Blog
AMA: Do autonomous forklifts have the same capabilities as manual forklifts?
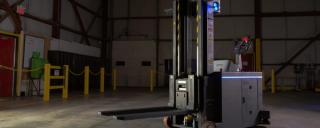
In this blog series, manufacturing facilities and warehouses ask their top industry and product questions, and OTTO’s material flow experts answer them.
Autonomous forklifts are a type of autonomous mobile robot (AMR) that are designed to improve safety, increase efficiency and help you reallocate skilled workers to more fulfilling roles. In order to accomplish this, autonomous forklifts such as OTTO Lifter have been designed similarly to manual forklifts that manufacturers have been using for centuries. However, autonomous forklifts can come with advanced capabilities and benefits that enable them to enhance operations inside a manufacturing facility.
Capabilities of manual and autonomous forklifts
Manual forklifts and autonomous forklifts such as OTTO Lifter share many similarities:
- Operates intelligently and flexibly: Manual forklifts are operated by workers that are capable of free navigation. Using a suite of sensors, OTTO Lifter can also make real-time decisions to navigate safely, even in the most dynamic facilities, unlike many automated guided vehicles (AGVs) that come to a full stop when their path is blocked.
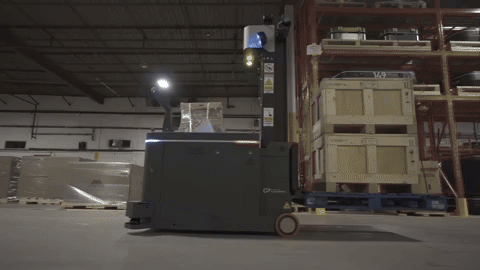
- Moves a variety of pallets: Just like manual forklifts, OTTO Lifter reliably assesses and picks up a variety of pallets, including wood and Grade A pallets such as CHEP, PECO, Block, and GMA Orbis HDMC 48-45.
- Detects stretch wrap and misplaced pallets: Using specialized sensors, OTTO Lifter can pick up pallets even when they are misplaced or wrapped in stretch film, just like a manual forklift operator.
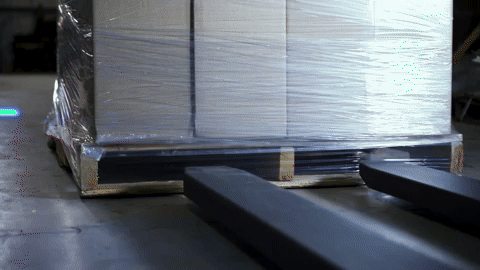
- Requires no infrastructure: Manual forklifts have no specific infrastructure required as they depend on human navigation. Similarly, OTTO Lifter relies on advanced sensors, including LiDARs, 3D cameras, and SLAM technology for real-time mapping and navigation, so it, too, doesn’t get lost in a facility. This enables OTTO Lifter to plan paths and avoid obstacles dynamically, making real-time decisions, just like humans.
- Performs various workflows: Manual forklifts and autonomous forklifts are well suited for similar workflows, including palletizer to stretch wrapper, stretch wrapper to storage, storage to outbound, inbound to storage, and creating or clearing staging lanes.
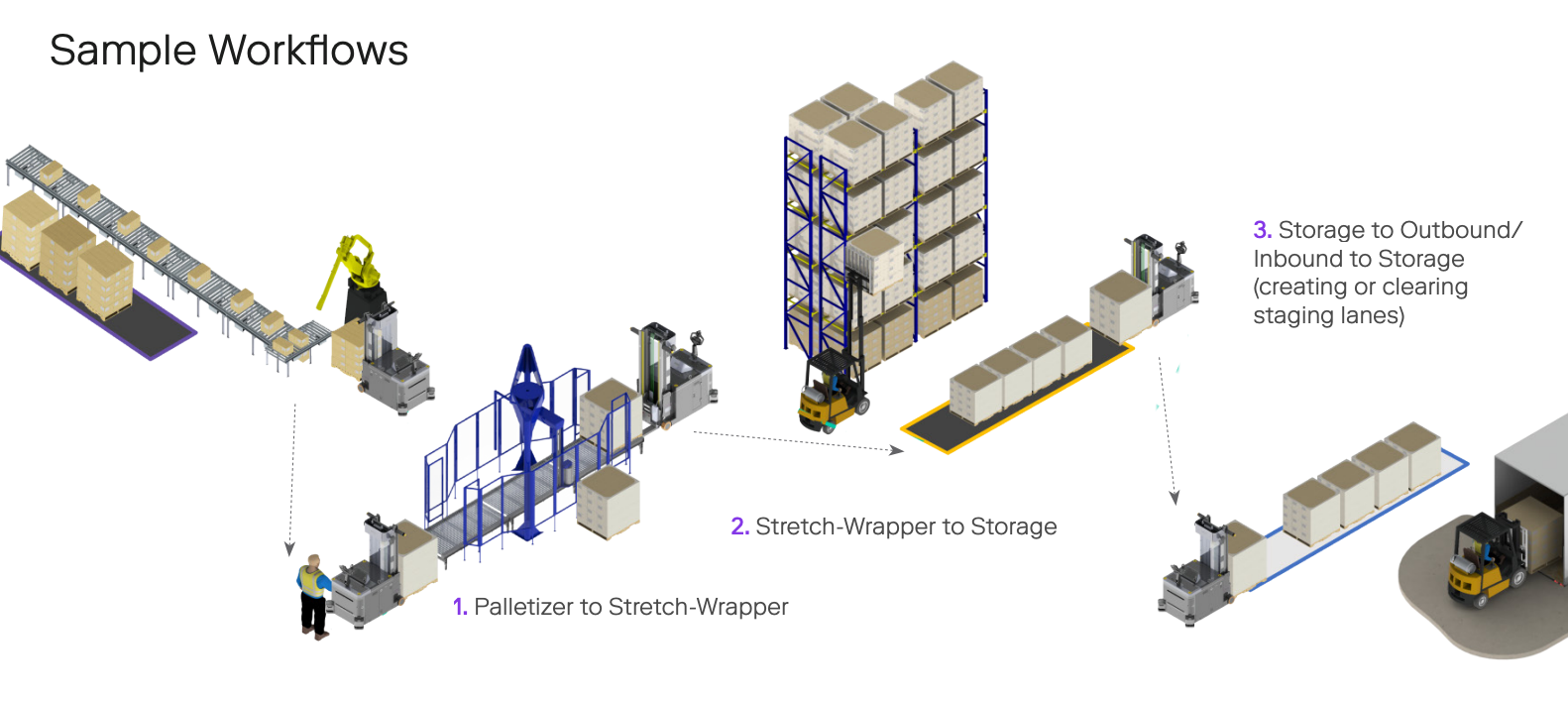
Benefits unlocked with autonomous forklifts
While autonomous forklifts and manual forklifts share many of the same capabilities, manual material handling can be dangerous. According to OSHA, there’s a 90% chance of a serious accident occurring during the 8-year average lifespan of a forklift.
Additionally, finding and retaining workers remains difficult amid the global labor shortage, where an estimated 2.4 million manufacturing jobs are going unfilled. The skilled workers that manufacturers are able to retain are not fulfilled doing manual material handling and instead should be redeployed to higher value-added tasks, enabling autonomous forklifts to handle the unsafe, repetitive task of material handling.
Autonomous forklifts such as OTTO Lifter have capabilities that are unique from manual forklifts to free up workers for safer tasks and deliver unmatched benefits.
- Offers autonomous and manual mode: OTTO Lifter offers a seamless transition between autonomous and manual mode, so operators can choose to control the robot manually with the tiller and return it to auto at any time.
- Scales easily: A new autonomous forklift can be added to the fleet with a click of a button. Since it will inherit configurations from your existing fleet, your new forklifts can be up and running on the first day, usually with no custom coding required. Multiple autonomous forklifts can be deployed and coordinated to work together efficiently within the fleet management software, enabling the operation to scale without a significant increase in supervision or management overhead. As the fleet grows, the existing fleet can be quickly reprogrammed or updated to handle new tasks, routes, or workflows for an optimized operation.
- Generates the most efficient route each time: OTTO Lifter will generate and follow the most efficient route to its destination, taking into consideration the “rules of the road,” blockages and congestion. The robots can be dynamically assigned tasks based on real-time needs, optimizing workflows and resource allocation.
- Enables data-driven decision making: The software managing OTTO Lifter provides real-time, reliable analytics through interactive dashboards that display data such as vehicle status, jobs in progress, and historical trends, enhancing your material flow
- Integrates with existing business management systems: OTTO Lifter integrates seamlessly with your MES and WMS systems via OTTO Fleet Manager, enabling jobs to be automatically assigned in real time. This ensures a unified, streamlined operation, reducing downtime and boosting overall productivity.
- Eliminates accidents: Autonomous forklifts do not suffer from fatigue or distraction, maintaining high safety standards. By performing repetitive tasks autonomously, OTTO Lifter reduces the risk of musculoskeletal injuries. Additionally, autonomous forklifts work productively without taking breaks or calling in sick, enabling 24/7 operations. By performing consistently and precisely, OTTO Lifter reduces errors and damage to goods that may result from human error.
- Reduces certification requirements: Autonomous forklifts eliminate the need for stringent operator training and certification required for manual forklifts, simplifying operations.
Once you understand the differences between an autonomous and manual forklift, you can begin to determine if an autonomous forklift is right for your facility. Watch the webinar “Transforming manual workflows with autonomous forklifts” to learn more about how leading manufacturers have deployed autonomous forklifts in their facilities and what to consider when evaluating autonomous forklifts.
Written by Poonam, Product Marketing Manager at OTTO by Rockwell Automation.
If you’d like to submit a question for our material flow experts to answer, please fill out the form below.
Ask a question
Subscribe to our newsletter
Stay in the loop on product news, case studies, upcoming events and more.