Blog
The importance of semi-annual software updates to enhance AMR fleet efficiency

Written by Jay, Vice President of Product, and Anthony, Vice President of OEM Platforms at OTTO by Rockwell Automation.
Autonomous material handling has many interconnected components—including hardware, software and services—that make the solution efficient, safe, and cost-effective for manufacturers to deploy. While the hardware component—the autonomous mobile robots (AMRs) themselves—often captures the spotlight, the software and services are essential to the success of a deployment.
Autonomous material handling deployments achieve their greatest level of efficiency when powered by a sophisticated software suite that continually evolves your facility’s performance, long after the initial implementation. Regular software upgrades increase the value of your autonomous material handling solution by addressing your most common challenges with new features that improve efficiency, safety, and cost-effectiveness.
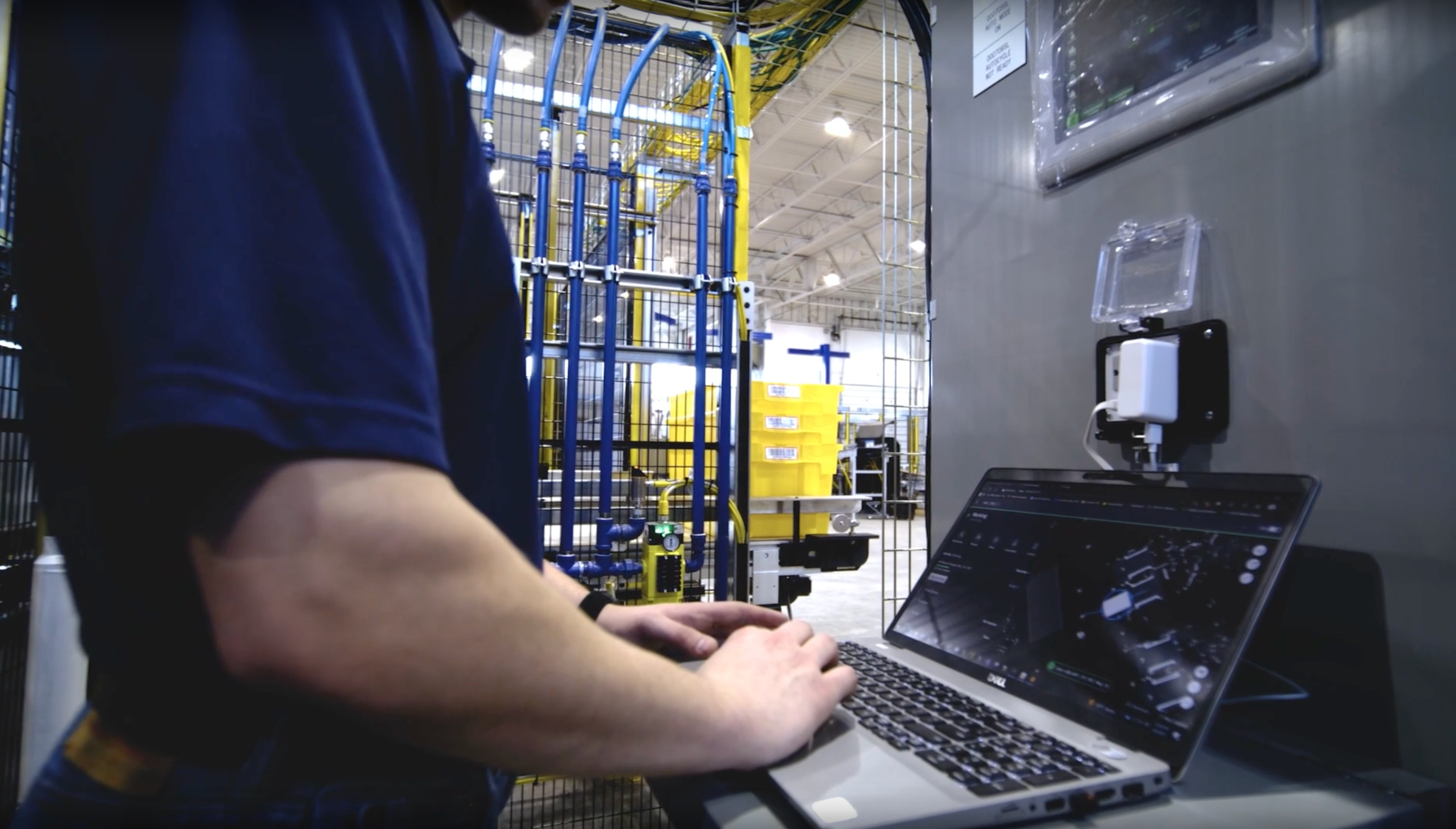
Video 1: Leading manufacturers leverage AMR software to improve operational efficiency across industries.
Customer feedback is the driving force behind OTTO’s semi-annual software updates
When the OTTO division was founded in 2015, we quickly released small updates that addressed individual customer needs. From 2019, we’ve committed to one release every six months to develop and deliver higher quality improvements for our customers.
We carefully prioritize every feature in our semi-annual releases to ensure they address our customer’s most critical needs. This means every single feature we release needs to deliver real impact.
Jay Judkowitz, Vice President of Product, OTTO by Rockwell Automation
What we choose to develop for each semi-annual release is based on extensive customer and market research. We speak with our manufacturing customers worldwide to understand how higher demands on productivity, usability, and scalability—to name a few—can be solved through software upgrades.
As we deploy larger fleets, we increasingly learn about the subtleties of how our customers want to see the robots work. This unique insight helps us refine operations for our customers and deliver incremental value, long after the initial deployment.
Increasing ROI is a top priority for every customer of ours and is therefore a priority for us. OTTO’s software updates help boost ROI through increased predictability and flexibility of our robots, optimized facility floor space, maximized fleet uptime, and enhanced security measures—all delivered through a simplified user experience.
Our customers are experts in manufacturing and the best in the world at what they do. To keep them moving forward, our job at OTTO is to create a robotic tool that is reliable, scalable, intuitive and easy to use. By continually simplifying the user experience so that anyone in a plant can easily use the solution, our customers can focus on what they are best at.
Jay Judkowitz, Vice President of Product, OTTO by Rockwell Automation
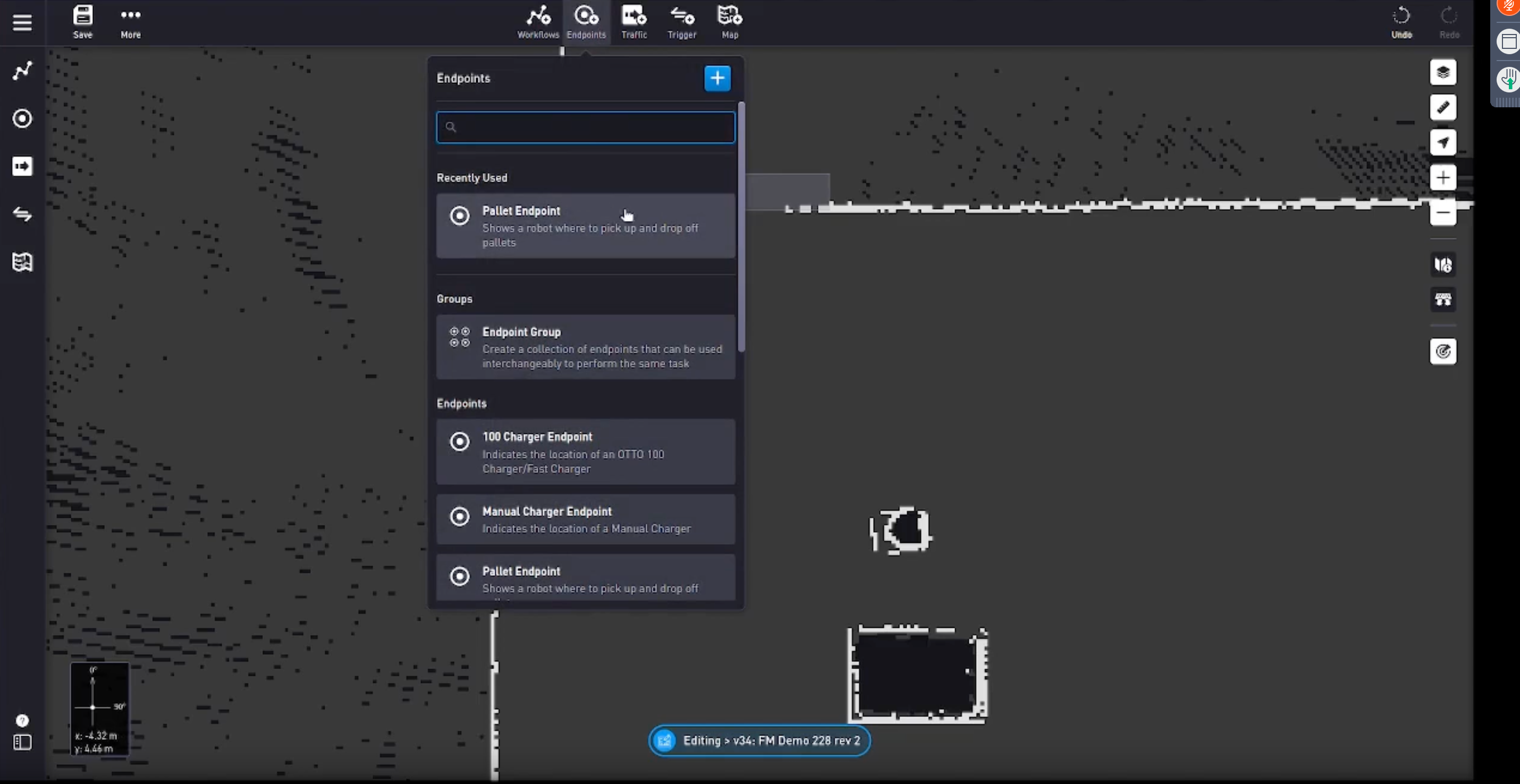
Video 2: A simplified setup process introduced in Spring 2023 saves users 50% of the time needed to create and edit facility maps and workflows. In this video, discover how easy it is to create a pallet endpoint using the new UI.
OTTO’s semi-annual commitment to delivering added value for customers
OTTO is committed to challenging ourselves every six months to make our products the best so that our customers can perform at their best. Amid the extreme competitiveness across the manufacturing industry, it’s essential that we give our customers the tools they need to succeed.
By enforcing a six-month timeline on ourselves, we continue to challenge our team and push our limits, merging the passion and urgency of a startup with the resources and knowledge of an established industry leader. We will continue to be our own disruptor, to evolve our products, to revolutionize the industry, and to exceed our customers’ expectations.
Anthony Tod, Vice President of OEM Platforms, OTTO by Rockwell Automation
To learn more about our latest semi-annual software update, read the press release.
Subscribe to our newsletter
Stay in the loop on product news, case studies, upcoming events and more.