Blog
3 ways demand-driven supply chains benefit from autonomous vehicles
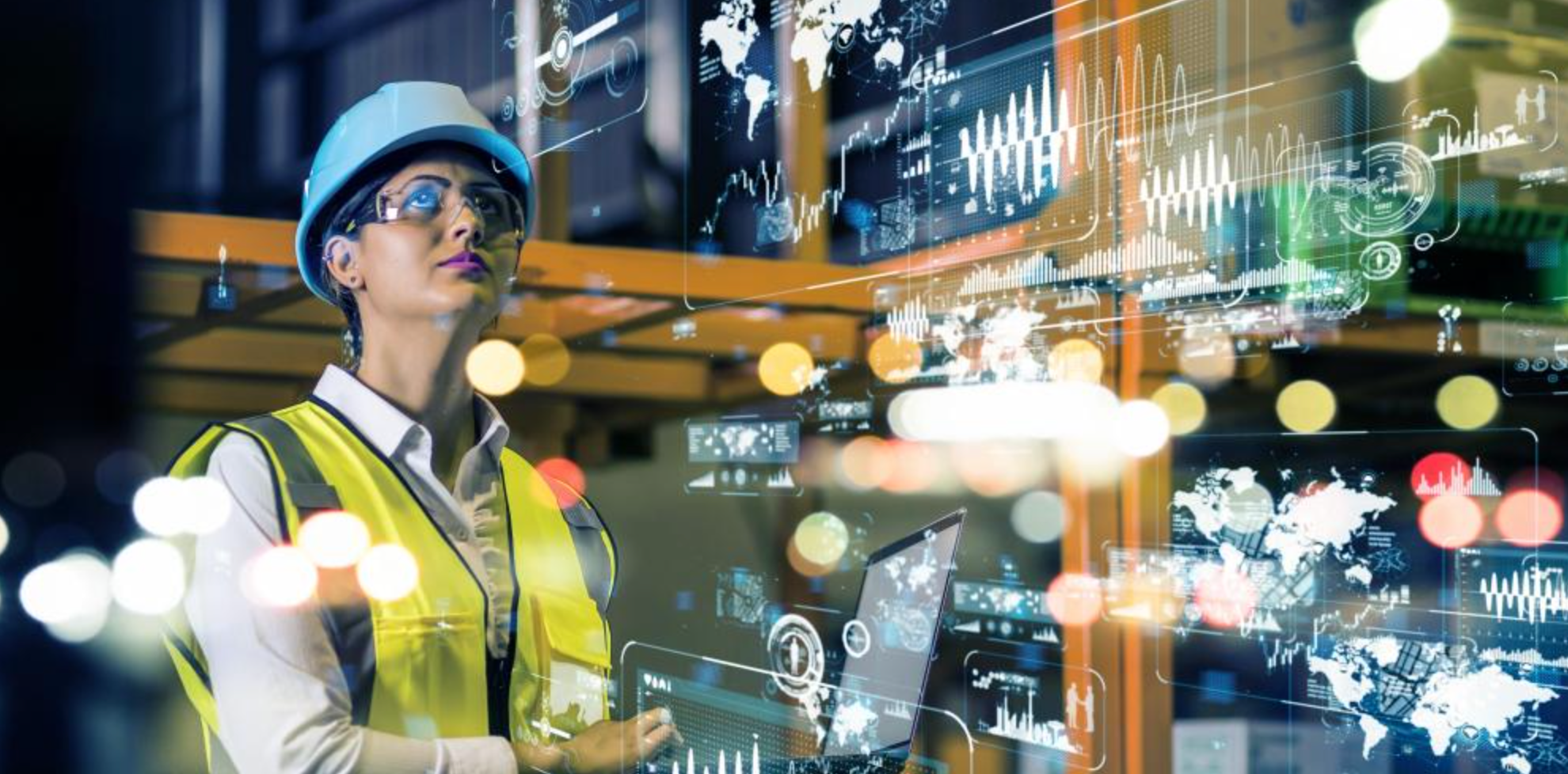
A demand-driven supply chain is flexible enough to respond to real-time signals. It supports fluctuating customer needs, and enables seamless warehouse communication in order to adapt to those changing customer needs on the line, in real-time.
A KPMG report cited the dangers of an inefficient demand-driven supply chain, referencing a company called Finish Line Inc. that could not process orders fast enough over the 2015 Christmas period, losing an estimated $32 million in sales and closing hundreds of its physical stores.
However, a demand-driven supply chain, with integrated autonomous mobile robot (AMR) technology, can help solve throughput inefficiencies by making supply chains more responsive to shifts in demand and customer expectations. Specifically, implementing AMR technology into the supply chain can bring numerous benefits, including:
1. Simplified material movement
When Gartner research named its supply chain trends to watch in 2019, it included an “autonomous things” category because of the benefits of autonomous vehicles, including their ability to move parts around a warehouse with no assistance or infrastructure while decreasing floor space and worker inefficiencies.
The OTTO 1500 is an autonomous vehicle that stores a map of its warehouse or factory in its memory and always knows its position through visual reference points. It can navigate around obstacles in real-time, unlike AGVs and conveyors.
A study by IQMS found that 76% of manufacturers prioritize improving floor productivity. This is because improving floor productivity has historically been difficult to do without increasing space requirements or the labor force size. However, at a GE Healthcare facility, the OTTO 1500 was able to simplify material movement, increasing productive floor space by 66%, without hiring additional personnel.
2. Increased supply chain efficiency
Many supply chains become inefficient by storing excess inventory. Companies can solve that problem and improve inventory management by using autonomous vehicles to replenish parts at assembly line stations on-demand.
A Ford Motors plant in Spain deployed an autonomous mobile robot that transports spare parts and as a result, saved up to 40 employee working hours without replacing any human jobs.
Ford Motors demonstrated “collaborative automation,” where robots support employees rather than replace them. This collaborative automation approach can also increase the amount of time that humans are able to do more rewarding and skilled tasks. While implementing AMR technology in factories and warehouses can increase supply chain efficiency in order to keep pace with competitors, it can also help companies appear to customers as innovative and forward-thinking.
The factory sells for us. It awes people who come to see it. It helps our sales organization close deals, because people see OTTO and immediately understand that Sunview is a forward-thinking, innovative company, and they want to do business with us.
Kurt Oberparleiter
VP of Operations, Sunview Patio Doors
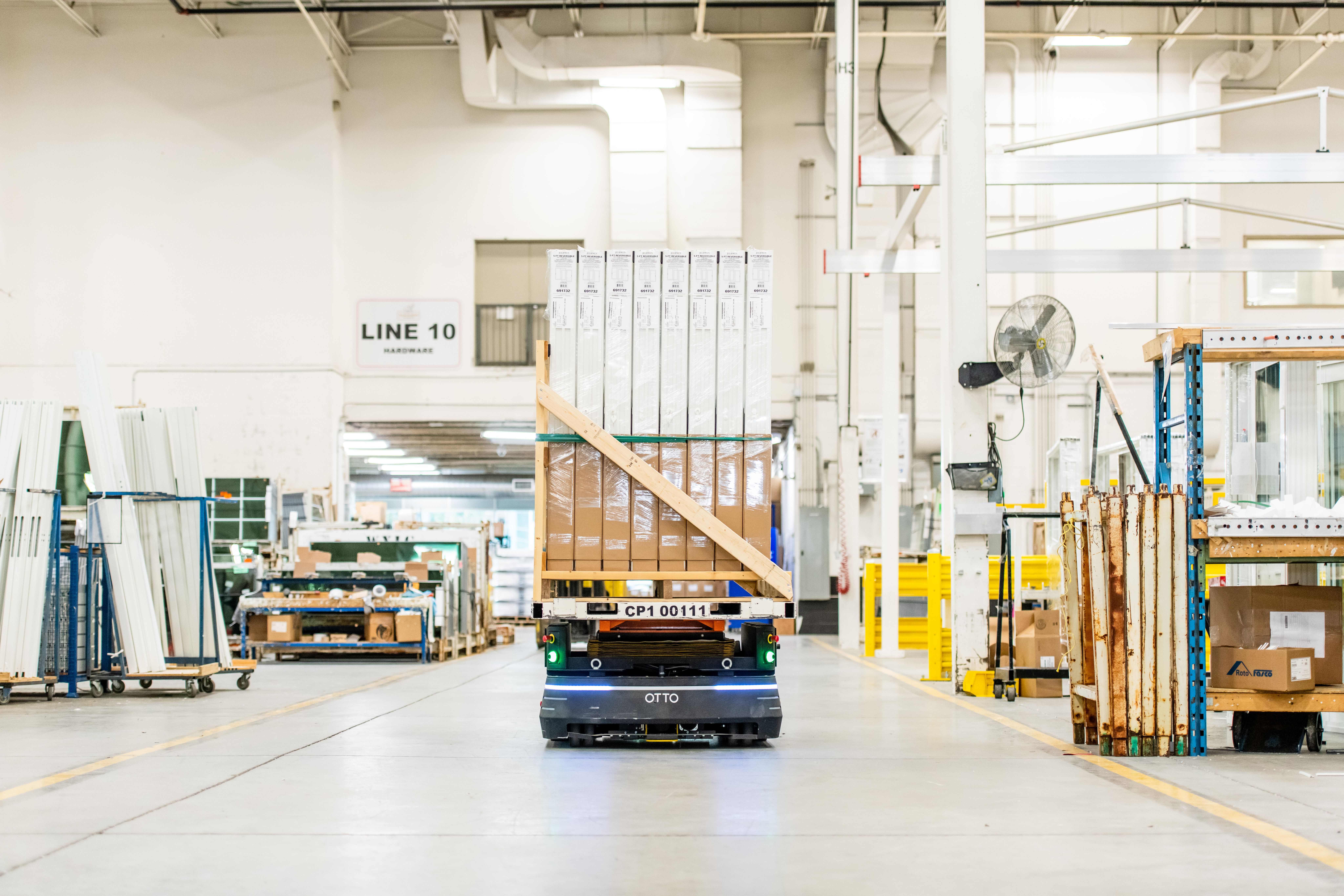
Image 1: OTTO at Sunview Patio Doors delivers finished goods to the warehouse, which frees humans to do more fulfilling work.
3. Better communication with other equipment
Some leading companies providing autonomous vehicles for supply chains offer APIs to facilitate communications between AMRs and factory equipment to streamline multistep processes.
A controller at the end of a packaging line can automatically summon a vehicle to transport goods, leaving humans free to do more value-added tasks. The API can connect to a warehouse management system (WMS) as well. This kind of connectivity can enable better information flow between machines and allow an entire facility to benefit from AMR technology.