Blog
Optimize your AMR fleet for higher productivity with the latest software release
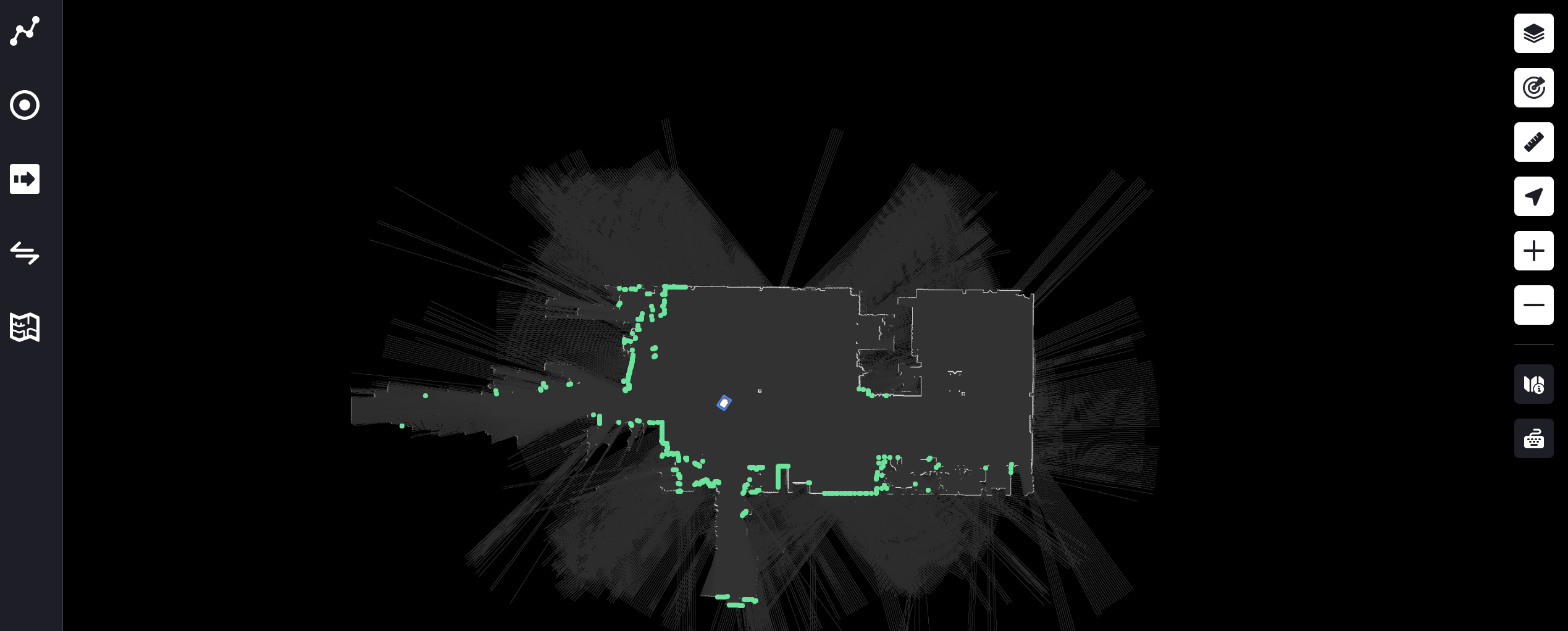
Automation is helping manufacturers turn the global labor crisis into a competitive advantage by removing waste from repetitive, dangerous, and unproductive tasks like material handling. Autonomous mobile robots (AMRs) are no longer buzz words in boardrooms. They are changing the face of factory floors by maximizing throughput, creating safer environments and redeploying humans to more fulfilling, value-added roles.
Unlike other pieces of common equipment including forklifts or production machinery, it’s the software behind the AMRs that makes the difference. OTTO Motors is focused on building the industry’s smartest AMR software to help manufacturers confidently automate more jobs in mission-critical operations at scale.
Our latest software release brings important enhancements to productivity, safety and usability within OTTO Fleet Manager.
At a glance:
1. Maximize output of large, multi-model AMR fleets with Team-Based Traffic Control
- Example 1: Reduced traffic congestion in tight spaces
- Example 2: Move more by creating high-speed zones
2. Reduce deployment time by 50% with new user-friendly facility integration interface
- New Facility Editing Interface for a user-friendly experience
- Launching Endpoints to save time in workflow set-up
3. VDA5050 standard compliance to support interoperability
Maximize output of large, multi-model AMR fleets with Team-Based Traffic Control
Effective traffic management is one the most crucial aspects of an AMR fleet deployment. It keeps the robots working and charged, avoiding traffic jams, blocked from reaching endpoints, or starving for work. As you automate more tasks and deploy multiple robots with different payload capacities and form factors, you also need a more nuanced traffic management system to get the most out of your AMR fleet.
In larger deployments, the same set of rules do not work for all the robots in your facility. For example, you may need to restrict routes for robots with overhangs to certain areas or avoid slopes for robots with sensitive payloads. Team-based Traffic Control enables users to create custom rules of the road for groups of different OTTO AMRs in the facility, resulting in reduced congestion and improving overall speed of traffic in large, heterogenous fleets.
OTTO Fleet Manager previously allowed users to group AMRs into teams for the purposes of allocating chargers and parking or assigning work. We expanded this concept in the new software update, enabling users to assign all map elements, including zones, lines and lanes, to teams. Users can now create multiple traffic plans in a single map and control traffic flow and robot behaviors based on team assignment.
Example 1: Reduced traffic congestion in tight spaces
As shown in the image below, consider a scenario where AMRs need to drive through a narrow corridor (marked with a green line) between two open areas. Even though the larger AMRs can fit in narrow aisles, they tend to drive carefully and slowly, reducing the speed of traffic. With the new software update, we asked: how can we deny the larger AMRs access to this corridor while permitting free access to the smaller AMRs so that they can drive though it at a higher speed?
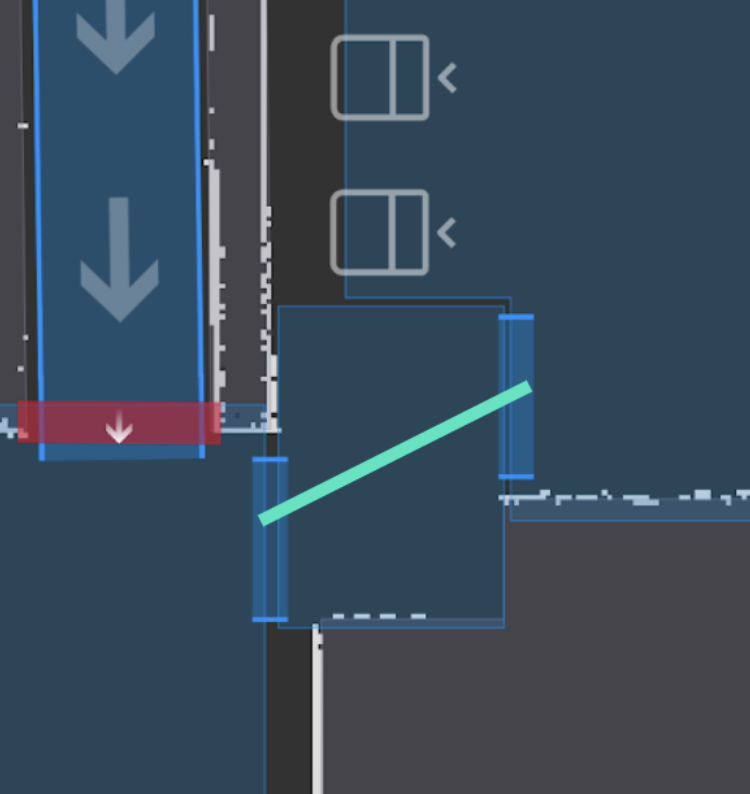
Image 1: The narrow corridor feature in OTTO Fleet Manager can reduce traffic congestion in tight spaces.
We can achieve this by creating an Assumed Cost Zone, and assigning it to “Team Heavy-Class AMRs” which represents all large AMRs, like OTTO Lifter and OTTO 1500. An Assumed Cost Zone, depicted by the green box in the image below, tells the robot that it is not allowed to navigate through this space.
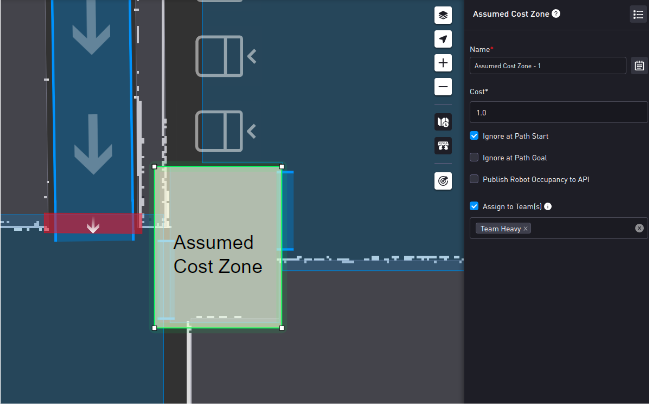
Image 2: The Assumed Cost Zone in OTTO Fleet Manager improves efficiency by blocking larger AMRs from entering the zone.
Example 2: Move more by creating high-speed zones
Consider a scenario where there are two Teams of AMRs: one with a high volume of traffic and the other with a low volume. In the latest software update, we asked: how can this traffic be kept organized and optimized for maximum throughput?

Image 3: The facility map in OTTO Fleet Manager with two lanes before implementing Team Based Traffic Control.
By applying Team Based Traffic Control tools to the layout shown in the image above, you would force the low volume AMRs to the lower lane, while allowing the high volume AMRs to use both the upper and lower lanes, when needed. By restricting low volume AMRs and creating a high-speed zone for high volume AMRs, the high volume AMRs remain unblocked and move faster.
New user-friendly facility integration interface reduces deployment time by 50%
The updated software release includes a refreshed and easy-to-use facility editing user interface (UI) within OTTO Fleet Manager, similar to the interface in OTTO App which was released in early 2021. Updates to the facility editing UI go beyond visual appeal and bring substantial improvements in usability and significant reduction in time to deploy. Our internal testing has shown that it takes a user 50% less time to set-up facility maps and new workflows compared to the previous versions.
The updated software involves two UI changes: a new facility editing interface and endpoints.
New facility editing interface for a user friendly experience
While our previous interface included all the functionality needed to create detailed and complex maps, users can now achieve the same benefits in less time and with less training. In the previous UI, users created the facility layout in one screen while navigating to another screen to create Places or Job Templates. With Places (logic) and Markers (x,y position) closely intertwined, users often had to jump back and forth, limiting productivity.
The image below shows the previous software with the many windows that the user had to navigate to, outlined in the red circle. The first tab, labeled Layout, brought the focus to the map itself and allowed editing. The other three tabs had the user working in the large left pane, unable to edit the map.
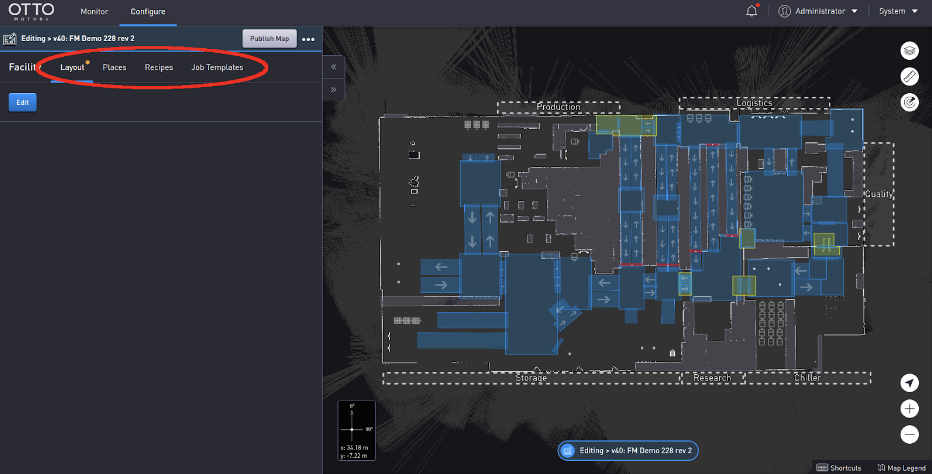
Image 4: The previous interface, with many windows that made editing the map difficult.
In the new software update, as shown in the image below, the functionalities are located near each other, creating a more intuitive and frictionless experience. The left bar provides easy access to all existing elements in the map and the top bar provides 1-click access to add new elements.
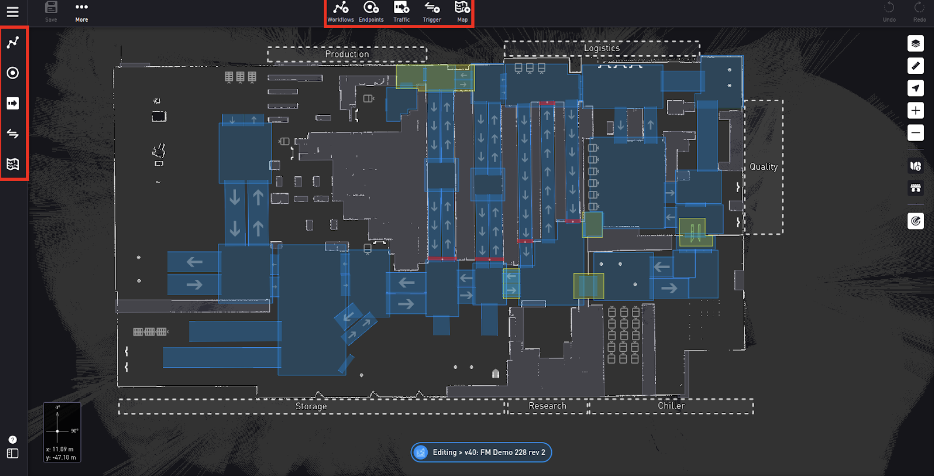
Image 5: The new software release enables a more intuitive and frictionless experience.
Launching Endpoints to save time in workflow set-up
In the previous interface, creation and editing facility maps required manipulation of three elements: Markers, Places, and Tasks, as described in Table 1.0. Let's say you want to set up a staging cart in your facility. In the old system, you would have to create the marker, then manually place and choose all the tasks and steps (and their settings) that a staging cart requires. In this software update, we asked: how can we simplify this set-up process and save time for our users? The answer is Endpoints.
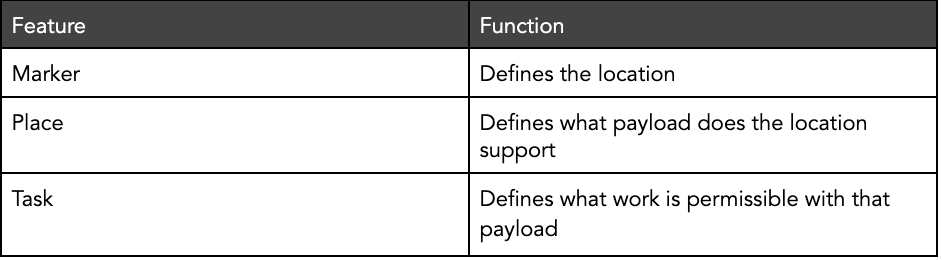
Table 1. Important feature names and functions that are commonly used in OTTO Fleet Manager.
Endpoints are a combination of a marker + place + tasks. Instead of having to create a marker, then create a place and set up its tasks - all you need to do is choose an Endpoint from a list of templates available in the Endpoint menu. With one click, a pallet, Staging Cart, or Custom Endpoint (e.g. OTTO 1500 Pick-and-Drop Stand) can be added to the map. Internal testing has shown a 63% reduction in clicks when creating these new Endpoints, ensuring a more efficient experience.
The example below shows the simplicity of creating a pallet endpoint using the new UI.
Video 1: Simplicity of creating a pallet endpoint using the new UI in software update.
VDA5050 standard compliance to support interoperability
Adoption of automation technologies is growing exponentially, but to reap full benefits of automation, manufacturers often need to deploy dissimilar technologies from different vendors. Interoperability is critical to seamlessly manage these different automation technologies, such as AGVs and AMRs.
To encourage this initiative, OTTO Motors became the first AMR vendor to support the well known AGV standard VDA5050, empowering customers to manage dissimilar types of material handling solutions from a third-party master controller interface. With VDA5050 compliance, all OTTO AMRs are now able to receive and follow orders to move, charge, dock, or activate their lift and conveyor attachments from third-party controllers.
Available and ready-to-use within our latest software update, VDA5050 expands the possibilities for safer and more productive human and technology collaboration. We have conducted tests to verify the VDA5050 support functionality by directing commands at OTTO AMRs from third-party controllers. One such test was conducted by Nvidia which showcased Nvidia's open source Mission Dispatch supporting OTTO AMRs out of the box because of the VDA5050 compatibility.
We showcased this capability in a demonstration with InOrbit where an OTTO 100 and an AGV were controlled by InOrbit’s master controller. Instead of controlling an OTTO AMR with OTTO Fleet Manager, InOrbit is able to issue commands through its own platform because of VDA5050. This opens the possibilities for an easy integration with your existing automation material handling systems like AGVs.
As the sixth software release in the past three years, OTTO Motors is continuously evolving its software suite to make material handling operations more productive, safe and easy-to-use. For detailed information about the OTTO software suite, AMRs and attachments, visit OTTO Technical Documentation. If you’d like to learn more about the OTTO AMR fleet, register for the webinar below to help assess which robot is right for your material handling needs.