Blog
Key takeaways from top performing Industry 4.0 eBook
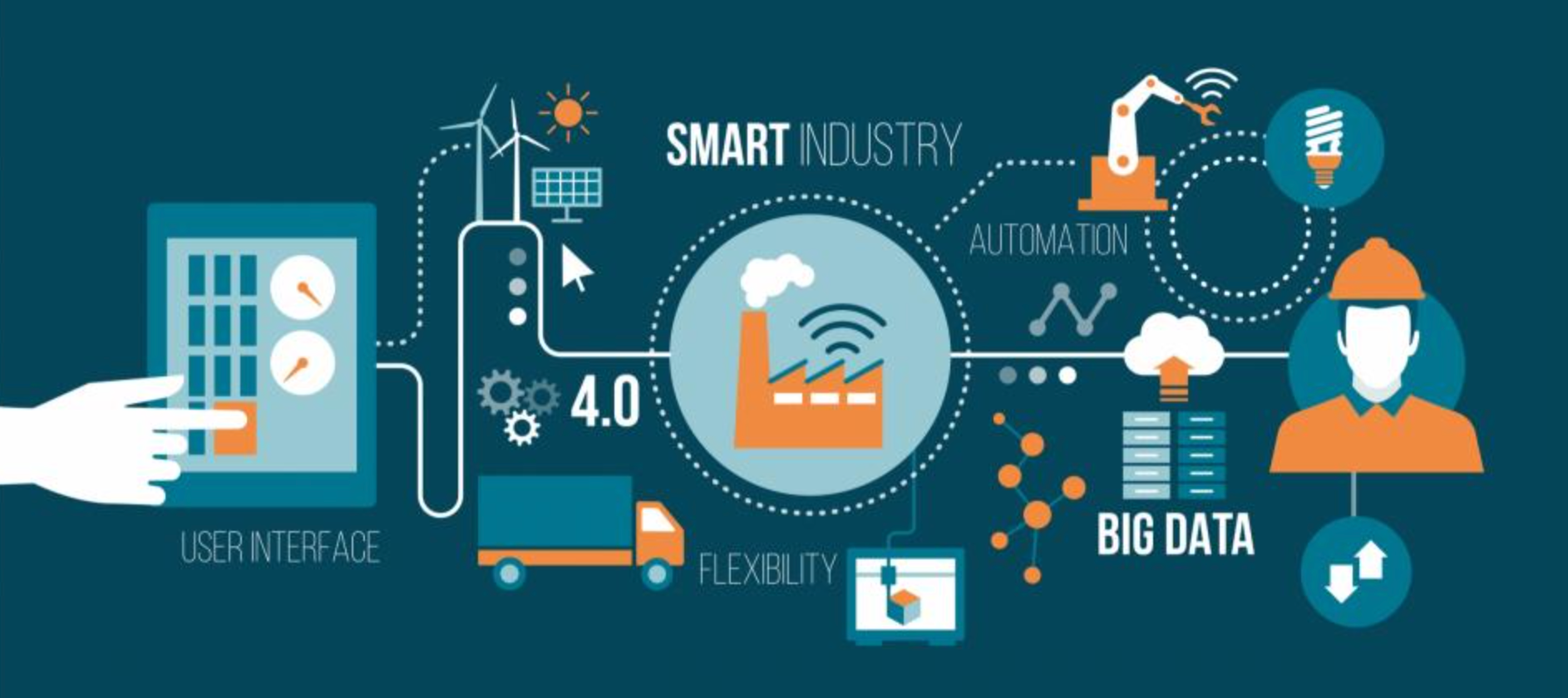
Automation has transformed the way factories and warehouses work, making it cheaper and faster to produce a wide variety of products. However, material handling remains an inefficiency in manufacturing, costing companies time and money.
The Innovation in an Interconnected World eBook will help you take the first step to automating material handling, ensuring your factory is connected from process to process. Here are the top three takeaways you need to know:
1. Your material handling process could be more efficient
Material handling has often been considered non-essential when deciding what to automate in the warehouse because it is non-revenue generating. However, inefficiency in material handling is extremely costly because of the human-intensive nature of the work. Your current material handling method might be driving up factory costs by involving unnecessary human motion, part transport and handling, or wait times. Consider this:
In a typical manufacturing facility, material handling can account for up to 70% of an item’s total production cost, occupy 25% of employees, consume 55% of factory space and up to 87% of production time.
Innovation through Industry 4.0 technology can also reduce the risk of error and increase worker safety by transferring workers from dull, dangerous or dirty work such as material handling to more value-added work.
Take GE Healthcare for example. GE requires consistent, fast and quality material handling to ensure hospitals can restore operations quickly. Before implementing OTTO autonomous mobile robots (AMRs), GE Healthcare's technicians pushed carts around the 280,000 square foot facility to move equipment between repair cells, shipping, and other technicians. The material handling was inefficient, costing the company time and money.
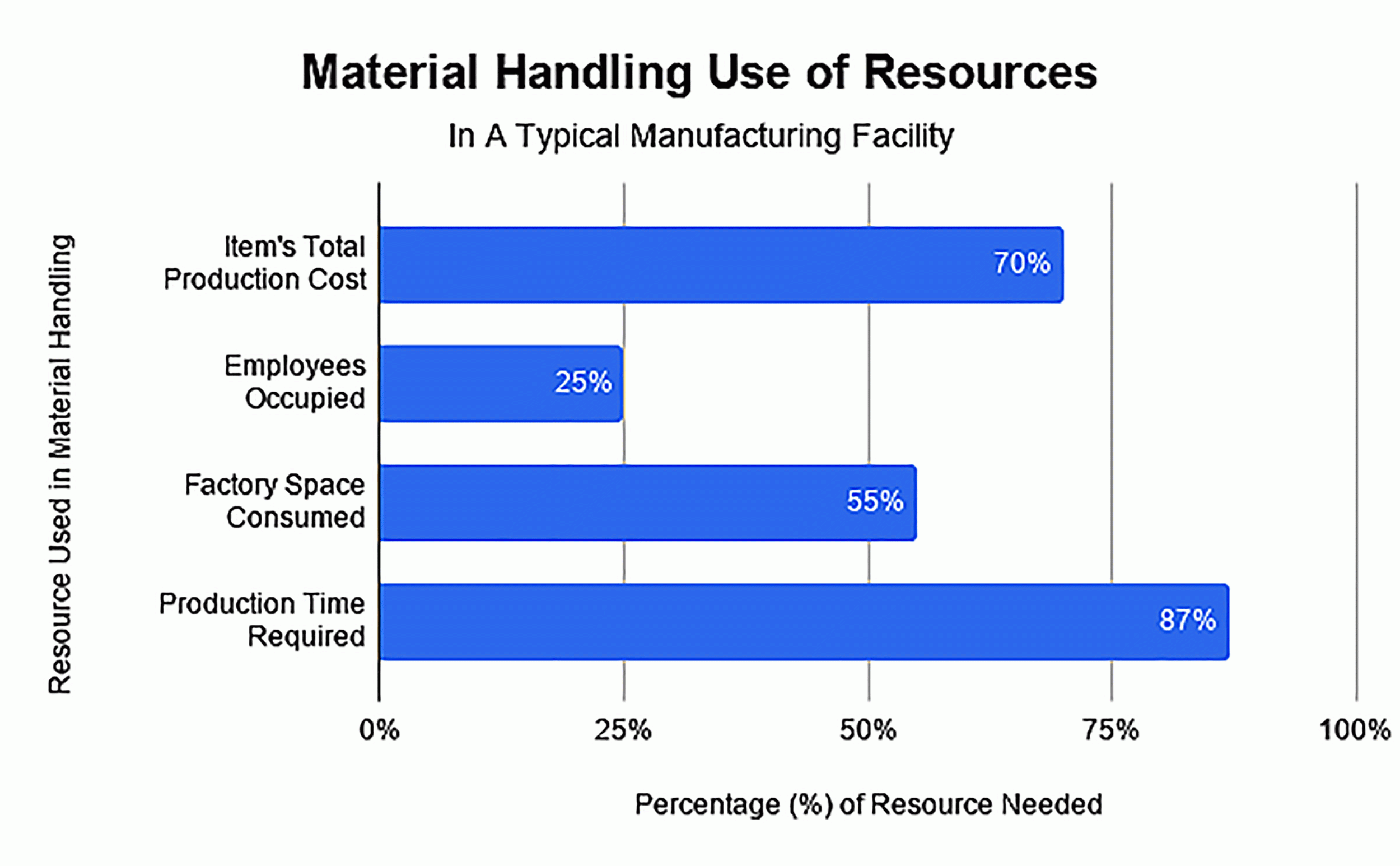
Chart 1: Inefficiencies in material handling in a typical manufacturing facility
2. Adding more forklifts, AGVs, or humans is not the answer
When faced with material transport challenges, an operation team's first thought may be to buy a new forklift, implement AGVs (automated guided vehicles), or hire more employees.
Here’s why those aren’t the answer:
- Forklifts require operators, can be dangerous, and—because they’re intended to move a lot at once and are cumbersome to operate—aren’t suited to the quick changeovers demanded of mixed-model assembly lines.
- AGVs are a form of mobile robot that rely on pre-programmed paths, such as magnetic tape, to find their way, so if anything changes—say, an obstruction blocks their path, or they’re needed on another route—someone has to reprogram them. This takes time, money and effort that could be better spent elsewhere.
- Humans are great at adapting to changing conditions on the factory floor, but assigning them to the tedious task of material transport is a waste of their talents.
Instead, GE Healthcare implemented AMRs into their facility, because AMRs can do what forklifts, AGVs, and humans can't: efficiently deliver equipment, safely, on time, and without any additional costs.
The system can make a decision to turn and take different routes, which was essential for us. Our process changes every day depending on what parts come in for repair, but OTTO can accommodate all of them with its flexible attachments for different payloads.
Patricio Espinosa
Director of Americas Repair Operations, GE Healthcare
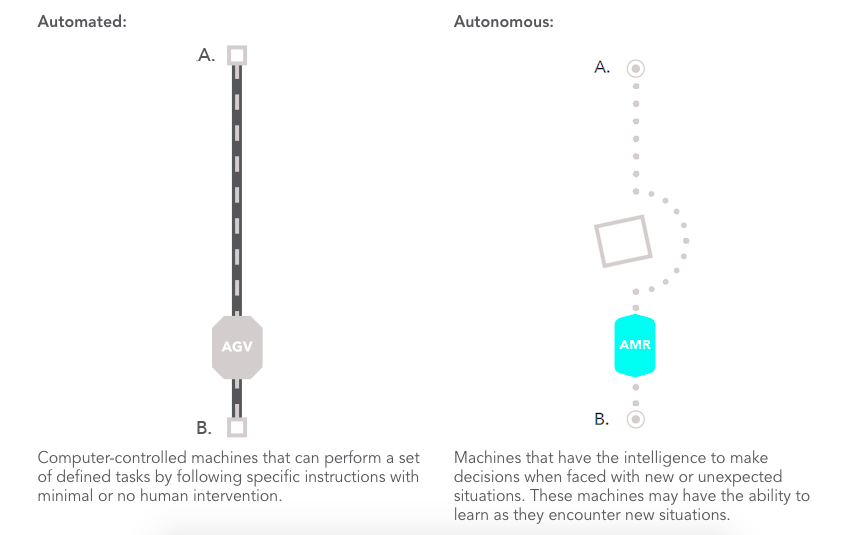
Image 1: The difference between AGVs and AMRs. AMRs are able to autonomously change course if something blocks their path.
3. Embrace Industry 4.0 to reap the full benefits of AMRs
AMRs operate autonomously while constantly sharing information to maximize efficiency. Specifically, AMRs do not require "direct driver input to control the steering, acceleration, and breaking." Further, AMRs will “deliver the right amount of goods to the line exactly when needed, produce the exact quantity required with no waste, and do so with maximum transport efficiency.”
AMRs and other Industry 4.0 technologies, such as artificial intelligence and 3D printing, are embraced around the world by innovative companies such as Google. Industries ranging from aerospace to agriculture to household appliance companies are using Industry 4.0 technology to improve facilities, processes, and lives.
When manufacturers embrace the technology of Industry 4.0, the Return on Investment is impressive, including:
- Higher throughput
- Lower labour costs
- Less worker compensation incidents
- Reduced training expenses
- Reduced infrastructure costs
- And many more
When GE Healthcare embraced Industry 4.0 technology, they were able to reduce the wasted space of their repair cells by 40% because there was no longer a need for extra physical infrastructure or large material movement equipment. This lean manufacturing allowed the company to increase their productive floor space by 66%.
Innovation in an Interconnected World highlights AMRs as an Industry 4.0 solution to your material handling inefficiencies. If you're looking to maximize your material transport efficiency, also look into The Plant Manager's Guide to Industry 4.0 blog.