Blog
Seeing is believing: Simulating AMRs for successful deployments
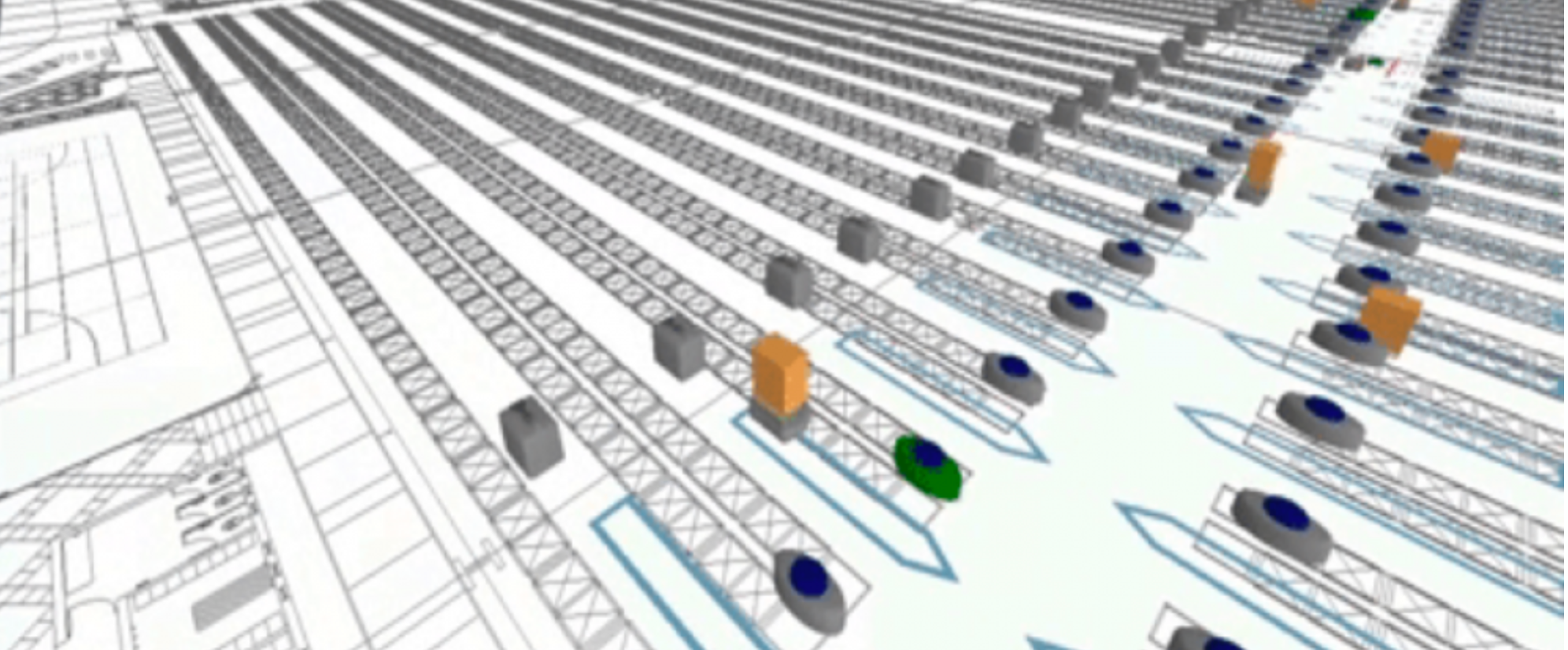
You wouldn’t ask an architect to build anything without designing it in AutoCAD first, so why are you installing AMRs without simulating the deployment first in software? In this post, Bonnie Yue, Simulation Services Manager, shares how our simulation services can help you reduce costs, validate feasibility, mitigate risk, and evaluate ROI — all before the robots are on-site at your facility.
We believe that successful solutions start with the end in mind. The earlier you can visualize what the end looks like and plan for the path to get there, the more successful you’ll be. As the Simulation Services Manager at OTTO Motors, I work directly with our customers using our simulation tools to help them build out that vision, and accelerate their return on investment.
What to consider when planning a large AMR deployment
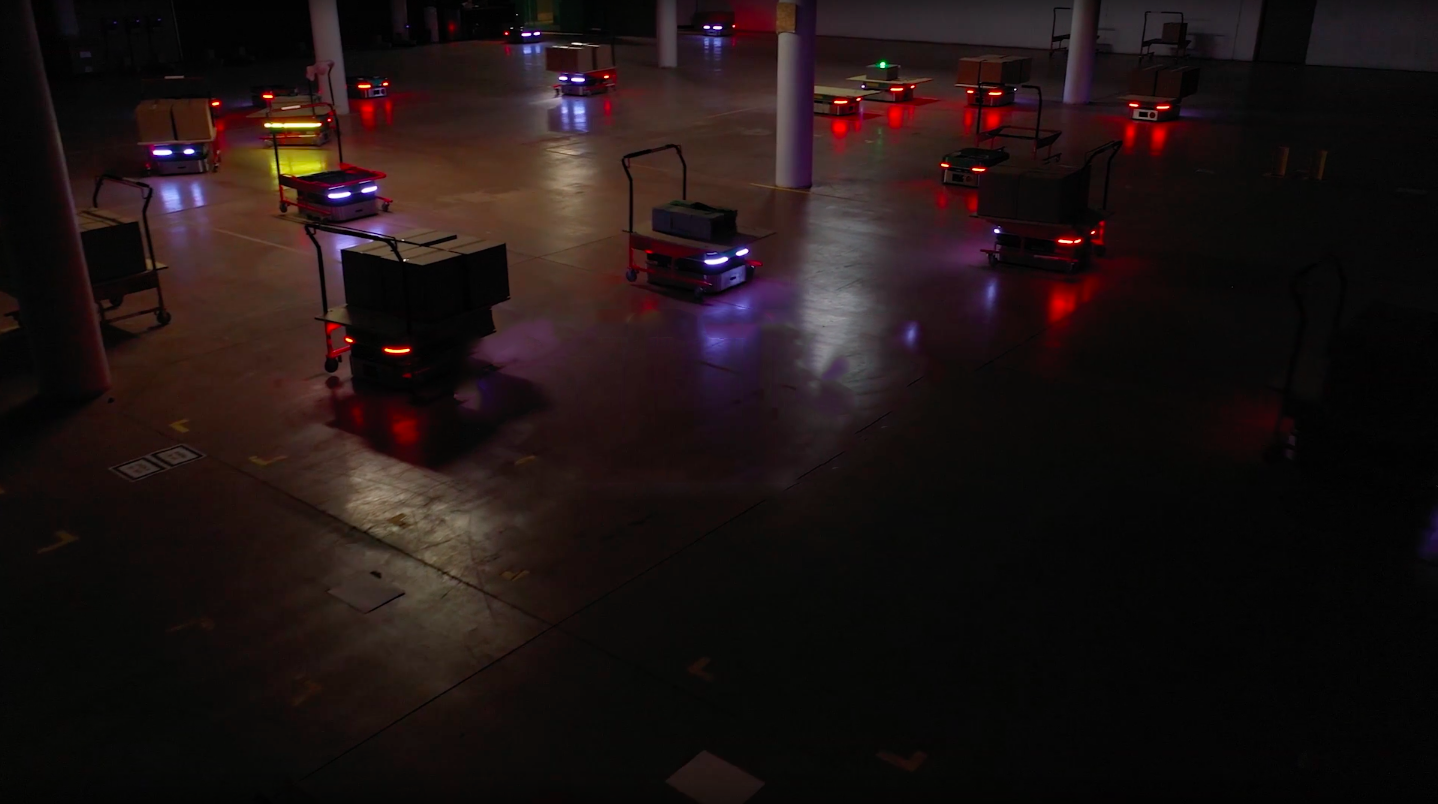
Large OTTO 100 AMR deployment.
Successfully deploying large fleets of autonomous robots requires careful planning and designing. There is typically a lot of focus on the hardware and software of the robots, their technology, features and compatibility with existing infrastructure. However, considering the purpose of the AMRs is to deliver material, material flow is a surprisingly overlooked aspect.
Let me highlight a few of our key considerations when evaluating material flow.
1. Traffic congestion
AMRs interact with each other, other manual/automated transporters, and humans on the floor. These small but frequent interactions add up and can significantly impact traffic flow and fleet sizing.
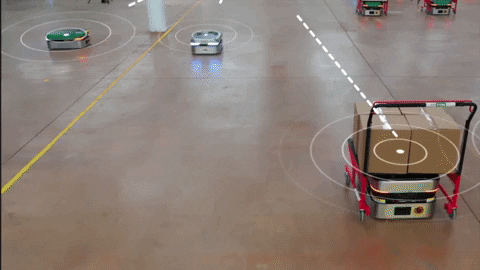
2. Routing
Even though AMRs are autonomous and plan their routes dynamically, there are still traffic rules that you can implement in your facility. These traffic rules can help minimize traffic congestion or shorten paths for the AMRs to improve robot utilization and material flow throughout a facility.
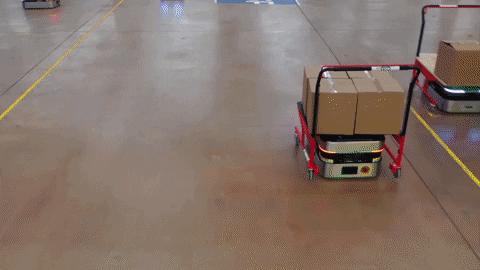
3. Space utilization
The amount of space available for AMRs to travel on as well as the location and quantities of queue spots, staging areas, and even parking and charging spots all impact material flow.
4. Workflow definition and job assignments
Robots carrying out mission critical operations may require custom workflow and job assignment definitions to ensure on-time delivery.
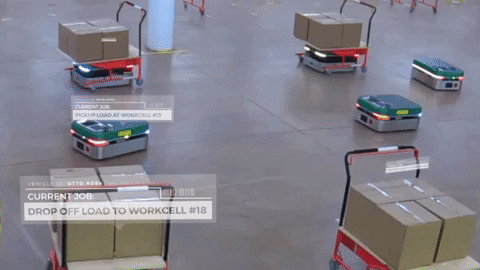
5. Fleet sizing
Fleet size impacts the overall traffic volume. The larger and more complex the project, the harder it is to determine the correct fleet size using conventional spreadsheet based methods.
Why simulation matters
The ability to test and quantify impacts in the early project phases is key. This is because during initial phases, there are many design options we can choose from, and the cost to switch between design options is low. The closer we get to the deployment date, the more finalized the designs of the layout, infrastructure and equipment are. If problems are found at this stage, design options are much more limited, and the cost to change it can be very expensive or even not possible to implement. This is precisely what we want to avoid—reacting to surprises late in the game.
Leveraging simulation, we can test all of the material flow factors I listed above and more, and evaluate as many alternate options as we want, well in advance of the actual deployment.
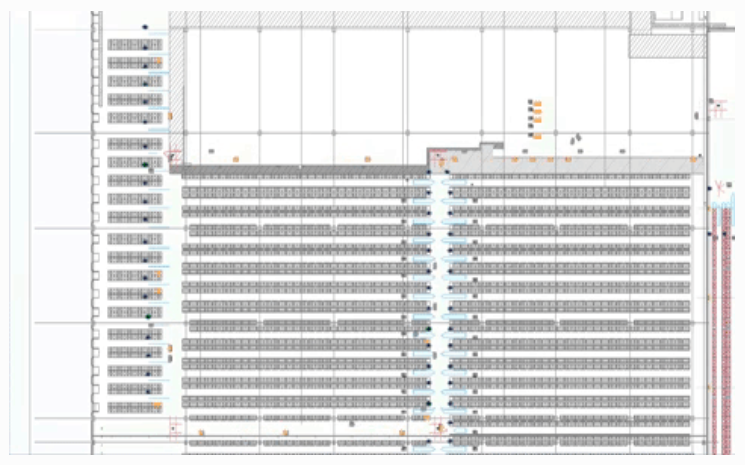
Sample simulation of a facility.
Simulation in action
We leverage simulation right from the early scoping phase, all the way to system deployment. The first use of simulation is to assess the feasibility of a project where we validate that the AMR deployment plan can meet throughput and space requirements. But that’s only the beginning. The simulation also provides key inputs for the business case and return on investment assessments. Once technical feasibility and the business case is confirmed, simulation can be used to understand design tradeoffs to allow you to make the necessary decisions to improve your operational requirements. Finally, simulation enables us to identify risks that we wouldn’t have known early. Once these risks are identified, we can work on solutions and assess the options to select the best mitigation plan.
If you’d like to learn more about our simulation services, you can watch our full webinar "Seeing is Believing: Simulating AMRs for Successful Deployments" where I walk through two case studies, sharing the type of simulation assessments done throughout the various phases of a project for two deployments at a Fortune 500 customer in the food and beverage industry.
WEBINAR: Simulating AMRs for successful deployments
Interested to learn more? Watch the webinar to see in depth case studies.