Blog
Transform 5 inefficient material handling workflows with OTTO 600
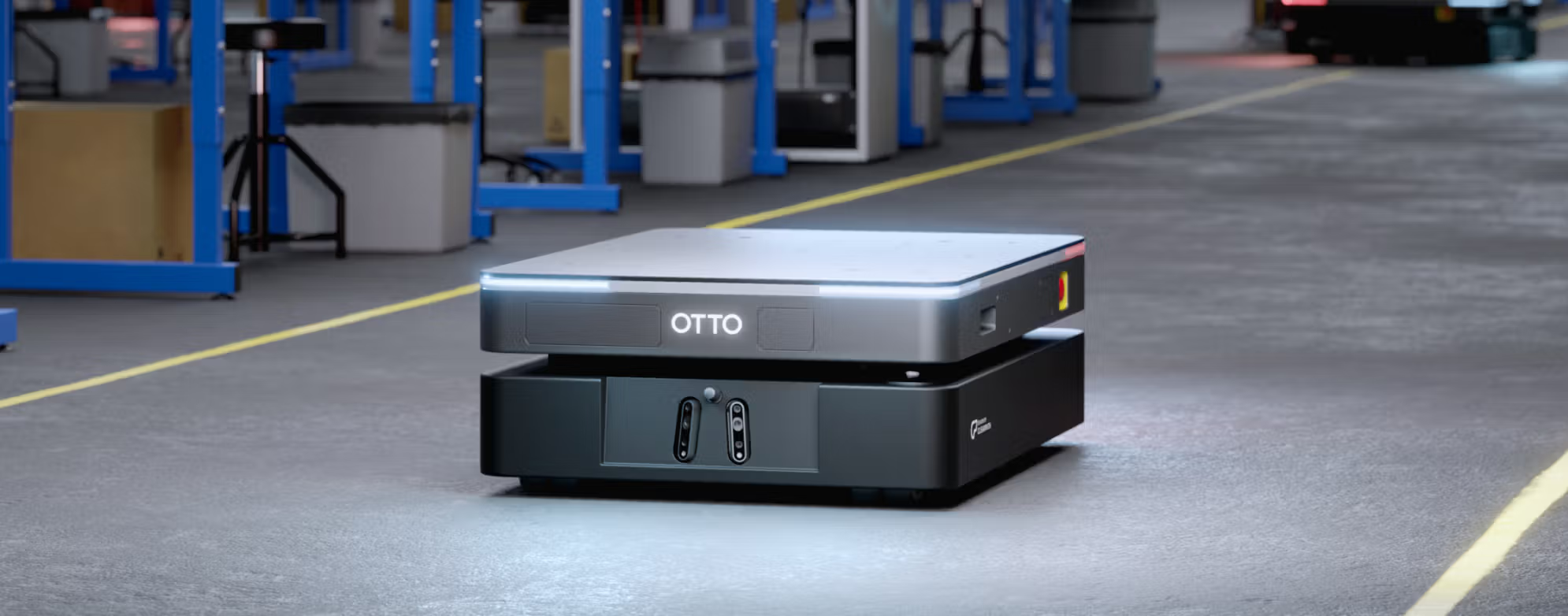
The automation of unsafe and inefficient manual material handling is helping manufacturers produce goods faster and with higher quality, enabling better service for their customers. As the adoption of autonomous material handling increases, with 79% of supply chain companies planning to adopt the technology in the next five years, the need for more form factors and payload capacities increase.
OTTO Motors has been at the forefront of the self-driving revolution since 2015 and continues to bring new and innovative products to the market. The launch of OTTO 600, a midsize AMR, unlocks the industry’s most comprehensive fleet of flatbed and forked AMRs that can move light, medium and heavy payloads up to 4,200 lb.
With a capacity of 600 kg, OTTO 600 is designed to streamline inefficient material handling workflows across various industries, including automotive, industrial, and consumer goods. Additionally, with the smallest footprint in its class (1050 x 700 x 320mm), OTTO 600 brings all the benefits that are expected from the OTTO AMR stack in a robot optimized for space-constrained applications.
Video 1: Introducing OTTO 600, a midsize AMR with uncompromising strength and agility.
In this blog, we explore five material handling workflows that you can improve by automating with OTTO 600: industry’s toughest and most nimble midsize AMR.
Work in Progress (WIP) transport
WIP is one of the most critical aspects of manufacturing and is often very complex, dynamic and characterized by ever changing needs. As a result, moving materials along the production line can lead to safety incidents, lost time and increased costs.
OTTO 600 can help you overcome these challenges as it offers the flexibility and intelligence needed to handle complex and harsh WIP transfers. It is powered by the software suite that is already proven to navigate dynamic environments in mission critical operations and is trusted by brands like GE and Toyota.
How OTTO 600 automates WIP transport
An operator at the prep station calls for an OTTO 600 by simply clicking a button upon completion of their task. OTTO, equipped with a conveyor attachment, arrives and connects to the conveyor at the station. The operator transfers the materials (usually a bin) on the OTTO by pushing a PLC button and marks the task complete. Then the operator sends OTTO to the designated location along the line, where the robot parks and the receiving operator unloads the bin. Once unloaded, the operator will simply click a button to complete the mission and OTTO will become available for the next task. OTTO 600 quickly moves your material from one process area to the next stage without compromising on safety.
Video 2: Just like all OTTO AMRs, OTTO 600 safely stops when a person stands or walks in front of it, only proceeding once the person has moved or it has found a safe route around.
Finished goods transfer to staging or shipping
The transfer of finished goods from the end of the production line to staging or shipping is a crucial step in delivering your product to customers. By automating this last mile with OTTO 600, you can get more products out the door in less time, free-up employees for valuable tasks and meet your targets for on-time delivery KPIs.
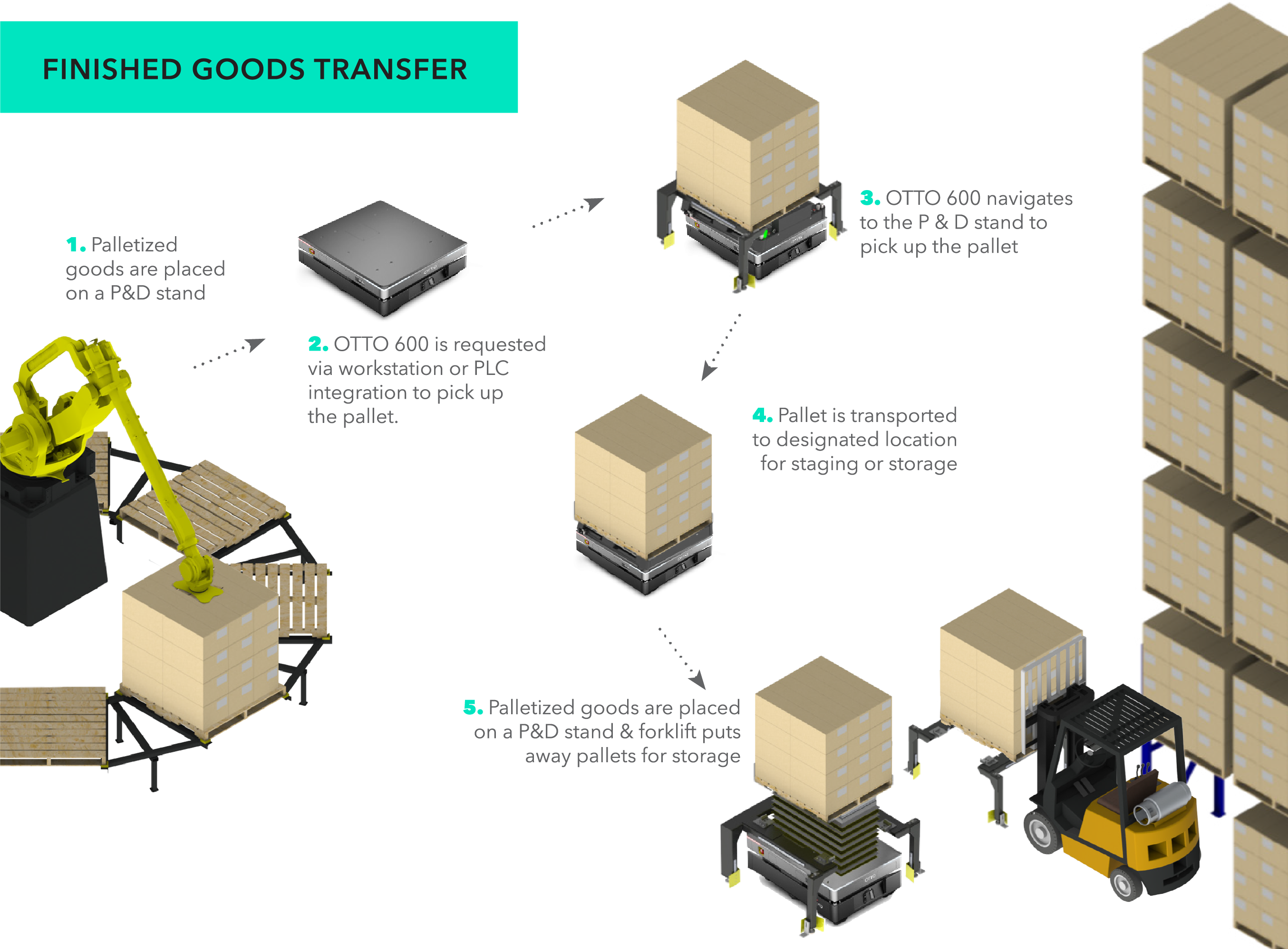
Image 1: OTTO 600 can automate the finished good transfer workflow.
How OTTO 600 automates finished goods transfer
OTTO 600 is equipped to help you transport different types of finished goods, such as pallets or individual parts. Let's consider how OTTO can be deployed in both scenarios:
- Palletized goods transfer: This is an example where OTTO 600, equipped with a lift, connects islands of automation. Palletizer builds and places pallets on a pick-up and drop-off (P&D) stand, and OTTO 600 is requested via PLC integration. OTTO 600 autonomously picks up the pallet from the stand and transports the material from the production line to the staging area or directly to the designated location in the shipping area. From the drop-off location, forklifts can then pick up the pallets and place them in the warehouse racks, ready to be shipped.
- Non-palletized material transfer: Your business may require you to automate the movement of non-palletized products from the assembly line to packaging and shipping. In this case, when the operator at the last station finishes working on the part, they request OTTO 600 by simply pressing a button. OTTO 600 autonomously navigates to the workstation where the operator places the material on it, and then will autonomously transport it to outbound where it can be packaged and shipped.
Moving finished goods through a very intense and crowded production environment can be challenging and marred by delays. OTTO 600, with its small footprint and nimble navigation, can help solve this challenge. In addition to maximum speed down a straight unobstructed aisle, it has been optimized for fast and safe turns and pivots.
Lineside delivery
One of the most crucial aspects of lineside delivery is to deliver the right part to the right place at the right time. Traditionally, materials have been delivered to the lineside by humans (pushing carts or driving tuggers) or AGVs which either requires a large workforce or infrastructure investment. However, it can be difficult to achieve precision with manual material handling, which is prone to errors. By autonomously moving material with OTTO 600, you can solve these challenges while improving safety and creating a more fulfilling work environment.
How OTTO 600 automates lineside delivery
While automating lineside delivery, an operator pre-loads a gravity rack with material for use by the manufacturing operation. When the lineside sends a signal that more material is required, the OTTO 600 navigates to the pick up point and docks to the gravity rack. The gravity rack then releases the material to slide onto the fixture on the robot. The OTTO 600 proceeds to the lineside drop off location, docks, and the material slides off the onboard robot gravity racking and onto the lineside racking.
Powered by industry’s most trusted autonomy software, OTTO 600 can efficiently navigate dynamic environments, avoiding obstacles and rerouting where required. This ensures that it will always find the most optimized route to the lineside for timely deliveries. Additionally, OTTO 600, like all other OTTO AMRs, is managed by OTTO’s fleet management software which ensures that the right AMR delivers the right parts to the right locations, every time.
We recently launched the new software version 2.28 which further strengthens OTTO’s software suite. Learn about the improvements in AMR traffic management and ease-of-use in the blog.
Video 3: Users can now optimize their AMR fleets for higher productivity with OTTO Motors’ latest software release.
Automating the movement of non-conveyable materials
Non-conveyable materials have always been difficult to move through facilities because they do not play nicely with your standard conveyor systems. These items are generally too heavy or large to move across conveyors or often too irregularly shaped to fit onto a conveyor. Typically, facilities would need to allocate more of their valuable workforce to manually transport non-conveyables, increasing the cost of material handling. This is often seen in the shipping and mail delivery industries.
How OTTO 600 automates the movement of non-conveyable materials
OTTO 600 is highly suited for this application because of its payload range which can carry a lot of non-conveyable materials across industries like logistics and warehousing. OTTO 600 offers a flexible material movement solution so you can move any payload at any time without infrastructure changes. If the flow of non-conveyable materials is inconsistent, OTTO 600 can be redeployed in other jobs without requiring any infrastructure changes.
Even when loaded with odd-sized materials, OTTO 600 can move non-conveyables quickly and safely due to two important features of our navigation software:
1) Robust and quick path planning
By leveraging different path planning technologies, OTTO 600 is able to be both flexible and predictable in complicated environments. It quickly plans for the most efficient path and once underway, OTTO 600 refines it by consistently searching for improvements to the route. Read more about path planning here.
2) Obstacle avoidance to ensure speed with safety
Unlike other AMRs in the market which may guess the shape and size of their safety fields, OTTO’s advanced autonomy software ensures OTTO AMRs know the exact shape and size. This allows OTTO to optimize and maximize its speed while accounting for safety obstacles and blockages. If an obstacle or blockage is encountered, OTTO will proactively avoid it, safely stopping if required, and then redirecting as required.
Video 4: Obstacle avoidance shown in OTTO Fleet Manager.
Palletizer to stretch wrapper
In the traditional process of palletizing and stretch wrapping, humans operating pump trucks and forklifts transfer the materials between stations. Not only can this process result in stress injuries and accidents, it also puts humans in low-skilled tasks when they could be performing higher-value duties. In fact, there is a 90% chance of a serious accident occurring during the eight-year average lifespan of a forklift, according to OSHA. OTTO AMR’s advanced safety sensors paired with class-leading autonomous driving capabilities reduces risk of workplace safety incidents and allows you to redeploy humans in more fulfilling roles.
How OTTO 600 automates palletizer to stretch wrapper
For this workflow, OTTO 600 is usually equipped with a conveyor attachment so that it can connect to the conveyors of two other pieces of equipment for material transfer - the palletizer and the stretch wrapper.
Once the palletizer finishes creating pallets and loads them on the conveyor, OTTO 600 can be triggered automatically with facility integration to retrieve them. OTTO 600 autonomously navigates and positions itself at the end of the palletizer conveyor and once in position, the pallet is transferred to the conveyor attachment on the OTTO 600. Alternatively, if your workflow involves creating pallets manually and loading them on a conveyor, an operator can trigger OTTO for pick-up by simply pressing a PLC button. OTTO 600 autonomously drives the pallet to the stretch wrapping machine, positions itself precisely, and transfers the pallet for wrapping.
OTTO 600 is a versatile AMR that can be equipped with various attachments including lifts and conveyors and can also connect islands of automations. Facility integration is one of the most important elements which enable seamless material handling in facilities.
OTTO 600 comes with OTTO’s industry-leading fleet management software which enables smooth facility integration to allow for fully automated workflows like these. Easily connect OTTO Fleet Manager to any factory tools or systems you have in a place like your ERP or WMS via REST API and Websocket or OPC-UA Protocols and Ignition for PLC integration.
Jay Judkowitz
VP of Product at OTTO Motors
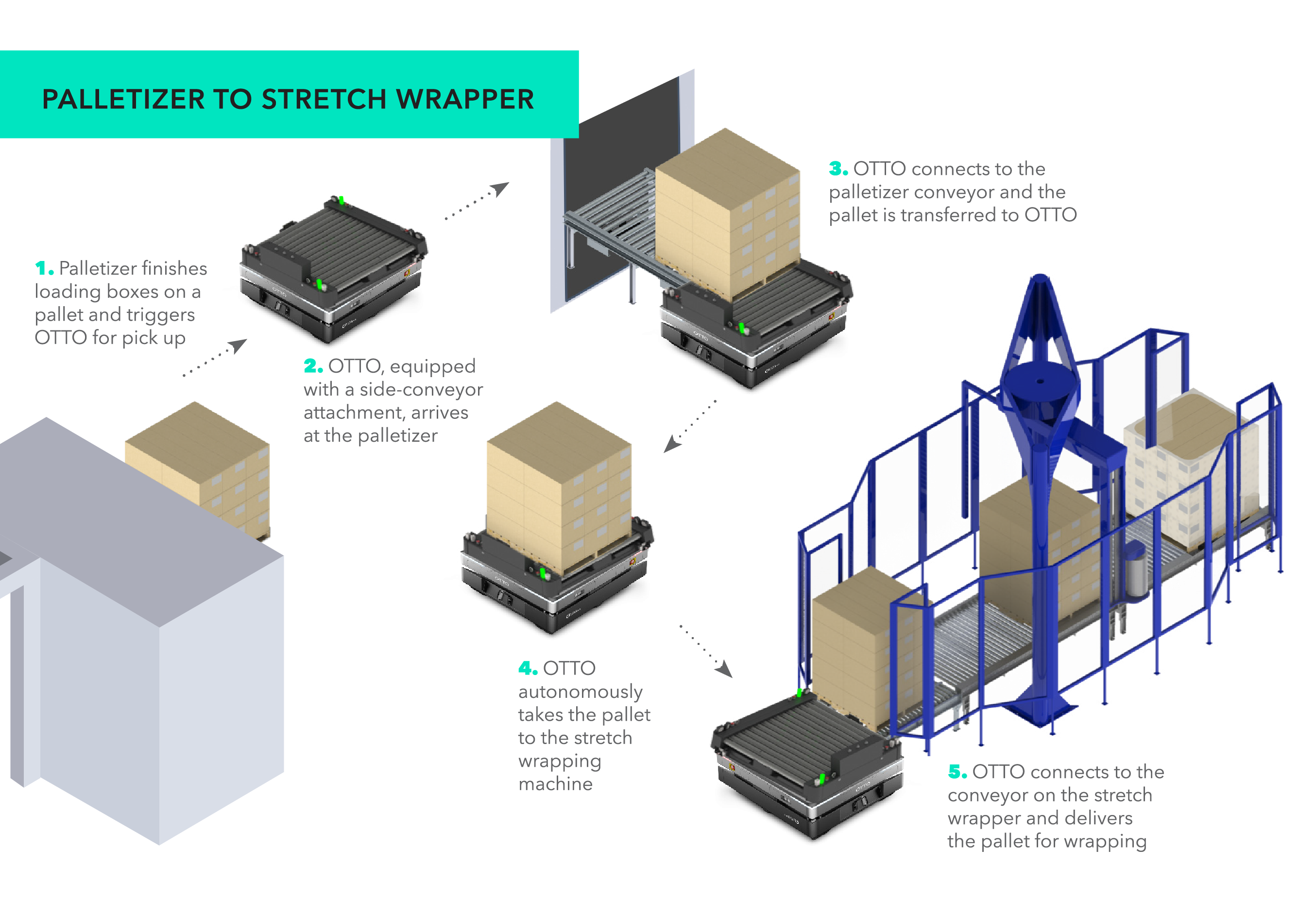
Image 2: OTTO 600 can automate the palletizers to stretch wrapper workflow.
Introducing AMRs to your operation can help combat material flow inefficiencies in your facility. The workflow guide above can be used as a starting point when considering which of your workflows are the highest priority for material handling transformation. Once a workflow has been identified as inefficient, unproductive or unsafe, the next step is for your team to consider which AMR is right for your needs.
From small-class to heavy-class, flatbed to forked, AMRs now offer a variety of footprints and capabilities that can improve your bottom line. In this webinar, we share a framework that will help you get started on your automation journey, from how to match common material handling challenges to the right AMR and what questions you should ask your AMR vendor.