Blog
AMA: Why should you implement autonomous mobile robots in your manufacturing facility?
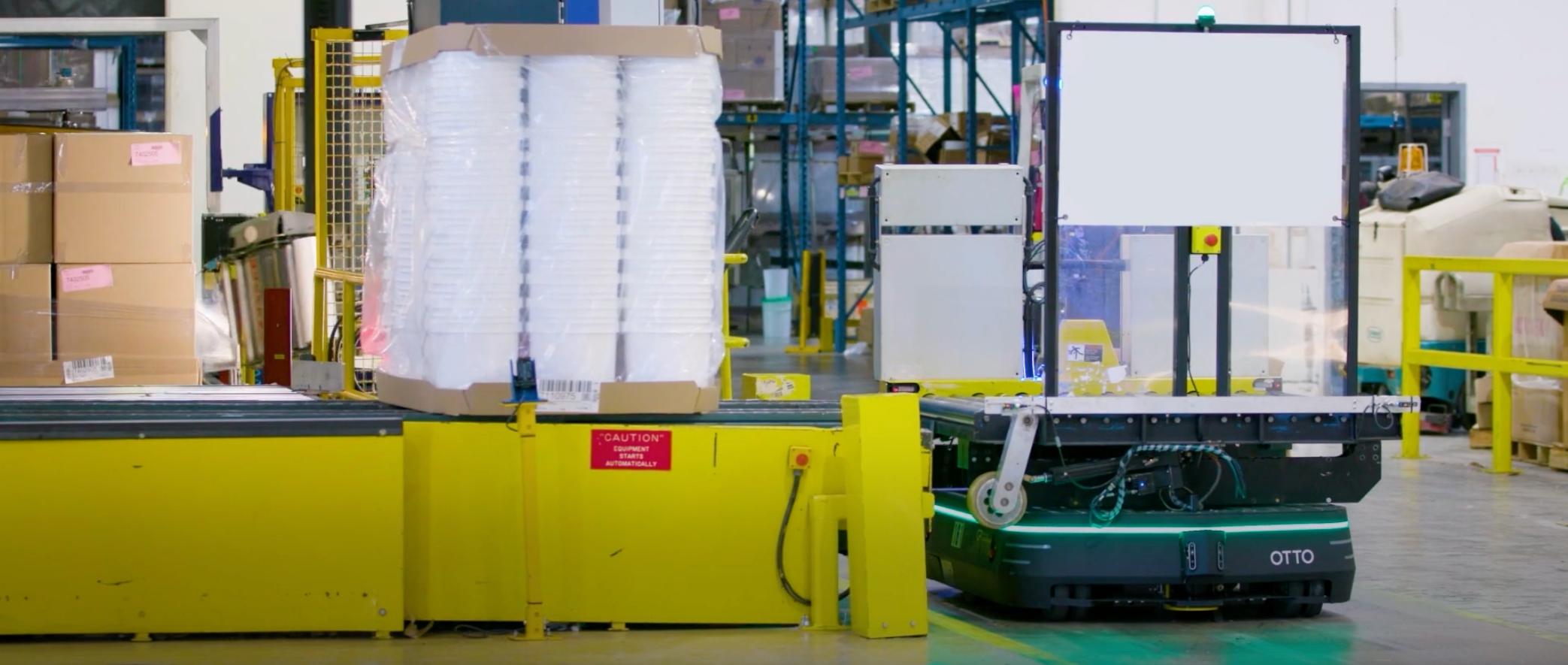
In this blog series, manufacturing facilities and warehouses ask their top industry and product questions, and OTTO’s material flow experts answer them.
Amid an increasingly competitive market and complex supply chain, manufacturers are facing more challenges than ever before, including safety, efficiency and labor shortages. To solve these challenges, manufacturers are turning to innovative autonomous material handling solutions, including autonomous mobile robots (AMRs).
Why should you implement AMRs in your manufacturing facility?
1. Improve safety
Manual material handling can be unsafe. According to OSHA, of all physical injuries in a workspace, 10% of them involve forklifts, and for a given manual forklift, there’s a 90% chance of it contributing to a serious accident during its eight-year average lifespan.
Manufacturers are solving this challenge by moving their materials with AMRs instead. Built with safety-rated LiDAR sensors and 3D depth sensing cameras, AMRs are designed to operate safely alongside people and other equipment.
When we introduced the OTTOs, we didn't have to worry about people getting hurt. For the last few years, it became apparent to us how important that was.
Dinesh Naidu
Plant Manager, Mauser Packaging Solutions
2. Increase efficiency and reduce costs
Material handling is one of the most inefficient processes in manufacturing facilities and warehouses, yet it is often overlooked. In fact, manual material handling can account for 87% of production time.
By switching to autonomous material handling solutions, manufacturers can increase efficiency and thus decrease costs. Equipped with real-time decision making intelligence, AMRs get to their destination using the most efficient, optimal route. For example, when Mauser Packaging Solutions implemented AMRs, they saw a 6x throughput increase.
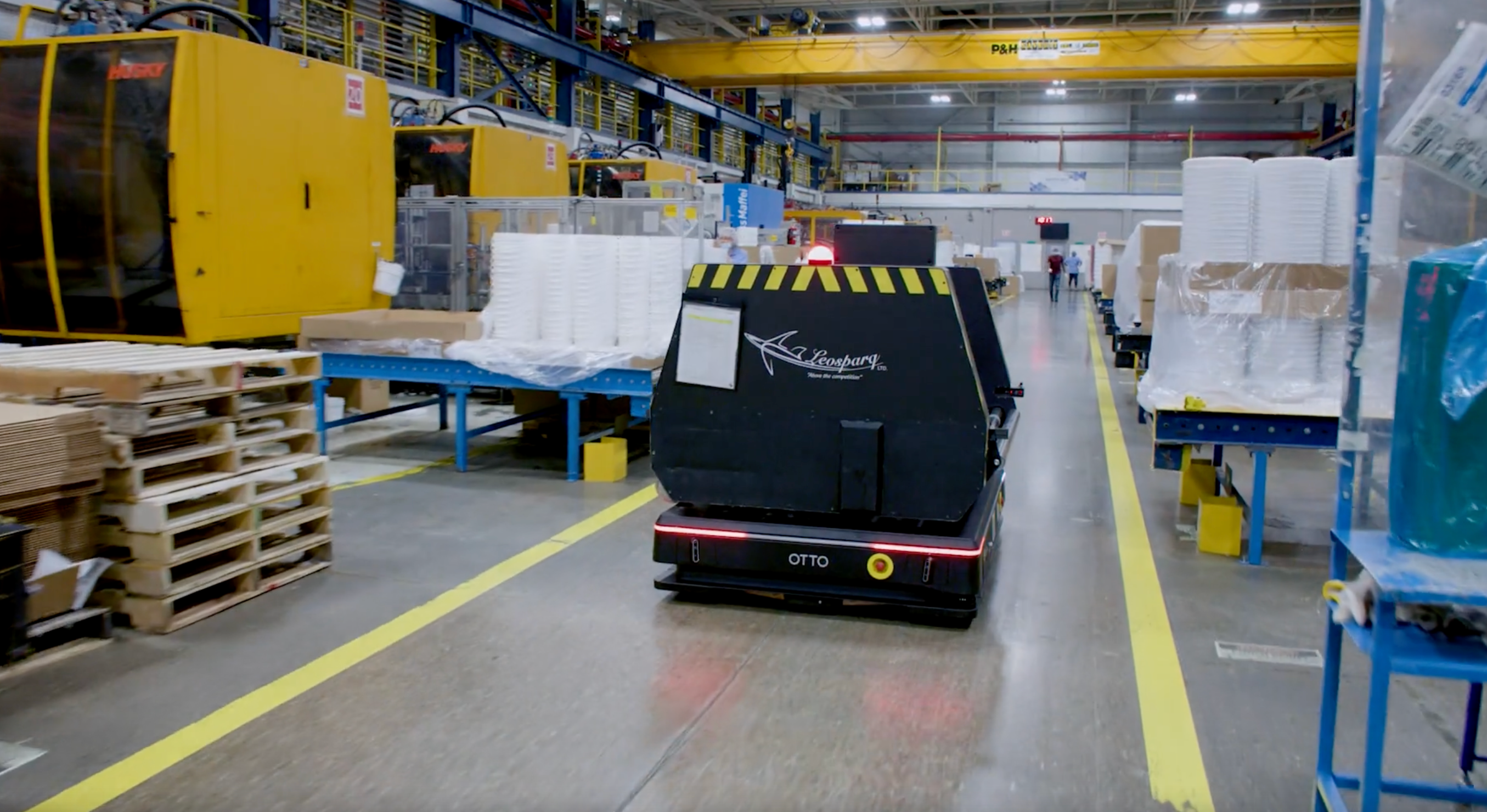
By increasing efficiency, AMRs help reduce manufacturing costs and generate rapid ROI. For example, GE Aerospace saved $1.3 million in the first year of implementation.
3. Improve flexibility and floor space utilization
Today’s factories are dynamic and need solutions that can adapt to consistent changes. AMRs offer unparalleled flexibility with the deepest integrations, enabling manufacturers to easily adapt to changes in processes, workflows and floor layouts.
Additionally, material handling can account for 55% of a factory floor, demonstrating the need for flexible solutions that use limited floor space. AMRs do not require any infrastructure to operate, unlike other material handling solutions such as conveyors and some AGVs. They operate completely autonomously by using existing infrastructure as points of reference for mapping their location. If an AMR encounters an obstacle, it can autonomously navigate around the blockage or generate a new route to its destination, unlike an AGV. For example, GE HealthCare was able to increase usable floor space by 66% when they implemented AMRs.
4. Reallocate labor to more fulfilling roles
Material handling can account for 25% of the workforce, which is especially challenging in the era of a global labor shortage. While 4.6 million new manufacturing jobs are projected to be created by 2028, 2.4 million of them could go unfilled.
By automating the dull, repetitive task of material handling with AMRs, manufacturers are able to reallocate the limited available labor into more fulfilling roles that better utilize uniquely human skills and often come with higher pay. For example, Mauser Packaging Solutions was also able to reallocate 3 laborers to higher-value work with AMRs.
AMRs have been disrupting the material handling industry for over fifty years. Increasingly, manufacturers are implementing this innovative technology to improve flexibility, efficiency, safety and usable floor space. By understanding the benefits of AMRs, manufacturers can make an informed decision to adopt the technology. If AMRs seem like the right solution for your facility, the next step is to understand which AMR is right for your operation.
Written by Poonam, Product Marketing Manager at OTTO.