Blog
Five key Industry 4.0 technologies
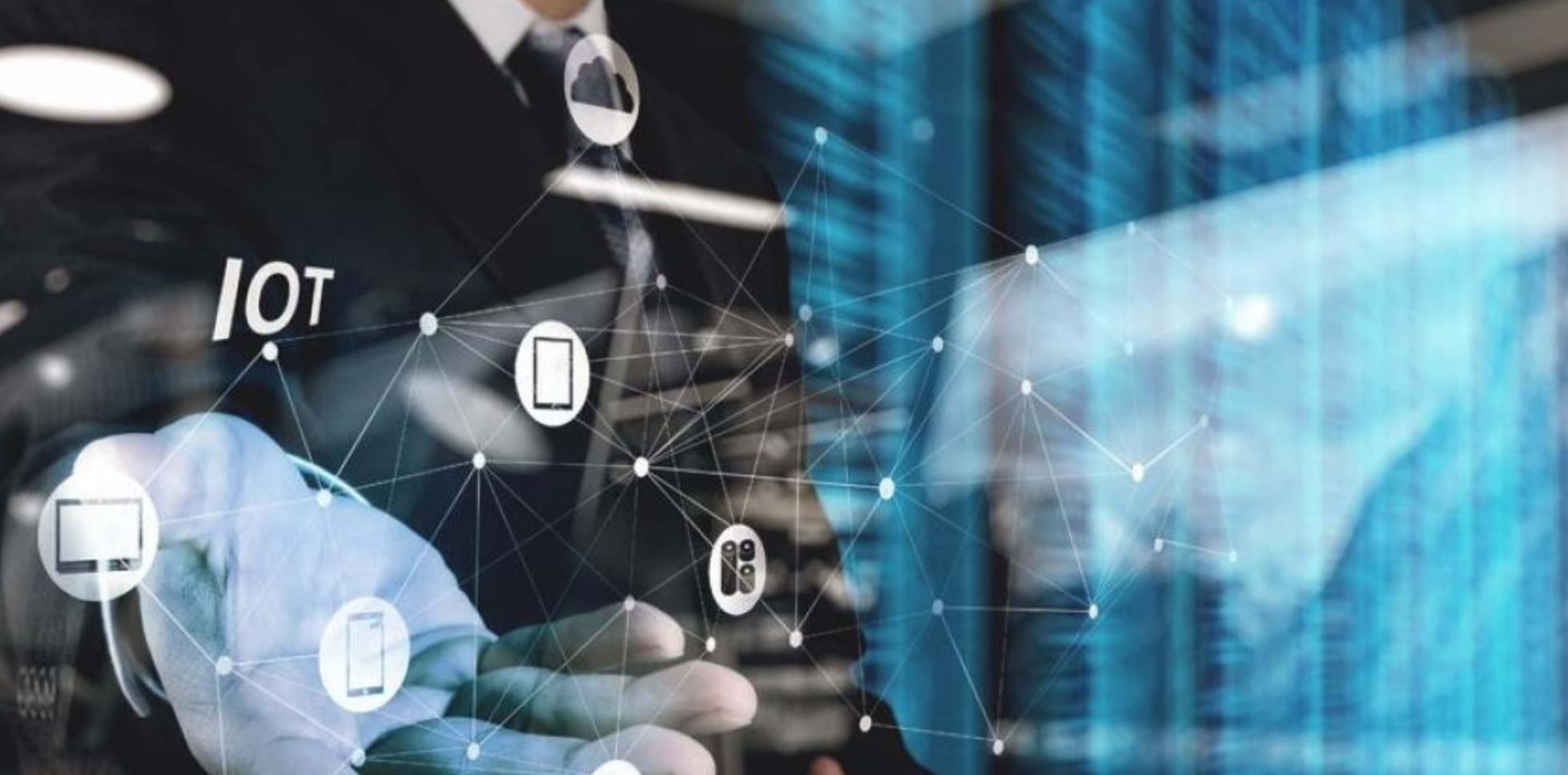
Originally posted via ARC Advisory Group.
New Industry 4.0 technologies, spanning mobile computing to cloud computing, have undergone vast development in the last decade and are now ready to be used as commercially available, interconnected systems within manufacturing – this is Industry 4.0. It holds the key to accessing real-time results and data that will catapult the industry into new levels of lean achievements.
The concept of Industry 4.0 however, is not a simple one. It envelops many technologies and is used in a variety of different contexts. There are five pieces that define Industry 4.0 at its core. Each piece is similar in nature but, when integrated together, create capability that has never before been possible. In an effort to understand Industry 4.0, the following five terms are explained as they contribute to the next industrial revolution:
1. Big data
As per Forbes, Big Data is a collection of data from traditional and digital sources inside and outside your company that represents a source for ongoing discovery and analysis. Today data is collected everywhere, from systems and sensors to mobile devices. The challenge is that the industry is still in the process of developing methods to best interpret data. It’s the evolution of Industry 4.0 that will change the way organizations and solutions within those organizations work together; teams will be able to make better, smarter decisions.
2. Smart factory
The concept of Smart Factory is the seamless connection of individual production steps, from planning stages to actuators in the field. In the near future, machinery and equipment will be able to improve processes through self-optimization; systems will autonomously adapt to the traffic profile and network environment. Autonomous Mobile Robots (AMRs), are an integral part of the Smart Factory, as their autonomous intelligence connects the factory together, allowing seamless operations.
Leading by example is the Siemens Electronic Works facility in Amberg, Germany. Smart machines coordinate production and global distribution or a built-to-order process involving roughly 1.6 billion components. When the Smart Factory is achieved, it will represent a pivotal shift for Industry 4.0, as the revolution will begin to roll out across multiple verticals. Various markets spanning healthcare to consumer goods will adapt Industry 4.0 technologies initially modelled in the Smart Factory.
3. Cyber physical systems
Cyber physical systems are integrations of computation, networking and physical processes. Computers and networks monitor and control physical processes with feedback loops; the physical system reacts, the system uses software to interpret actions and tracks results. The notion centers on computers and software being embedded in devices where the first use is not computation; rather it is a loop of action and machine learning.
4. Internet of Things (IoT)
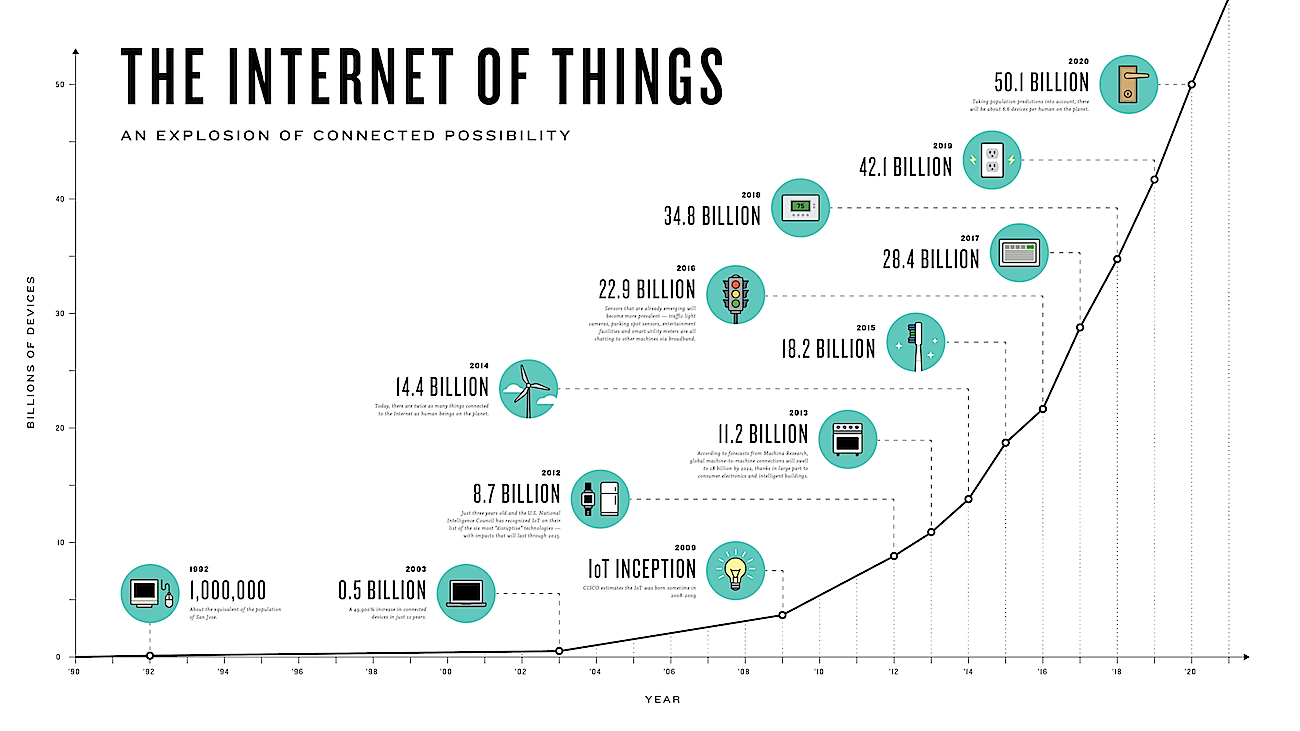
Photo credit: i-scoop.eu
The internet of things is a simple term for a grandiose concept. IoT is the connection of all devices to the internet and each other. As Wired said, “it’s built on cloud computing and networks of data-gather sensors; it’s mobile, virtual, and instantaneous connection.” This interconnection will enable “smart factories” to take shape as equipment will use data to manufacture, move, report and learn at astounding rates, efficiently. Click here to learn how the industrial IoT drives productivity in factories.
5. Interoperability
Interoperability is in essence what happens when we bring the above elements together. It is the connection of cyber-physical systems, humans and smart factories communicating with each other through the IoT. In doing so, manufacturing partners can effectively share information, error-free. Consider that no single company can dictate all its partners use the same software or standards for how the information is represented. Interoperability enables error-free transmission and translation.
From 3D prints to autonomous vehicles, Industry 4.0 technologies are propelling the manufacturing industry with new means of efficiency, accuracy and reliability. The level of intelligence offered today is only the beginning for what is to come.
The 5 factors of Industry 4.0 in practice
Autonomous mobile robots (AMRs) are a primary example of this technological evolution. Compared to their predecessors (autonomous guided vehicles), AMRs offer industrial centers increased flexibility and efficiency, higher throughput rates, and a faster return on investment. They move through plants with purpose, finding the most efficient route to their final destination by way of infrastructure-free navigation (no beacons, magnetic tape or cables). Onboard intelligence provides obstacle avoidance to ensure safe, collaborative work environments. Meanwhile, AMRs such as OTTO also offer intuitive light signals, much like vehicles on outdoor roads, to effectively communicate behaviors like turning, stopping, or parking. AMRs collect and share data from within the fleet, whether that fleet is used in one facility or many. Therefore, executives have visibility of real-time data and are able to make informed, educated decisions to positively impact KPIs and grow of their operation.
AMRs are only one example of how Industry 4.0 is going to transform the manufacturing sector. This industrial revolution will collect, use and share data so that industry can reach new heights in safety and efficiency, driving the sector closer to the ultimate goal of lights-out manufacturing.