Blog
AMA: Why is the design stage of an AMR deployment so crucial?
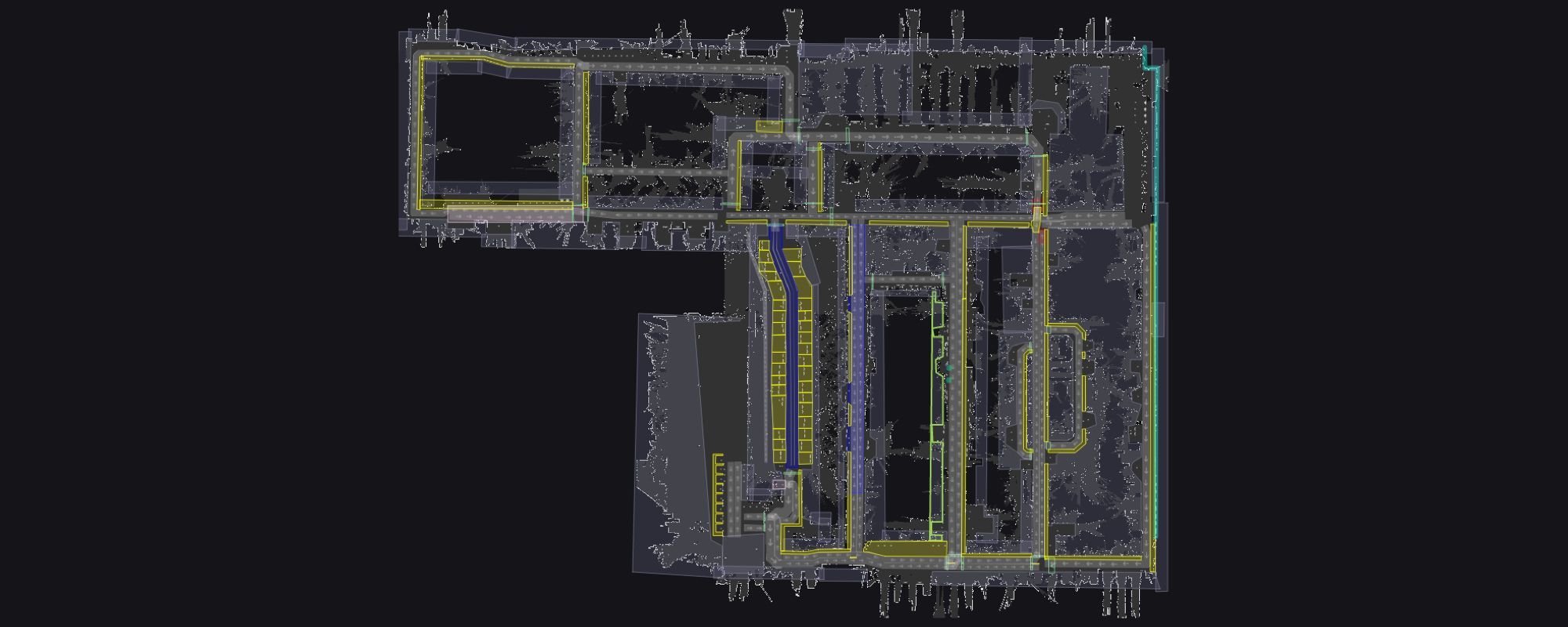
In this blog series, manufacturing facilities and warehouses ask their top industry and product questions, and OTTO’s material flow experts answer them.
This is the first blog in a two-part series about deploying AMRs. Read the second blog here or watch the full webinar here.
Prior to deploying autonomous mobile robots (AMRs) in your facility, manufacturers need to ensure they are set up for success to maximize ROI. By taking preemptive steps ahead of deployment, manufacturers can feel more confident, better prepared, and capable of training staff.
The key to a successful deployment is in the preparation. Manufacturers can set themselves up for success by establishing 8 key elements with their AMR vendor in the design stage.
The 8 key elements in the design stage of deployment
Preparing for deployment starts with creating a preliminary design. In this stage, the AMR vendor will focus on the key elements in the deployment to identify any major constraints in the facility layout or infrastructure.
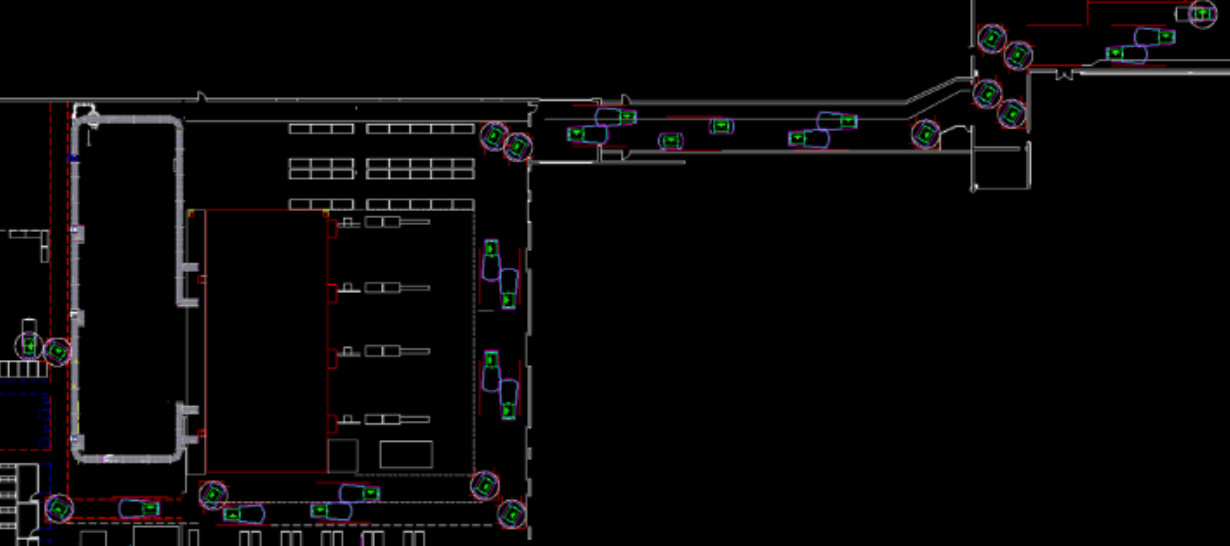
Image 1: A facility layout mapped during the preliminary design phase.
Preliminary design defines three key elements:
- Workflow and layout: This stage involves developing the initial facility layout with essential workflow factors in consideration. What materials need to be moved? Where will the AMRs pick up, drop off, park and charge? Which aisles will the AMRs travel through? How will the AMRs integrate with the facility’s MES/WMS systems and PLCs? At this stage, the AMR vendor will work with you to understand where and how the robots will interact with human-operated vehicles as well as other automated robots.
- Attachment and tooling: The goal of this stage is to identify the attachment best suited for your workflow and the tooling required to hold the payload in place. Sometimes, the attachment, payload and tooling have a larger footprint than the AMR itself. Your AMR vendor will perform a payload stability analysis and calculate the overall footprint, accounting for these parameters to the preliminary layout.
- IT requirements: AMRs have certain IT infrastructure requirements that must be set up during the design stage to ensure a successful deployment. This includes checking the bandwidth within the facility, VPN access to enable remote support and access to OTTO App UI.
TIP: Identifying any constraints in the facility and layout at this point is critical; poorly defined inputs will have a significant impact on the future elements within a project, such as the implementation timeline and throughput.
The next step is to validate your fleet size and ensure throughput requirements are met by simulating these preliminary design elements.
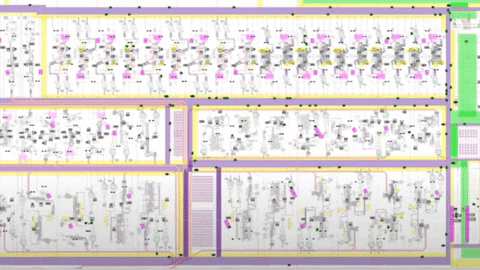
Video 1: A simulation test showing productivity at scale.
TIP: Ensure the simulations are continuously run throughout the detailed design stage below to improve upon the design and ensure the system is responding well.
Once the preliminary design elements have been validated, the AMR vendor will apply detail and accuracy in order to establish confidence in the designed system ahead of deployment.
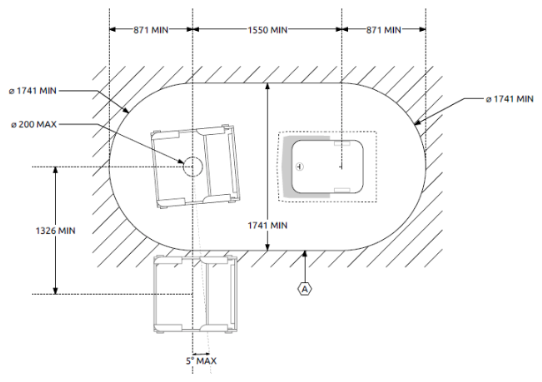
Image 2: Determining safety fieldsets based on attachment and payload footprint.
Detailed design defines five key elements:
- LiDAR fieldset and navigation specifications: Based on the footprint of both the attachment and payload measured in the preliminary design stage, the AMR vendor will establish exact LiDAR fieldsets and navigation specifications to define the safety parameters of the robot and the speeds at which they can go.
- Map and workflow: To produce accurate calculations, the AMR vendor will build a detailed visualization of the facility, layered with comprehensive map and workflow specifications. What are the “rules of the road” (such as single vehicle zones, exclusion zones and stop signs)? What types of jobs will the AMRs complete and how will they be dispatched? What are the docking parameters at each endpoint?
- Custom integration: To ensure the AMR solution can effectively communicate with your existing systems, custom integrations are designed at this stage with ease of use, robustness and scalability top of mind. Custom integrations can involve a range of solutions, including how to manage traffic integrations with external systems such as AGVs or AMRs from different suppliers.
- IT deployment: To ensure AMR deployment can begin on day one, IT deployment is completed during the detailed design stage. While IT requirements were defined in the preliminary design stage, this is the time to deploy the fleet manager, verify VPN access, verify data ingress and data egress, and set up LDAP authentication.
- Pre-site integration: In the case of high risk deployments, such as customized docking sequences, the AMR vendor may conduct pre-site integration testing to help save time and costs during onsite deployment.
TIP: Deployment of IT infrastructure must be completed before the robots can enter the facility to avoid losing time on site waiting for issues to be resolved.
By understanding all eight key elements that go into pre-deployment, you can be better prepared for your own deployment and know what design considerations to look for when selecting a vendor.
To learn more about the design stage, read the first blog in this series, or watch the full webinar, “Maximizing success: Best practices for an effective AMR deployment.”
To learn how thorough your shortlisted AMR vendors’ deployment processes are, download the checklist of which elements they should be considering during each phase of deployment.
Written by Abhinav, Systems Engineering Manager at OTTO by Rockwell Automation.
Download the checklist
Subscribe to our newsletter
Stay in the loop on product news, case studies, upcoming events and more.