Choosing the right material handling technology: Why Sunview Patio Doors automated with AMRs

Sunview Patio Doors (Sunview) quickly understood that manual material movement was limiting their efficiency, flexibility, and safety. Read more about the challenges that led Sunview to incorporate automation in their operation. Once Sunview knew they needed to automate, they had to determine which type of material handling technology would best meet their needs for increased safety, flexibility and efficiency: AGVs or AMRs?
AGVs Do Not Meet Sunview’s Needs
Sunview initially considered automating with Automated Guided Vehicles (AGVs), but they found limitations that proved to be insurmountable, and they ultimately decided to implement the benefits of autonomous mobile robots (AMRs).
AGVs are computer-controlled machines that rely on guidance devices such as magnetic tape, beacons, barcodes or predefined laser paths to move from location to location on a factory floor. If an obstruction blocks their predefined path, AGVs remain halted until a worker comes to remove the obstruction. In some cases, AGVs can’t operate around humans at all.
In our case, that magnetic strip would probably be cut on day one, or someone would put something in front of the sign posts stopping the entire operation.
Kurt Oberparleiter
Vice President of Operations, Sunview Patio Doors
If AGVs are like a street car, using predetermined paths, then AMRs are like an Uber. Similar to an Uber, AMRs are flexible and do not require external infrastructure for navigation, saving money and time-to-implementation. Instead, AMRs use onboard sensors, machine learning and AI to understand their environment and adapt to changes in real-time to detect and avoid obstacles. AMRs are also highly scalable and are able to be used in multiple applications.
AMRs in Sunview's Operation
Sunview used an AMR to automate the process of bringing the finished product from the end of the production line to the warehouse, then reloading and bringing the empty pallets back. Sunview’s AMR collaborates with humans daily to ensure the right products are loaded on the vehicle and then delivered to the right place, at the right time.
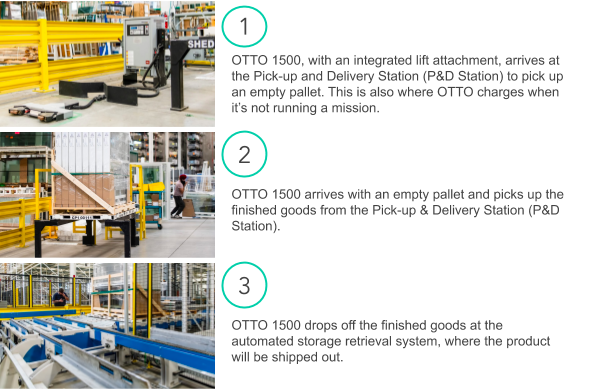
A Showcase Facility in Action
Implementing an AMR has allowed Sunview to standardize their processes, improving the entire flow of the plant. The response from clients and prospects who tour the Sunview facility and see an OTTO autonomous mobile robot in action has also been positive.
The factory sells for us. It awes people who come to see it. It helps our sales organization close deals, because people see OTTO and immediately understand that Sunview is a forward-thinking, innovative company, and they want to do business with us.
Kurt Oberparleiter
VP of Operations, Sunview
Through implementing innovative Industry 4.0 technology, Sunview is seen as a Showcase Facility in their industry. Sunview's innovation will enable them to grow their revenue by 38% over three years—nearly four times the rate of growth in the least innovative manufacturing companies.
As the pace of supply chain innovation escalates, so does the price of inaction. Leaders will outpace their competitors faster than ever.
George Prest
CEO, MHI