Blog
How leading CPG manufacturers have implemented AMRs to improve safety, flexibility and throughput
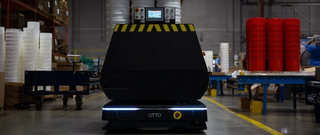
The CPG industry is characterized by constantly shifting demand and evolving consumer preferences, leading many manufacturers to consider automation solutions that prioritize flexibility and efficiency. To solve their most common challenges, CPG manufacturers are increasingly automating their material handling processes with autonomous mobile robots (AMRs).
Designed to improve material movement predictability, flexibility, and productivity, AMRs move a variety of material for CPG manufacturers, including cleaning supplies, plastic packaging, pet products, clothing, furniture and more. Download this infographic to learn which CPG workflows AMRs most commonly automate.
How 3 leading CPG manufacturers deployed AMRs to solve their top challenges
1. Improving safety for a Fortune 500 plastics packaging manufacturer
This $13 billion plastics packaging manufacturer deployed AMRs to reduce material handling costs, optimize floor space, and most importantly, enhance employee safety. With many employees nearing retirement, automation reduced the physically demanding tasks, boosting both employee retention and wellbeing.
The injection molding and decorating facility previously moved materials manually with carts and forklifts, but this caused safety and ergonomic risks, which led to the introduction of an autonomous forklift, OTTO Lifter. Watch the video below to see how OTTO Lifter automates the transport of packaging products from the palletizer to the stretch wrapper.
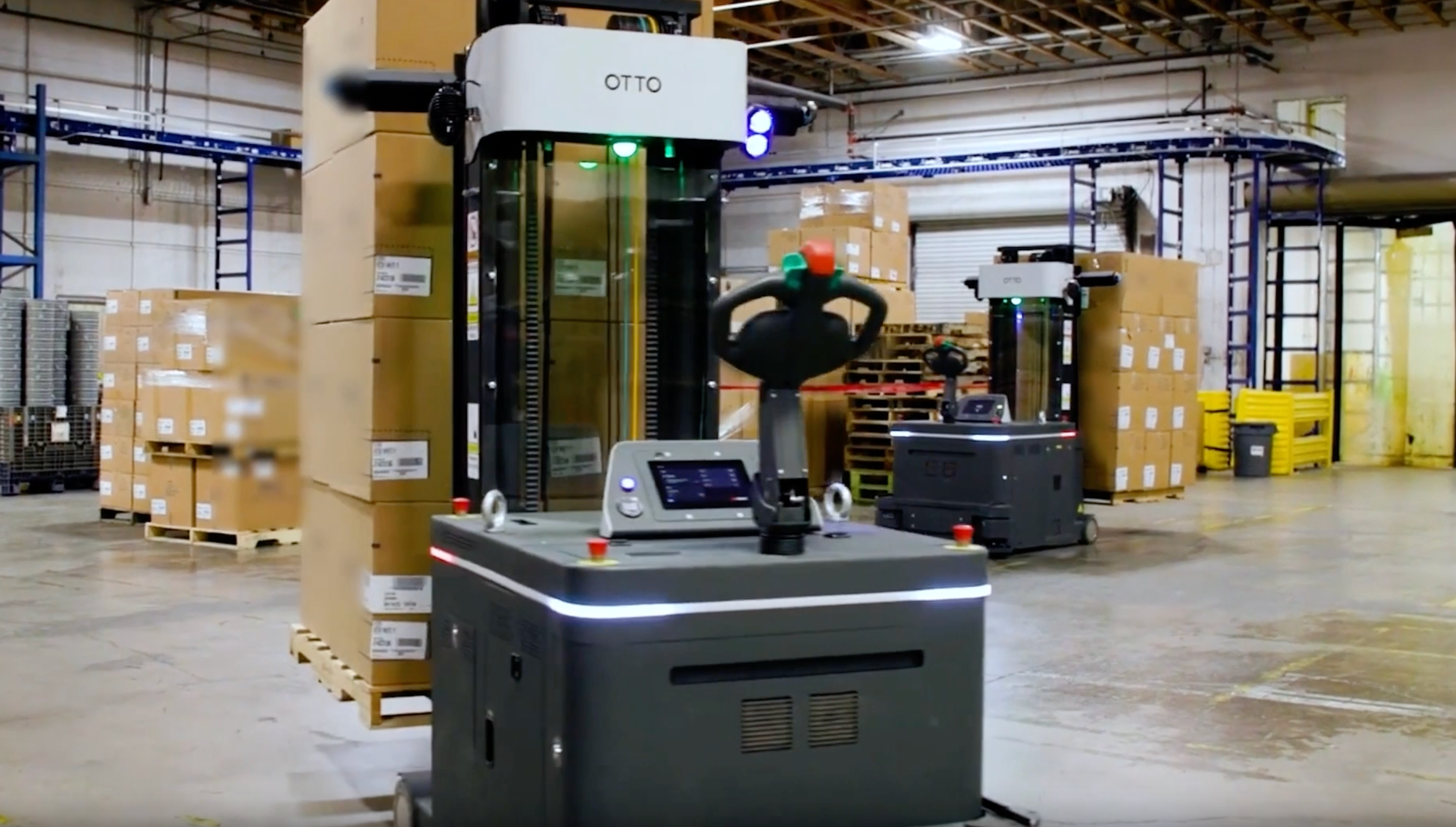
2. Increasing flexibility for a billion-dollar food and beverage manufacturer
With hundreds of facilities across North America, this Fortune 500 company is a household name in the food and beverage industry. Driven by labor force changes, increasing competition, and the need for operational stability, the manufacturer deployed flexible AMRs to manage the transport of raw materials and finished goods.
Today, 83 OTTO 100 AMRs have been deployed in two facilities spanning over 1.7 million square feet. Traveling over 1,100 miles and completing more than 5,200 missions per day, the solution is saving over $3 million every year while enhancing safety and boosting productivity.
3. Maximizing throughput for Mauser Packaging Solutions
Mauser Packaging Solutions is a global packaging leader with over 180 facilities worldwide. Looking to replace their automated guided vehicle (AGV) system which couldn’t deliver the uptime and throughput required for 24/7 production, Mauser turned to autonomous material handling with OTTO 1500.
Deployed at two facilities, the OTTO 1500 AMRs work safely alongside operators to move plastic containers from the conveyor to the stretch wrapper. In one facility, three workers were reassigned to higher-value tasks and safety was improved by eliminating two forklifts. The other facility was able to increase throughput by 6x.
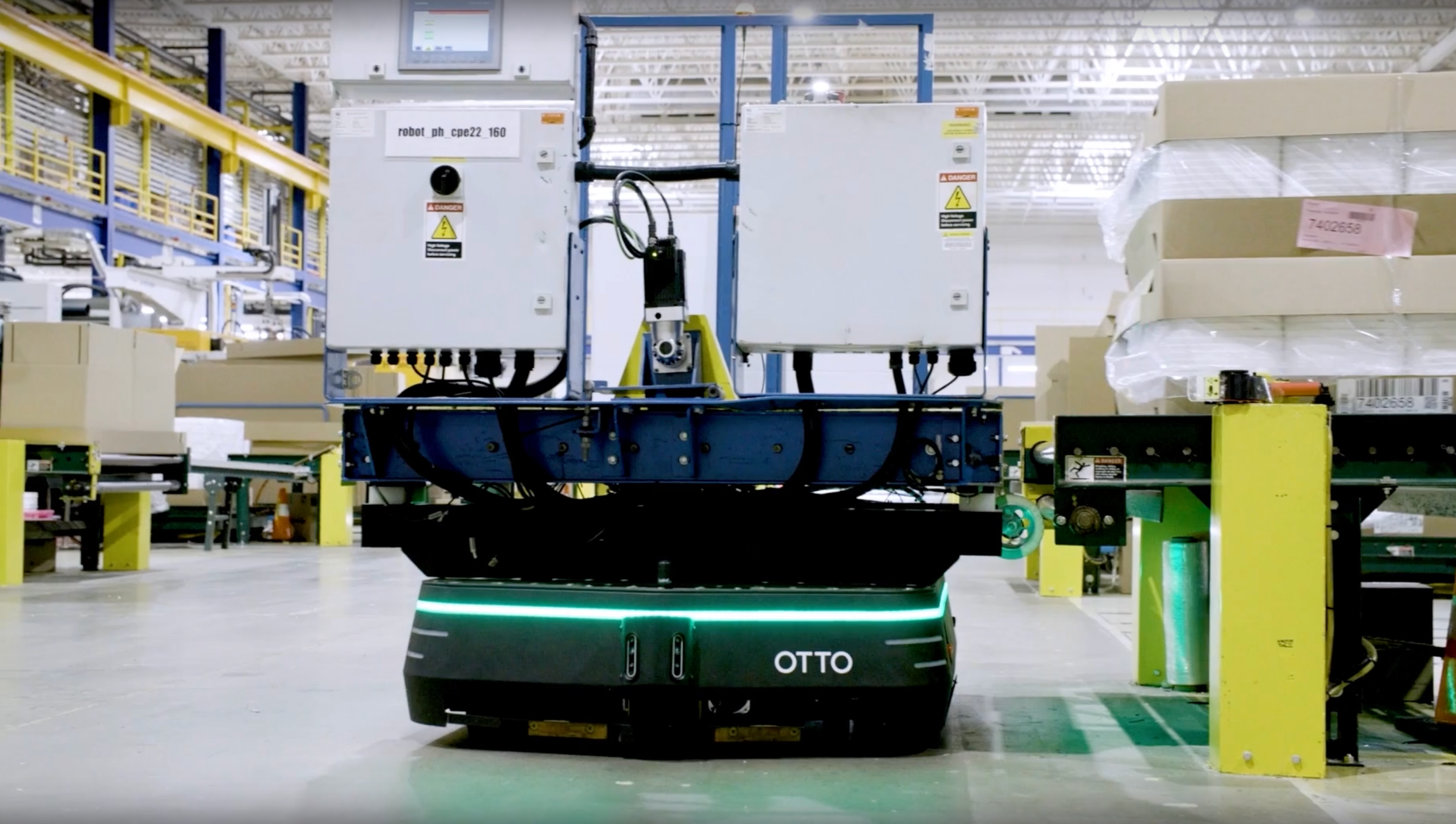
4 key AMR capabilities that enable CPG manufacturers to solve their top challenges
CPG manufacturers need an automation solution that can be tailored to solve their unique challenges. To ensure your AMR solution meets your facility’s goals now and in the future, there are four key capabilities to consider.
- Powerful software: While most AMR software solutions deliver standard autonomous driving and fleet management features, it’s advanced software that unlock next-level operational efficiency. Advanced software solutions enable scalability without sacrificing productivity, are capable of intelligent fleet orchestration, and have interactive dashboards that convert data into optimization opportunities. Use this questionnaire to help evaluate your shortlisted vendors’ software capabilities.
- Ease of getting started, scaling and modifying: While your chosen software needs to be advanced with many capabilities, it also needs to be equally user-friendly, even for first-time users. As your production lines change, your workflows may need to as well. The intuitive software should make it easy to set up and modify rules in different parts of the facility and to add new areas as you scale.
- End-to-end integration capabilities: Integrating your fleet with broader facility automation is essential to streamline material movement in your connected factory. The software you select should minimize programming overheads with pre-built APIs that empower your existing business management systems to trigger work instructions, and communicate with existing PLCs to optimize the payload transfers. It should also offer different ways to dispatch work to your fleet, provide performance insight and invite collaborations with other solutions and other vendors.
- Wide hardware portfolio to support your needs: Fixed automation solutions may only be able to move products with uniform dimensions. Choose an AMR provider with a wide range of payload capacities and attachments, capable of unlocking various workflows and moving unique payloads as your operations evolve.
To learn more about how leading CPG manufacturers are solving their most common challenges with safe, flexible and productive AMRs, watch the webinar “A practical guide to AMRs in CPG manufacturing.”
Subscribe to our newsletter
Stay in the loop on product news, case studies, upcoming events and more.