Blog
How OTTO Lifter solves material handling challenges across four unique industries

Manual material handling is dangerous. In fact, it is the leading cause of compensable injuries in the American workplace. This is typically due to manually-operated forklifts, which have a 90% chance of a serious accident occurring during their 8-year average lifespan, and are responsible for over 7,000 injuries in 2020 and 1 in 6 workplace deaths.
Not only is manual material handling dangerous, it’s also costly, consuming about 25% of the workforce, 55% of the factory floor and 87% of the time of production in a factory. These are some of the many reasons why manufacturers across all industries are turning to automation. These manufacturers are looking for options that are more flexible than conveyors and automated guided vehicles (AGVs) for their dynamic, space-constrained facilities.
That’s where autonomous mobile robots (AMRs) come in. Autonomous forklifts like OTTO Lifter mimic manual forklifts while offering the advantages of automation. In this blog, learn how four manufacturers have deployed OTTO Lifter in common workflows to solve their top challenges.
Putting safety first at a Fortune 500 consumer packaged goods facility
For this $13 billion CPG manufacturer, improving safety was the top priority. They also deployed OTTO Lifter to reduce physical strain for their near-retirement employees, cut labor costs and optimize floor space. Previously, workers were moving material manually with carts and forklifts, but this caused ergonomic risk that ultimately led to the introduction of automation.
While other AMRs introduced elevation that could cause ergonomic strain, an autonomous forklift allowed our employees to maximize safety by maintaining ideal ergonomic material handling elevations for a process that operators repeated up to 25 times per hour.
Director of Equipment Solutions, Fortune 500 CPG manufacturer
In their injection molding and decorating facility in Henderson, Nevada, this customer deployed two OTTO Lifter AMRs to automate the transport of pallets to and from their robotic palletizing systems. In this workflow, operators pack boxes from the molding and decorating departments and place them onto centralized conveyors, feeding the robotic palletizing cell. A mission is triggered for OTTO Lifter to pick up the full pallet inside the robotic cell and efficiently transfer it from the floor to a conveyor attached to a stretch wrapping machine. OTTO Lifter then retrieves an empty pallet from the robotic pallet dispenser and delivers it to the robotic palletizer to begin again. Built with industry-leading safety equipment and capable of working safely alongside industrial robotic equipment, OTTO Lifter optimizes safety and efficiency in this workflow.
Deployed in 2023, OTTO Lifter is already helping this CPG manufacturer improve ergonomics, retain employees, and optimize floor space. Learn more about this deployment in the blog.
Reallocating labor at a heavy truck parts distribution center
In this second example, a heavy truck parts distribution center wanted to reallocate their available labor to more fulfilling roles amid the global labor shortage that will leave an estimated 2.1 million manufacturing jobs unfilled in the USA by 2030. At this facility, operators were spending a significant amount of time on non-value-add work, driving between the receiving area and the warehouse to pick up packages countless times each shift.
Instead, the manufacturer wanted OTTO Lifter to automate the repetitive task of material handling that was previously done with manually-operated forklifts, and have their valuable operators spend time palletizing goods in storage racks. To achieve this reallocation of labor, the distribution center deployed OTTO Lifter in their parts distribution warehouse to streamline pallet handling, automating the transport of pallets from the inbound dock to the warehouse.
OTTO Lifter is built with an easy-to-use interface that displays key information at a glance, enabling operators to quickly learn the system and address issues immediately. Equipped with adaptive fieldset technology that improves efficiency by preventing slow downs around corners, people, and obstacles, OTTO Lifter maximizes average speed without compromising safety, boosting productivity. Capable of autonomously picking up misplaced and stretch wrapped pallets, OTTO Lifter navigates dynamic facilities quickly and safely, minimizing the need for human intervention.
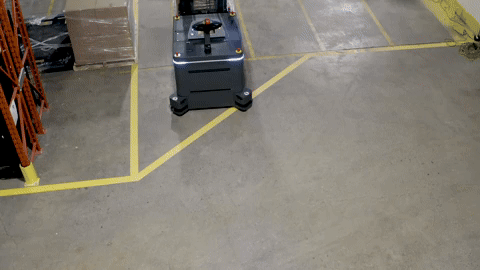
Introducing next-level integrations at a third-party logistics center
A warehouse and logistics company, called Kenco Group, introduced OTTO Lifter to overcome labor shortages and solve safety challenges associated with manual material handling. Previously moving materials with lift trucks, this solution drove transformational efficiency through the integration of material handling with their existing WMS system.
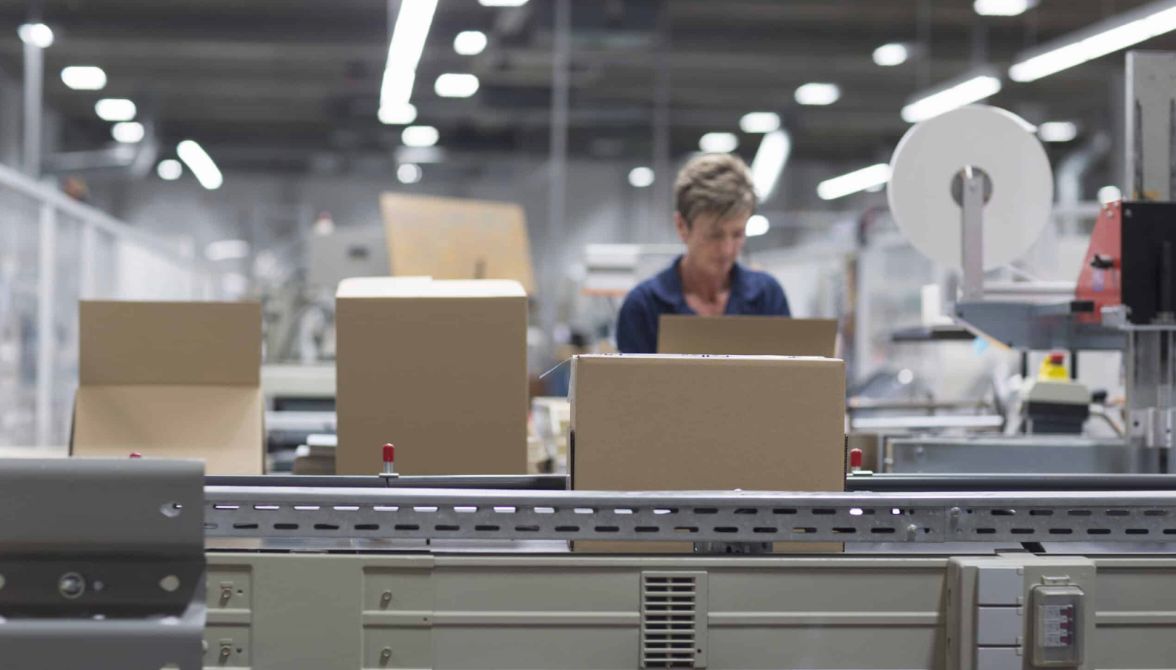
OTTO Lifter seamlessly collaborates with other OTTO AMRs in this large distribution center to move pallets from inbound staging to outbound staging, called dock to dock transport. In this workflow, OTTO Lifter receives a mission from the customer’s WMS which is integrated with OTTO Fleet Manager APIs, enabling jobs to be automatically assigned in real-time, streamlining operations and ensuring precise inventory control. OTTO Lifter picks up pallets from the floor-level staging lanes, efficiently transports pallets through this dynamic facility, then creates staging lanes near the outbound dock.
Reducing waste across a Fortune 500 food and beverage facility
In order to reduce waste, this Fortune 500 food & beverage manufacturer deployed OTTO Lifter to replace their manual material handling process led by manual forklifts and pallet jacks. OTTO Lifter automated the process of moving goods from the palletizer to the stretch wrapper, and finally to outbound staging.
Specifically, at this facility, ten OTTO Lifter AMRs support three unique tasks:
- They deliver empty pallets to the palletizing cell.
- They deliver the palletized totes and pallets of candy in display towers from robotic palletizing cells to stretch wrapping machines.
- They pick up the pallets from stretch wrapping machines and create temporary staging lanes near the outbound area, where a customer’s order of mixed products are put together. Capable of autonomously managing pallet lanes, OTTO Lifter maximizes efficiency without constant oversight.
Since implementing an autonomous forklift, the manufacturer has experienced consistent load handling, resulting in less scrap and higher quality. They are now able to easily track in-process inventory, and improve ergonomics and safety.
I’ve gotten the opportunity to have hands-on experience with OTTO Lifters and OTTO Fleet Manager while engineering a layout, simulation, and deployment for my project. Within 5 years, I can envision OTTOs popping up all over to solve any multitude of delivery scenarios. OTTO is moving the industry forward and mobile robots are the future.
Packaging Systems Engineer, Fortune 500 food and beverage manufacturer
With a payload capacity of 2,640 lb and an autonomous lift height of 39 inches, OTTO Lifter is improving safety, reallocating labor, introducing next-level integrations and reducing waste for manufacturing facilities spanning a variety of industries. To learn more about how you can transform your manual workflows with autonomous forklifts, watch the full webinar or download the infographic.
Subscribe to our newsletter
Stay in the loop on product news, case studies, upcoming events and more.