Blog
Bringing robotics and people together in the supply chain

According to the 2023 MHI Industry Report, robotics and automation have become “table stakes for operations to remain competitive,” with the highest potential to disrupt the industry. With labor shortages cited as a top challenge for manufacturers today, manufacturing facilities and warehouses need both people and robotics working together.
Robots in the supply chain shouldn't replace workers, but rather augment their work. This middle-ground approach preserves jobs and the benefits go beyond that. As more facilities dive into automation, it's become evident that using robotics and people side-by-side provides the most profitable solution in its enhancements to supply chain safety, flexibility and efficiency.
Accounting for labor shortages
With over 2.4 million manufacturing jobs expected to go unfilled by 2028, many warehouses and manufacturing facilities are having difficulty finding labor. In fact, according to the 2023 MHI Annual Industry Report, companies cited “hiring and retaining qualified workers” and the global “talent shortage” as their top two challenges this year. Fulfillment centers and manufacturing facilities can make up for these labor shortages by employing robots alongside the few available workers they are able to hire.
As demand grows, companies need to produce more, but may not be able to find the additional workers to meet this rising demand, especially as we approach the holiday season. Without automation, these facilities would have to overwork their employees to meet their customers' needs. This is a challenge that has impaired companies for many years, with customer demands for faster response times, lower costs and service expectations ranking among the top cited company challenges across many MHI Industry Reports. If manufacturers employ robotics, on the other hand, they can supplement the work their employees are already doing.
Traditionally, supply chain companies have had to rely on seasonal workers to manage peak seasons. This approach may slow operations down due to the necessary onboarding for new workers or lack of available labor. Using robots to meet new demands instead can lead to a 20% reduction in operating costs while making work easier for current employees.
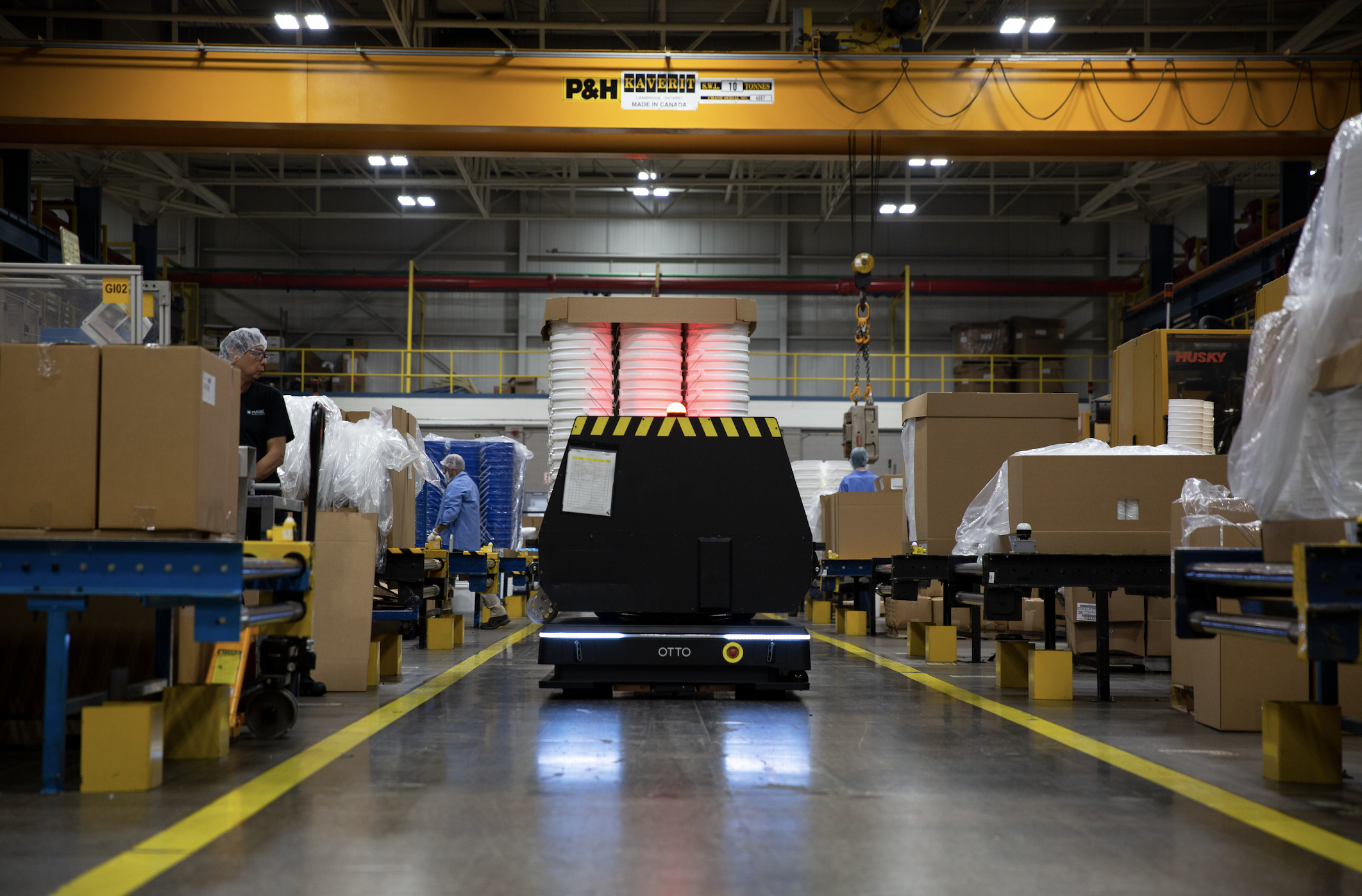
Image 1: OTTO AMRs increase productivity by allowing highly skilled laborers to transport materials from their workstations, without doing the dull and dangerous work of lifting and moving materials throughout the facility.
Maximizing skill sets
Given the advantages of automation, it may be tempting to pursue an entirely robotic workforce. As beneficial as this concept may seem, research suggests that robotics and people work best together. One of the most influential factors behind this is a robot’s limited capacity for uniquely human skills, including critical thinking, team work, creativity and more.
The jobs that robots fill include repetitive tasks like assembly, packaging, and rapid painting and welding. Needless to say, those are not the most desirable positions. But robots don't replace positions that require critical thinking and collaboration, which are often more rewarding.
Robotic Industries Association
Veo Robotics found that using robot-human collaboration halved the time workers alone needed for a task, and idle time was reduced by 85% when compared to all-human teams. When people and robots work side-by-side, they reach an ideal middle ground between speed and versatility. The unique skill set of workers and the efficiency of robots make up for any shortcomings on either side alone.
Robots in the supply chain should bring out the best in employees. The inverse is true of people. Together, they can create a better industry.