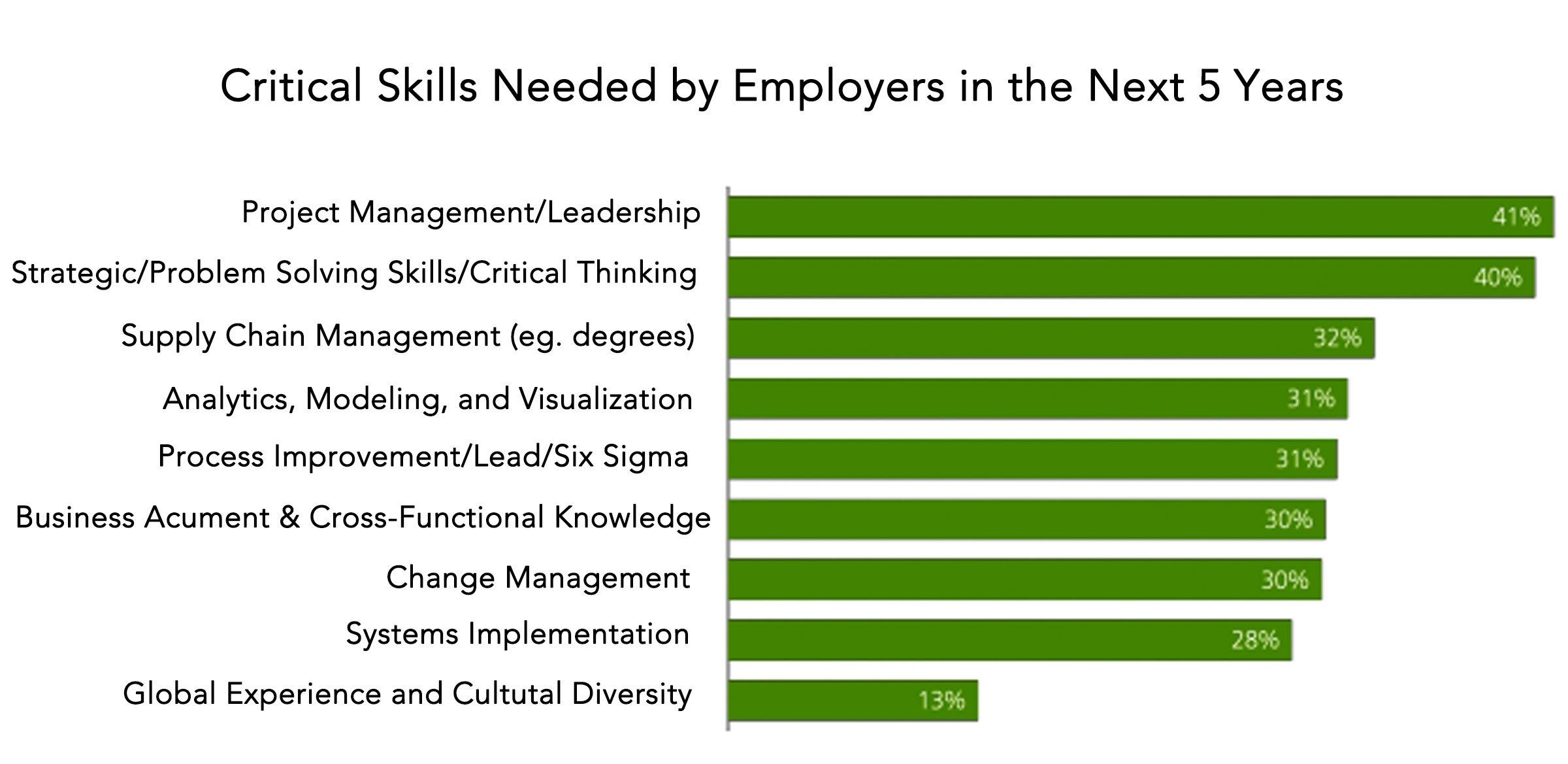
Chart 3: The crucial skills needed by employers over the next five years, with project management and critical thinking leading.
Companies are increasingly investing in digital technologies, and the market for recruiting new talent is competitive and limited, so many companies are looking inside their operation to find and invest in existing employees. In fact, while 37% of companies plan to address their future technology adoption challenges through recruiting, 30% plan to do so through reskilling and retraining existing workers.
Reskilling and retraining your current workforce can:
- Allow companies to transition employees from overstaffed areas of the operation to areas in need of workers
- Keep workers performing tasks that digital technologies cannot do faster and for cheaper, optimizing efficiency and saving money
- Help build a talent pool that fits a company’s specific and future needs – filled with employees who already understand the existing operations, and do not need to be trained from scratch
- Encourage employees and provide opportunities for personal growth and job satisfaction
In order to reskill or retrain employees, some companies are sending workers to educational classes or investing in in-house training. For example, Walmart developed the Walmart Academy, a training program complete with virtual reality, augmented reality and stimulation technology to train store and supply chain associates.
These reskilling actions resulted in:
- Improved consistency of training
- Faster deployment of new technology
- Increased employee pride and sense of accomplishment
Everybody wants to win. One of the most demotivating things is trying to perform a task that one hasn’t yet been trained to do with excellence. We all like to know how to do our jobs the best way and, when we have the proper training and skills to perform our job, we are more confident, more productive and enjoy our work more.
Steve Miller
Vice President Supply Chain People, Walmart U.S.
Action steps for your business:
- Analyze your workplace with a focus on needed areas for skilled workers, as well as areas where digital technology can better be used
- Find in-house talent capable of reskilling and search for motivated employees with an interest in elevating their careers at your company
- Be transparent about the role digital technology will play in these workers’ jobs, and retrain them accordingly
3. Disrupt the market now - invest in industry 4.0 technologies
Since 2019’s report, robotics and automation has moved from the 6th to the 1st most likely technology to create a competitive advantage and disrupt the market, with 67% of respondents believing it will do so. Other top technologies with this potential include:
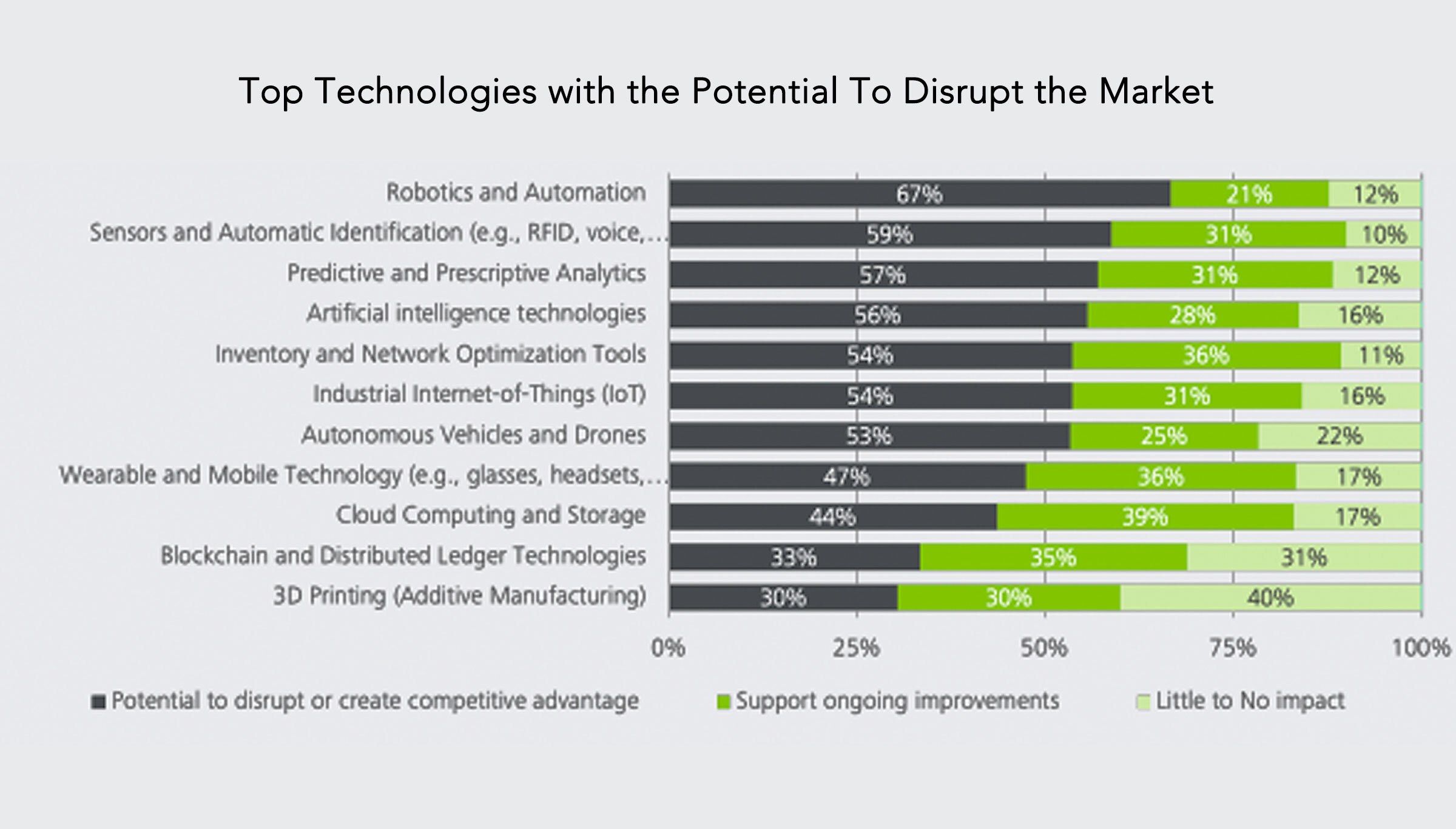
Chart 4: The top three technologies with the potential to disrupt the market or create a competitive advantage include robotics and automation, sensors and automatic identification, and predictive and prescriptive analytics.
By investing in robotics and automation, you would join the 39% of survey respondents investing in these technologies today, and the 34% budgeting to invest in them within five years. Stay ahead of your competition by investing now.
Investing in these technologies will also help you fill your talent gaps to further provide a competitive advantage. “NextGen” employees (workers under the age of 40) are generally not drawn to manufacturing careers, considering them boring and outdated. However, these employees consistently want to work for companies with emerging, innovative technologies, including 80% of millennials who are drawn toward companies with leading technology, such as robotics and automation.
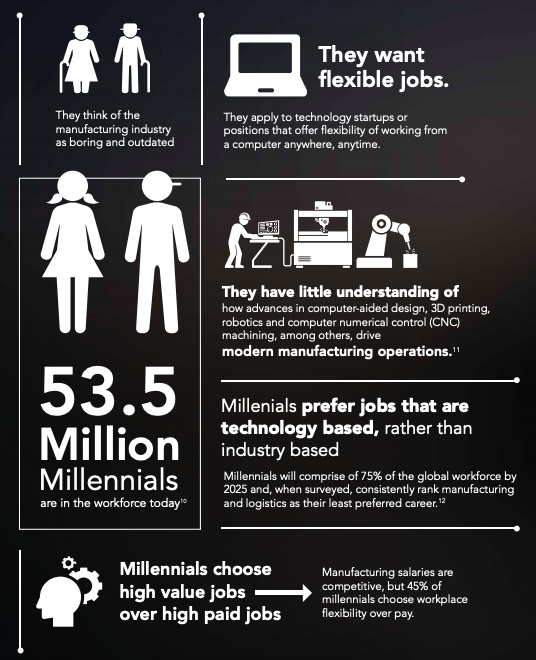
Image 1: While historically millenials have not been drawn to the manufacturing industry, innovative technologies can attract them.
Workforce challenges cannot be solved without building and maintaining a culture of innovation and technology within your organization. Talent and technology are fundamentally linked together in the success of future supply chains.
George Prest
CEO, MHI
By investing in leading technologies now, you can disrupt the market, create a competitive advantage, and attract younger employees to your supply chain.
Action steps for your business
- Establish a commitment to enhancing your supply chain with digital technologies such as robotics and automation while there’s still time to stay ahead of your competition
- Consider adopting a variety of Industry 4.0 technologies to work toward lights-out manufacturing and provide extensive data for consumption. Utilize MHI’s Supply Chain Digital Consciousness Index to assess your digital mindset and chart a path toward adopting digital technologies
- Adopt technologies that are proven to provide actionable insights via data, allow for retraining of existing workers, and that will attract potential workers to your difficult-to-fill positions