Blog
Increasing material flow efficiency in your supply chain
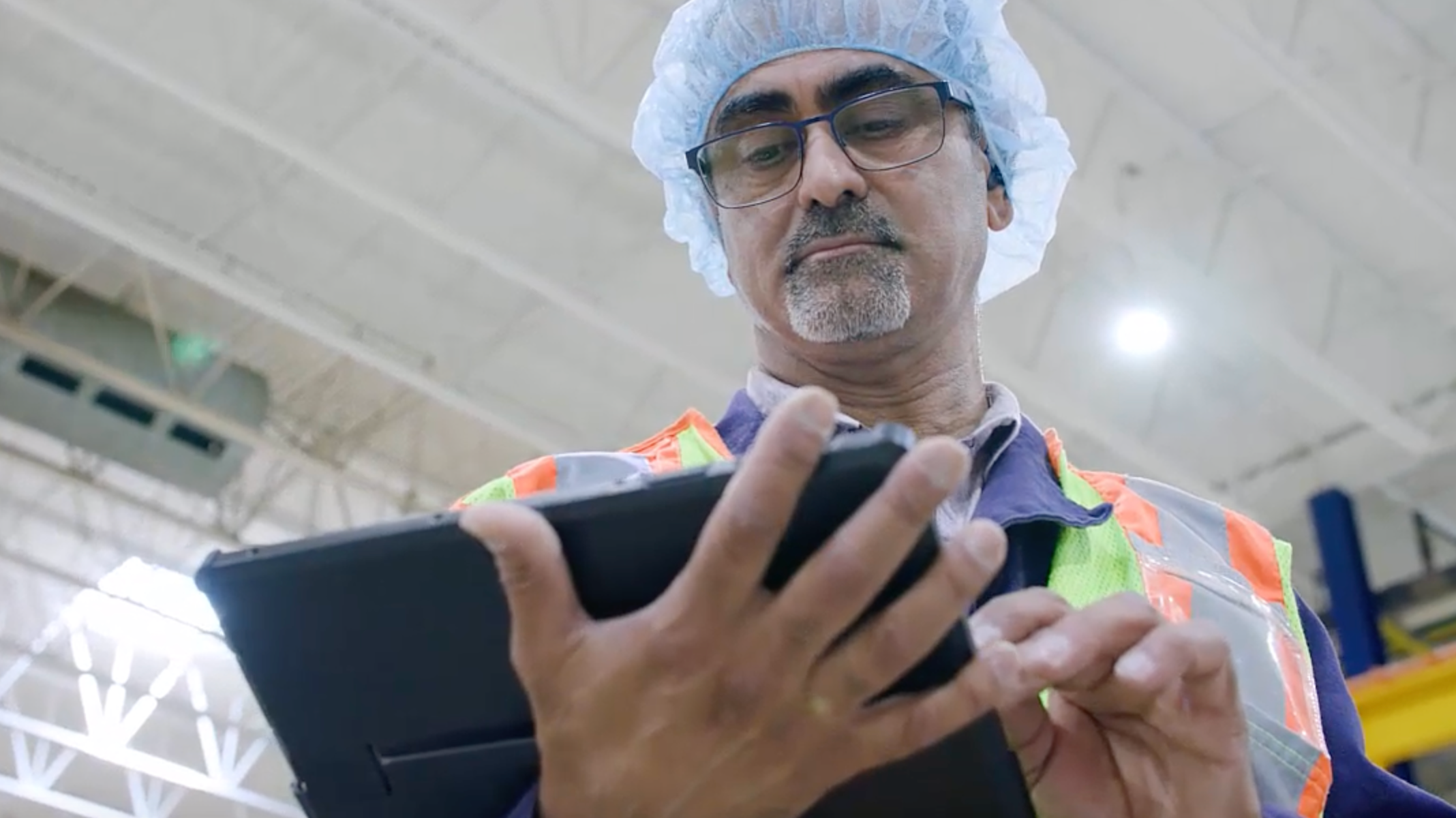
Modern supply chains need to be efficient to keep up with rising consumer demands and to reduce operating costs. In fact, customer demands for “more customized products and services,” “faster response times,” “lower delivered costs/pricing” and “service expectations'' are four of the top eight company challenges according to the 2023 Material Handling Institute (MHI) Annual Industry Report. Company success often depends on their ability to efficiently move parts around the manufacturing facility and between workstations. Products are moving from a raw material state to the end user quicker than they ever have before, but the demand for efficiency is still increasing.
Consumer expectations for choice and customization only add to the pressure felt by the supply chain and material handling functions. Products and parts must be located quickly, their progress tracked accurately, and shipped out to the customer on time.
The material flow process
A part can go through a lot of hands and processes before it becomes a finished product. If a recently received part needs to be stored before use, for example, it must be properly identified, coded, put in the correct location, and recorded. That is a lot of steps before it is even used in production. There are many cases where products are damaged due to handling, inaccurate storage, or delays moving to the next stage. It’s critical that the part is moved through the facility safely and accurately.
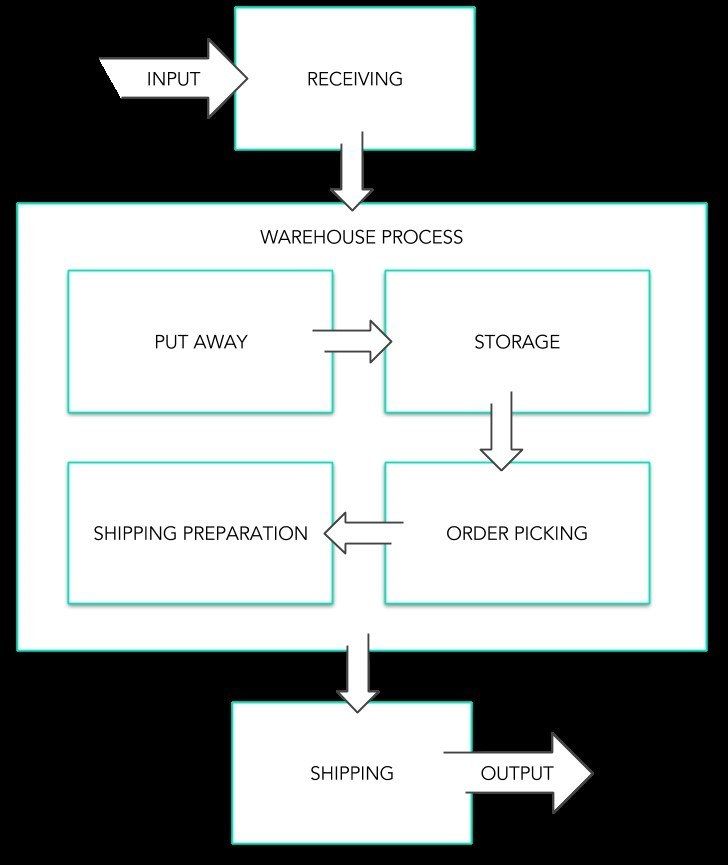
Image 1: The material flow process.
Maximizing efficiency of material flow with AMRs
A key part of the material handling process is the proper identification and unitized arrival of an item. When a part is inbounded, or if it is going to be cross-docked, it should have barcode labeling. Barcodes help to ensure the correct SKUs and quantities are received into inventory, and just as importantly, can be found when they are needed. They also enable automated material handling equipment to do its job. Now, parts and products can be moved to where they need to be with innovative technology, like autonomous mobile robots (AMRs).
Similarly, when parts are needed in production, AMRs can quickly locate, retrieve and move the materials to line side for use.
Optimal product flow leads to productive operations
During the production and order fulfillment processes, logistics managers need to ensure material flow efficiency to optimize inventory flow. Inefficient processes or inaccurate systems can lead to delayed deliveries and poor customer service. Every time an item moves, it’s an opportunity for an error to occur. In a survey, 17% of customers said they would stop buying from a company after one late delivery, and more than half said they’d abandon the company after two or three. Thus, material flow efficiency is critical to your operation.
AMRs and other material handling robots are tools used in modern facilities that prevent these types of problems. AMRs also help to maintain better control over inventory and product flow and improve the movement of material around a facility—especially in areas with high volume and where repetitive movements are required. They are also especially useful in facilities with frequent infrastructure changes and where equipment such as conveyors are not as effective.
OTTO has the most comprehensive AMR fleet in the industry, capable of improving productivity and safety, and combating the global labor shortage. Fortune 500 customers worldwide, including GE and Toyota, implement OTTO AMRs in dynamic, mission critical environments and have achieved:
- $1.3M saved in the first year at GE Aerospace
- 600%+ throughput increase at Mauser Packaging Solutions
- 70,000+ manual touches removed annually at Danfoss
- 66% improvement in floorspace use at GE Healthcare
Optimizing the movement of both raw materials and assembled products throughout a manufacturing facility or warehouse gets materials where they need to be faster, and with less chance for damage or loss. With more efficient and accurate material flow, assisted by technology such as AMRs, production runs better and customer deliveries are on time.