Blog
3 AMR software capabilities that are critical in successful deployments
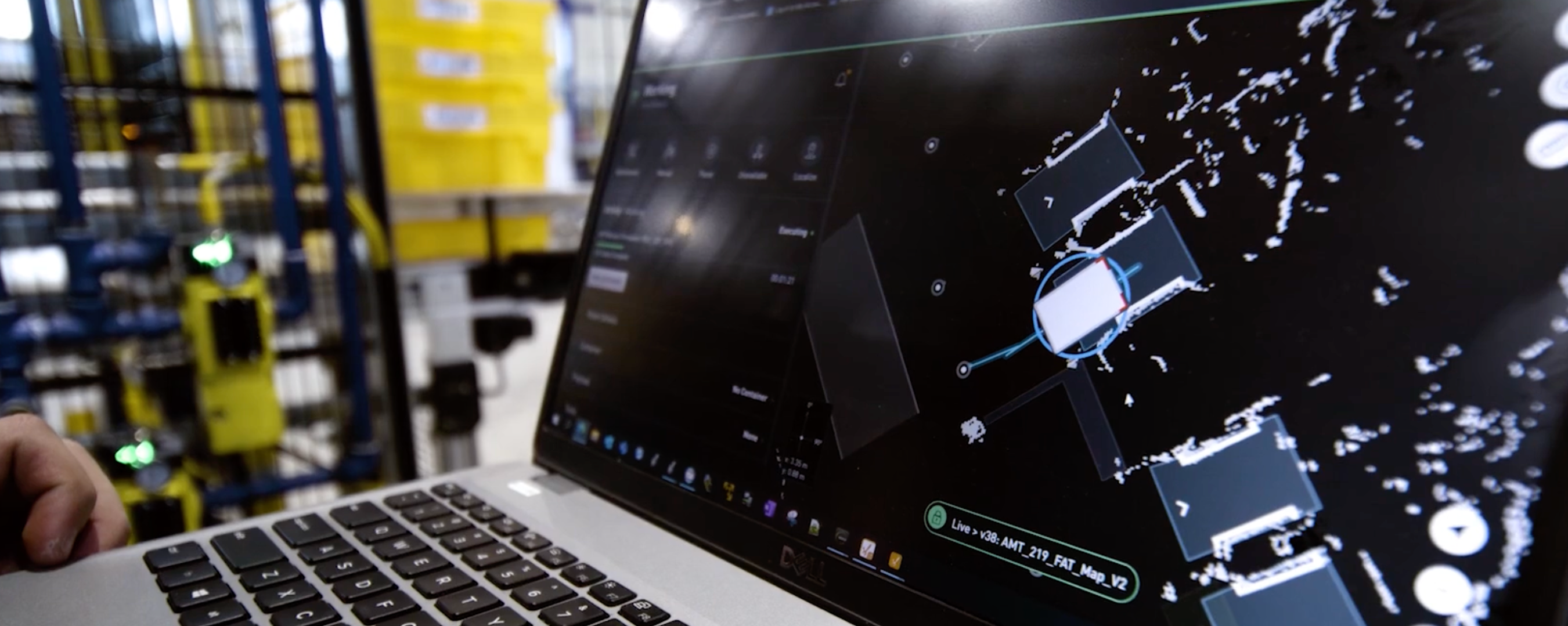
Autonomous mobile robots (AMRs) are increasingly adopted across the manufacturing industry to increase safety, improve inefficiencies, and reallocate available labor to more fulfilling tasks. AMR deployments achieve next-level efficiency when they are powered by a sophisticated software suite that transforms your material movement and maximizes ROI. As outlined in this software webinar, below are three software capabilities that are key to solving top automation challenges, distinguishing the successful deployments from the challenging ones.
1. Maximizing productivity in tight, dynamic spaces
In many manufacturing facilities, space is at a premium as a result of narrow aisles, crowded floors, and poor floor conditions. It is crucial to select a solution that can operate efficiently, and with a minimal footprint.
When combining environmental factors relating to the customers' sites (e.g. lack of space, floor suitability, climate), these become the second largest barrier to mobile robot adoption.
2024 Mobile Robots Buyer Survey by Interact Analysis
Alongside implementing narrow robots that can move heavy loads, such as OTTO 600 and OTTO 1200, software is the key to overcoming these barriers and ensuring that AMRs operate efficiently, even in tight and challenging spaces.
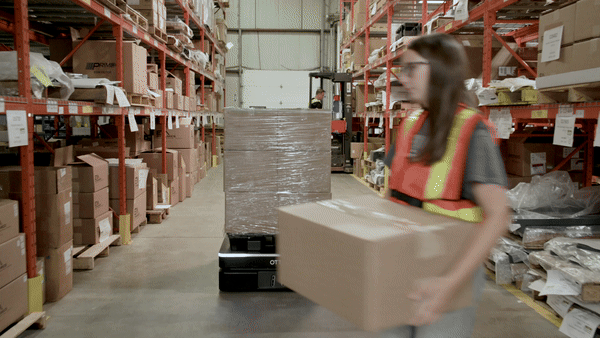
The advanced software capabilities that drive productivity in tight, dynamic spaces are:
- Safely avoiding static and dynamic obstacles with adaptive fieldset technology: Working like adaptive headlights on a performance car, the fieldsets shift and extend out in the direction the robot is turning. The improved visibility allows AMRs to prevent unnecessary stops or slowdowns at intersections and around people, obstacles, and turns, ensuring sustained productivity and a higher average speed without compromise to safety.
- Navigating in narrow aisles without sacrificing productivity or safety with fieldset switching: Some AMRs have the ability to increase their average speed by up to 2x with a fieldset switching feature. When an overhanging payload is unloaded, the AMR will run on a smaller LiDAR safety footprint, enabling more nimble movement and higher throughput.
- Efficiently rerouting when blocked with guided navigation technology: Automated guided vehicles (AGVs), another material handling technology, operate like a train on a track, following a predefined path and unable to navigate around obstacles blocking their path. With guided navigation technology, AMRs can work similar to Google Maps, creating and following the most efficient route on a road network to provide a combination of flexibility and predictability.
- Maximizing use of limited floor space with parking space optimization: Capable of decreasing the space needed for dedicated parking by up to 50%, AMRs with a parking space optimization feature can park at locations other than their designated spots—such as P&D stand endpoints—reducing the need for parking space while also cutting down travel time and improving productivity.
When GE HealthCare introduced AMRs to reduce wasted floor space and increase material flow efficiency, they saw a reduction in repair cell sizes by 40%, increasing productive floor space in their facility by 66%.
2. Centrally integrating with existing factory systems
Adapting to unique manufacturing environments is just one consideration in facility-scale automation. Centrally integrating with your broader facility’s existing software, hardware and other material handling equipment is essential to deployment success. Centralized integrations enhance operational productivity by ensuring different automation systems work together to create a fully connected operation. This simplifies monitoring and management, reduces the need for manual intervention, and ensures smooth communication between AMRs and other systems.
The advanced software capabilities that enable central integrations are:
- Ensuring continuous productivity by connecting with your business management systems: The chosen software should integrate with your business management systems to offer operators a variety of manual and automated dispatch options using convenient, pre-built fleet APIs. This will reduce custom coding and enable you to start moving materials within days, not weeks. By responding immediately to your key business drivers, the software will ensure the right part gets to the right place at the right time.
- Improving safety by communicating with your existing PLCs, without the need for additional sensors: To enable real-time communication when transferring a payload between AMR attachments and your existing equipment’s PLCs, your selected software should have a built-in appliance proxy. This type of integration offers manufacturers a scalable way of coordinating and monitoring the status of payload transfers across their facility, without the need for additional sensors and set-up time.
- Collaborating seamlessly with other material handling systems, without custom integration work: By enabling customers to select and combine the best solutions from different vendors, you can reduce integration costs, improve flexibility and increase productivity. The software should be compliant with an interoperability standard, such as VDA5050, to support third-party fleet management softwares and establish a common interface without custom integration work.
Amway—a manufacturer of health, beauty and home care products—used PLC integrations to simplify deployment, enabling a sophisticated industrial workflow. In this workflow, the AMR software talks to a PLC which opens the door from a room where the AMR is parked to the area they need to move. The robot drives to the palletizer, communicates with an Ignition OPC-UA server to arrange the transfer of an unwrapped pallet, and drives to the stretch wrapper. Here, an Ignition for PLC integration arranges the pallet transfer back onto the AMR for delivery. By implementing AMRs, Amway was able to reduce costs related to infrastructure and labor, while improving flexibility.
3. Future-proofing operations through productive scaling
Over time, your AMR deployment will grow, and it’s important to choose a solution that grows with it. As you get further into a project with a software solution that cannot manage scale, the harder and more expensive it is to switch providers. Thus, it’s essential to consider the scalability of AMR software before deploying even a pilot program.
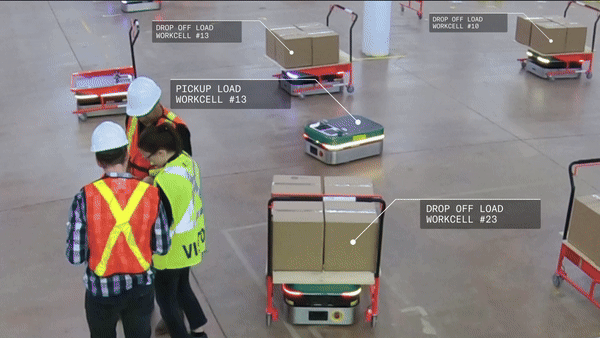
The advanced software capabilities that enable productive scaling are:
- Selecting the right robot for the right task at the right time with queuing: By ensuring multiple robots are not all directed to the same endpoint simultaneously, AMR software helps prevent congestion. With a queuing feature, one robot claims ownership of a space while the others wait their turn. Your chosen software should also continuously track each robot’s location, destination and job status, then automatically and intelligently select which robot should do which jobs in real time.
- Optimizing charge management with opportunistic charging: AMR software should maintain optimal charge levels without impacting production by autonomously sending robots to charge in between jobs throughout the day. This enables AMRs to share charging interfaces, optimizing cost savings and improving the ease of scaling.
- Managing traffic efficiently for all map sizes and fleet sizes with traffic rules: AMR software should optimize how robots move through your facility using zones for path planning, behavior and localization. It should enable you to establish traffic rules, such as speed limits, for all robots in the facility and apply select rules to teams of robots carrying out different types of tasks.
- User-friendly commissioning and troubleshooting with sophisticated features: Adding new AMRs should be as easy as a few clicks when they inherit the existing fleet’s configurations. Once you’ve created an endpoint template, such as a charger or a pallet, every subsequent endpoint you add to the system should be effortless. As the deployment grows, additions become easier.
Driven by labor force changes, increasing competition, and the need for business continuity, a Fortune 500 household name in consumer packaged goods deployed over 80 AMRs to transport raw materials and finished goods. The deployed AMRs have reduced labor costs, enhanced safety, and boosted productivity, traveling over 1,100 miles and completing more than 5,200 missions per day.
When evaluating AMR vendors, it is essential to consider their software as you determine how the solution will help meet your goals and address your challenges across scalability, integrations, security, productivity and more. To help you define your software requirements and create RFPs that effectively communicate your needs, we’ve created an evaluation questionnaire available for free download. To learn more about the three software capabilities covered in this blog, watch the full webinar here.
Subscribe to our newsletter
Stay in the loop on product news, case studies, upcoming events and more.