Blog
The power of sophisticated middleware in creating a connected factory
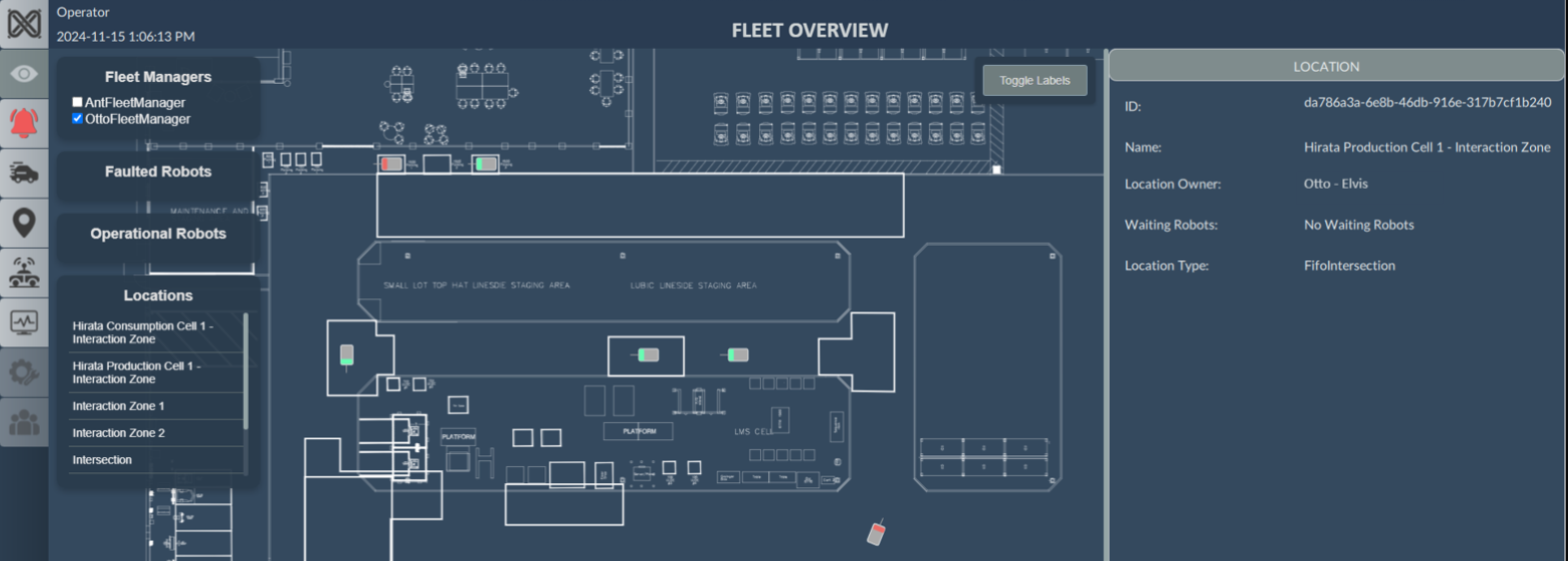
Manufacturing facilities need to move as much material as possible, while being flexible to changes in demand, resources, and processes. However, some facilities increasingly struggle to maintain flexibility while managing isolated automation systems, leading to inefficiencies and increased costs.
Industry 4.0 technologies can bridge these gaps, but many facilities lack the technical skills to adapt to the complexities of programming languages and communication protocols. This lack of flexibility hinders product changes and slows response times, often leading companies to hire more staff and incur high retooling expenses, leaving them unable to scale efficiently.
This is where middleware becomes essential, connecting isolated systems into an integrated ecosystem and enabling customers to fully leverage their automation investments.
How sophisticated middleware transforms isolated automation systems into integrated ecosystems
Middleware solutions are designed to seamlessly integrate intralogistics automation into manufacturing facilities, helping manufacturers streamline operations, reduce costs, and maximize ROI.
Middleware bridges the gap between disjointed systems, driving operational efficiency by focusing on three main pillars of interoperability:
- Operational Technology (OT) Interoperability—Seamlessly integrate diverse operational technologies, such as PLCs, robot cells, hoists, conveyors, AGVs, line controllers, HMI screens, Andon boards, and other OT equipment.
- Enterprise Interoperability—Connect business systems like QMS, ERP, MES, WMS, WCS, and WES to a central hub, allowing them to publish or subscribe to data. From there, the data is aggregated in the middleware to create rules and drive actions.
- Mixed Fleets Interoperability—Manage traffic, inventory, and mission dispatching across AMRs, manual traffic, and other logistics automation, all on a unified platform.
When multiple APIs from different vendors are interacting in the same facility, seamless integration can be a challenge. Even if each API is easy to use on its own, differences in terminology and data structures where they interact can require costly custom coding, which adds time and complexity to integrations. Middleware overcomes this challenge by unifying APIs into a common framework, using plugins to translate data into a format each system can understand. This eliminates the need for custom coding and ensures systems work together efficiently, driving operational improvements and delivering value faster.
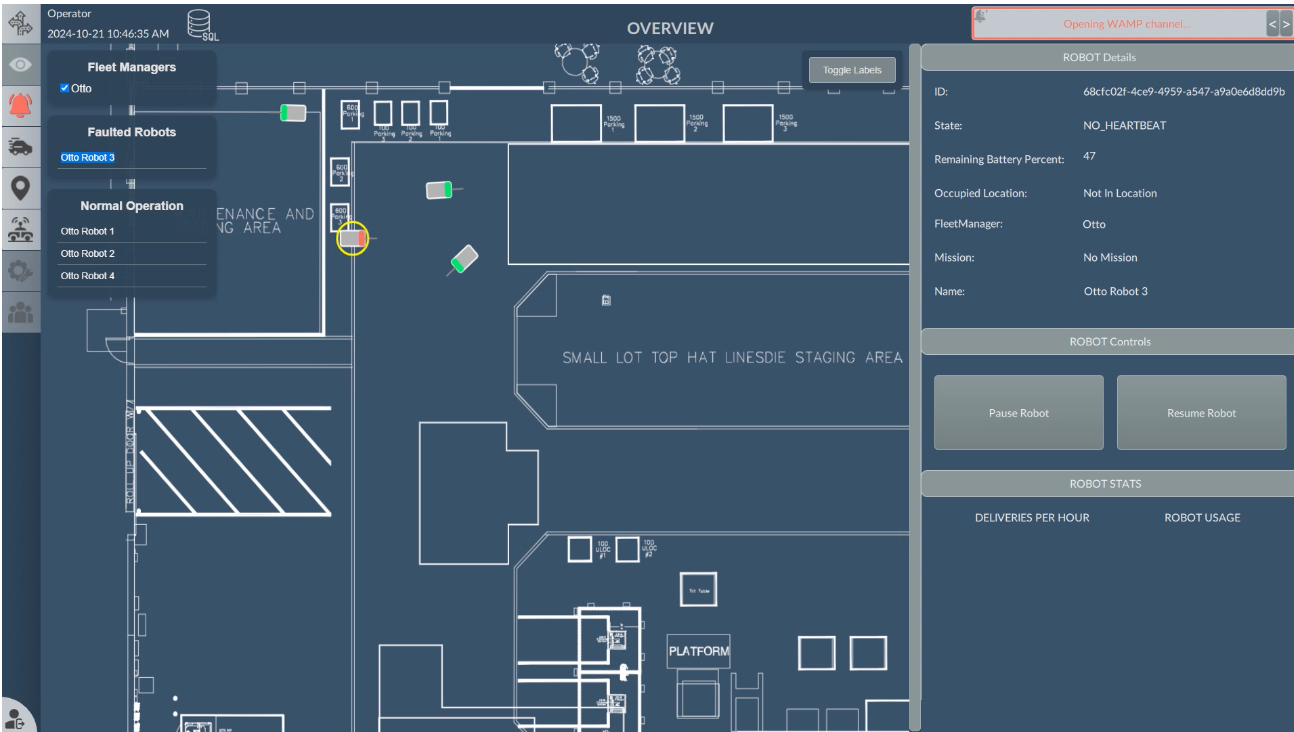
Video 1: In this example middleware software, users can select robots across their mixed fleet to view status, or pause/resume the robot as needed. Additionally, independent fleets can be toggled to focus on a specific supplier.
Additionally, traditional intralogistics solutions often create “black-box” solutions that restrict integration with other technologies. Sophisticated middleware overcomes these limitations by supporting both legacy and new systems, allowing any individual component to be upgraded, replaced, added or removed without disrupting existing relationships and efficiencies. By centralizing control of diverse automation technologies, middleware improves resource utilization and control, allowing manufacturers to scale with confidence.
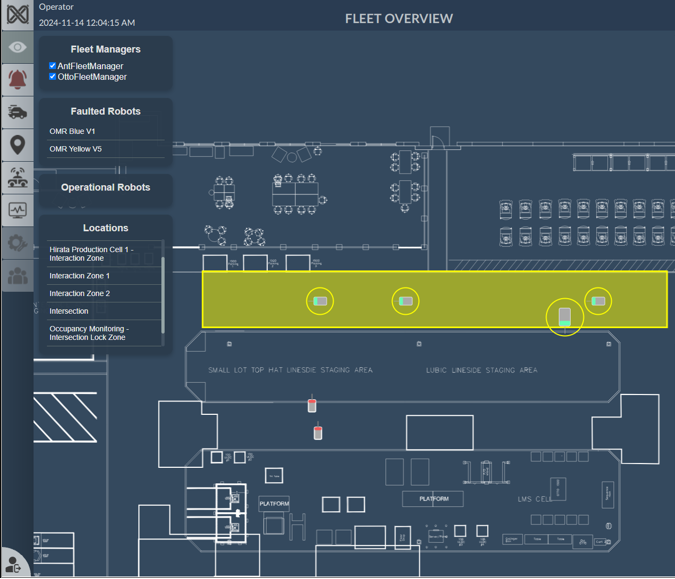
Image 1: "Proximity Zones,” as shown above in this example middleware software, are designed for high-traffic areas where mixed fleets share larger spaces with less predictable traffic flow. A “Proximity Zone” ensures that when the flow of traffic becomes impeded—whether due to another vehicle servicing a work location or an emergency situation—all units properly wait their turn instead of trying to circumvent the obstruction. This creates predictable and repeatable traffic interactions, improving productivity.
By deploying an advanced middleware solution like NEXIA, manufacturers can streamline the deployment of a complete factory system, reducing implementation time from years to just months. NEXIA’s low code/no code configuration empowers employees to manage system changes without specialized programming skills, alleviating staffing pressures and reducing complexity. The platform minimizes system dependencies, ensuring plant upgrades have minimal impact on operations and allowing staff to focus on high-value tasks. Built utilizing over three years of proven success deploying some of the largest and most complex systems in North America, NEXIA helps manufacturers cut planning time for upgrades and integrations by over 40%, and achieve a 20% faster ROI by dynamically adapting automation to real-time data.
Contact us today to discover how NEXIA can help you integrate, simplify, and optimize your automation, unlocking the potential for greater efficiency and growth.
Subscribe to our newsletter
Stay in the loop on product news, case studies, upcoming events and more.