Blog
AMA: My AMR deployment has been designed. What’s next?
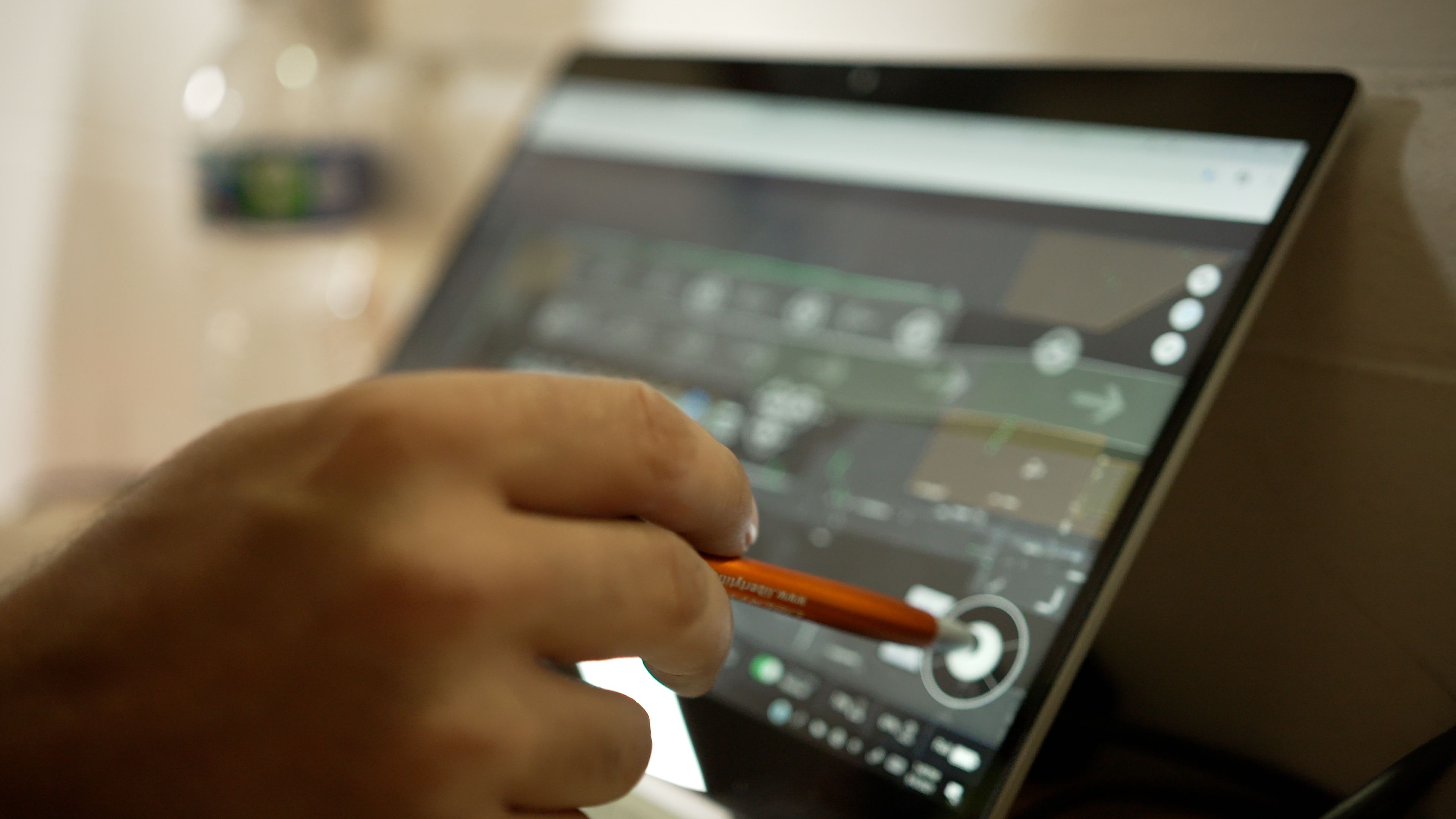
In this blog series, manufacturing facilities and warehouses ask their top industry and product questions, and OTTO’s material flow experts answer them.
This is the second blog in a two-part series about deploying AMRs. Read the first blog here or watch the full webinar here.
Deploying autonomous mobile robots (AMRs) is a complex process that requires thorough planning in advance to ensure the on-site deployment is smooth. Once the preliminary design, simulation, and detailed design have been completed, the next step is for the vendor to deploy the solution at your facility and support your deployment moving forward.
Deployment will go smoothly if you have selected an AMR vendor that has a thorough design process. This will ensure you feel comfortable using the system, confident in attaining ROI, and prepared to scale in the future. During deployment and support, ensure your vendor is considering the following six elements.
The 6 key elements in the AMR deployment and support phases
The deployment phase occurs once design is complete. In this stage, the AMR vendor will execute the thoroughly designed system at your facility and ensure your team is set up for success.
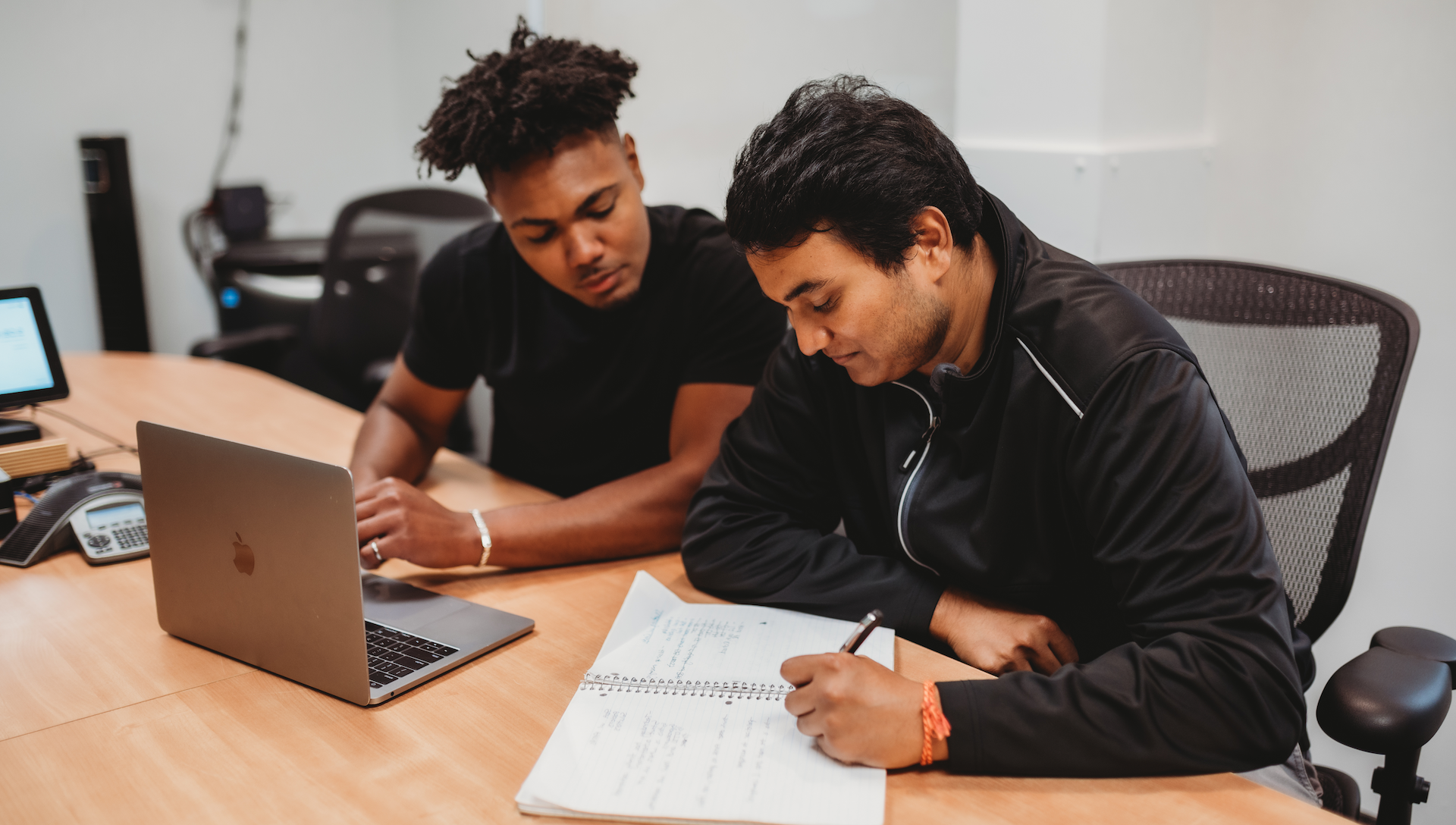
Image 1: Training and handoff is the last element of deployment, where your vendor will equip your operators with the skillsets they need to independently operate the deployment.
Deployment contains four key elements:
- System commissioning: Deployment begins with commissioning the system on site, including configuring the LiDAR fieldsets and robots, connecting the middleware platform to the fleet management system, verifying the full stack communication and more. Is the vendor verifying all endpoints and setting up the AMR network configuration? Will they test the safety stopping functionality on each piece of hardware? By being methodical here, you can reduce any potential rework and save time during deployment.
- Workflow testing: This is when the vendor will test each workflow and the movement of material between endpoints within the facility. Will they test docking accuracy at endpoints? Are they double checking the workstations, interlocks and middleware elements? Are the AMRs’ routes compliant with the map rules that were set up during design? Testing each element of the deployment on site ensures that what was designed remains efficient in the facility itself.
- Optimization and stabilization: This involves optimizing the designed workflows and stabilizing what could not be predicted and simulated during the design phase. Is the vendor fine tuning the map zones and traffic rules based on real-time interactions with the facility’s business management systems? Are they flexible enough to handle changes from what was simulated in design to what is accurate on site? Have they provided training and tools to optimize and stabilize the solution moving forward? The right level of detail in this stage will make it easy for you to add AMRs and workflows in the future.
- Training and hand off: This element includes equipping operators with the skillsets they need to independently operate the deployment. Is there proper and thorough documentation to refer back to? Are on-site staff prepared to recover the system from common challenges that can occur during operation? Do operators know how to capture the correct data to send back to the vendor’s remote support team in the case of larger fleet issues? This step empowers your team to independently operate the AMRs, ensuring they can use the system effortlessly every day.
TIP: Creating a test plan or checklist when commissioning the system will help guide you through this phase and minimize the rework required.
Once the system has been deployed, the project gets transitioned to the support team. Maintaining the fleet—big or small—doesn’t have to be stressful with the right vendor.
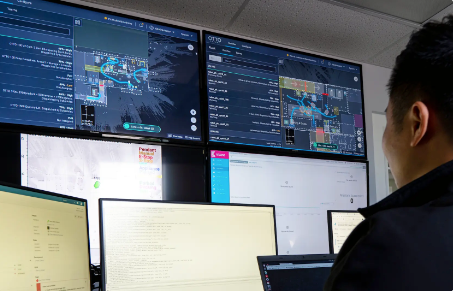
Image 2: An AMR vendor helping a customer monitor and support their project post-deployment to ensure it is performing as it should be.
Support contains two key elements:
- Monitor and support: The vendor’s support team should monitor the system remotely to ensure it is performing well and meeting KPIs. Does the vendor offer various plans post-implementation to offer the level of support you need? Is the vendor’s support team familiar with the facility, the deployment, and the customer’s operations team? Can the vendor share recent customer satisfaction metrics to provide proof of a positive customer experience? Some vendors will leave manufacturers without a maintenance plan, which can greatly hinder productivity. Look for a vendor that has a support plan that’s right for you.
- Updates and improvements: The vendor should support map and workflow improvements that can be implemented on the current software and identify the need for system updates based on requests from the customer. These requests should then be shared with their product team to consider implementing. This ensures the vendor is committed to helping the customer maximize productivity now and in the future.
TIP: Ensure your chosen vendor has a dedicated customer success manager (CSM) for your deployment at no additional cost. The CSM will proactively engage with you to ensure your ROI is maximized and your fleet is optimized.
Now equipped with the entire deployment process, from design through support, you can be better prepared for your own deployment and know what to look for when selecting a vendor. To learn more about the design stage, read the first blog in this series, or watch the full webinar, “Maximizing success: Best practices for an effective AMR deployment.”
To learn how thorough your shortlisted AMR vendors’ deployment processes are, download the checklist of which elements they should be considering during each phase of deployment.
Written by Abhinav, Systems Engineering Manager at OTTO by Rockwell Automation.
Download the checklist
Subscribe to our newsletter
Stay in the loop on product news, case studies, upcoming events and more.