Blog
Pioneering perspectives: “OTTO became the industry’s AMR scaling expert through one of the world’s largest deployments”
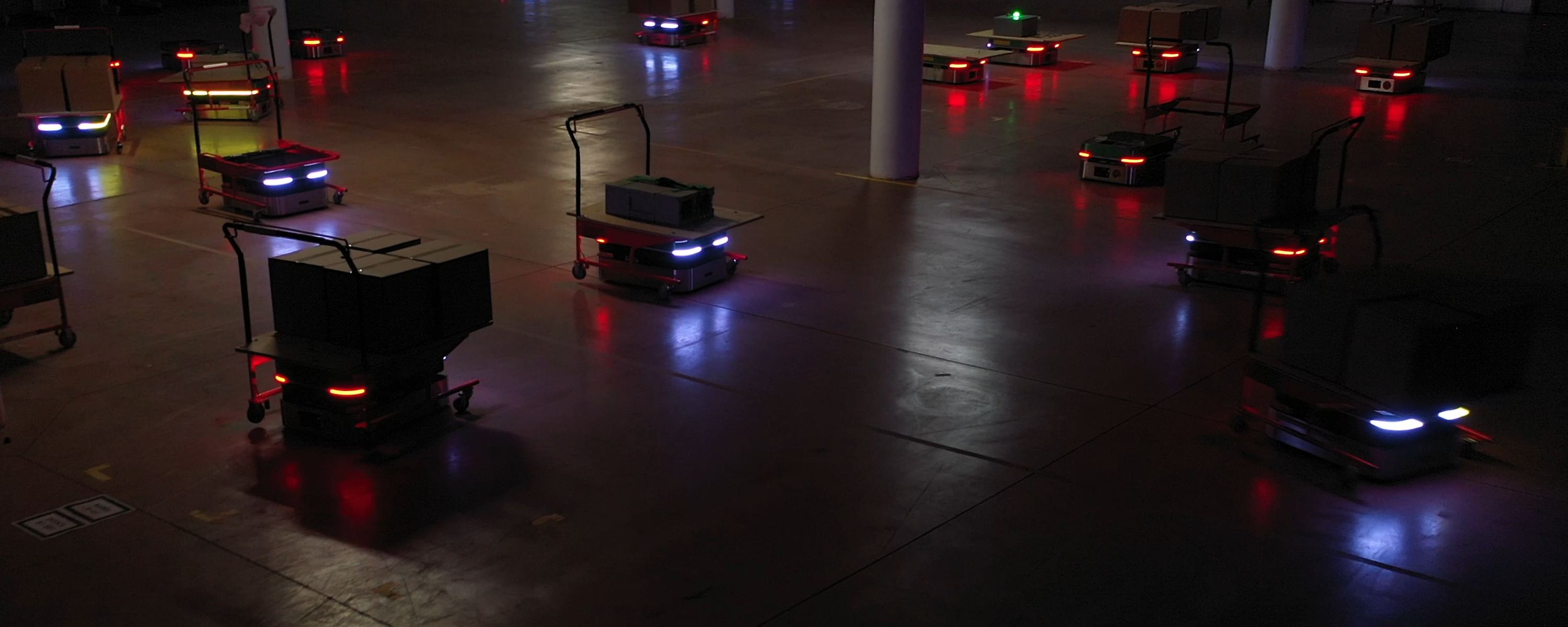
Written by Mark, Senior Program Manager at OTTO by Rockwell Automation.
OTTO grew rapidly in the company’s early years, but we had no idea just how big we could get. That is until we implemented one of the world’s largest deployments of autonomous mobile robots (AMRs) for material handling in manufacturing in 2020. As the leader of the project’s services team, I saw first hand how this deployment changed the material handling industry and shaped OTTO’s future within it.
Why a Fortune 500 company asked OTTO to deploy at scale
When the project began in 2019, we had many deployments with well-known customers that were achieving ROI, improving throughput, and increasing plant safety. OTTO was also leading the market in AMR scalability at this time, with powerful software capabilities that kept the robots operating productively at scale.
While other AMR vendors were operating fleets with a handful of robots, OTTO was already productively scaling to dozens of AMRs in mission-critical facilities.
Then, because of our scaling expertise and experience, we were asked by a billion-dollar Fortune 500 organization to implement 83 robots and simulate 130 across two facilities moving different payloads through various workflows, including connecting islands of automation, raw material transport, and finished goods transport. This household name in the consumer packaged goods industry trusted OTTO for this new challenge and we embraced it with excitement.
Early challenges and our experimental solutions
This deployment certainly did pose challenges that we—and very few AMR vendors in the world—had ever faced before. Scaling to 130 robots productively required months of simulation and validation, as well as live testing of the fleet. Our office was not large enough to replicate a portion of the customer’s factory floor, so we rented the basement of a pharmacy in town to make sure the deployment would perform successfully for the customer. A furniture rental company was using a portion of the basement too, so there were these piles of furniture in the corner. It always makes me laugh thinking back to those days.
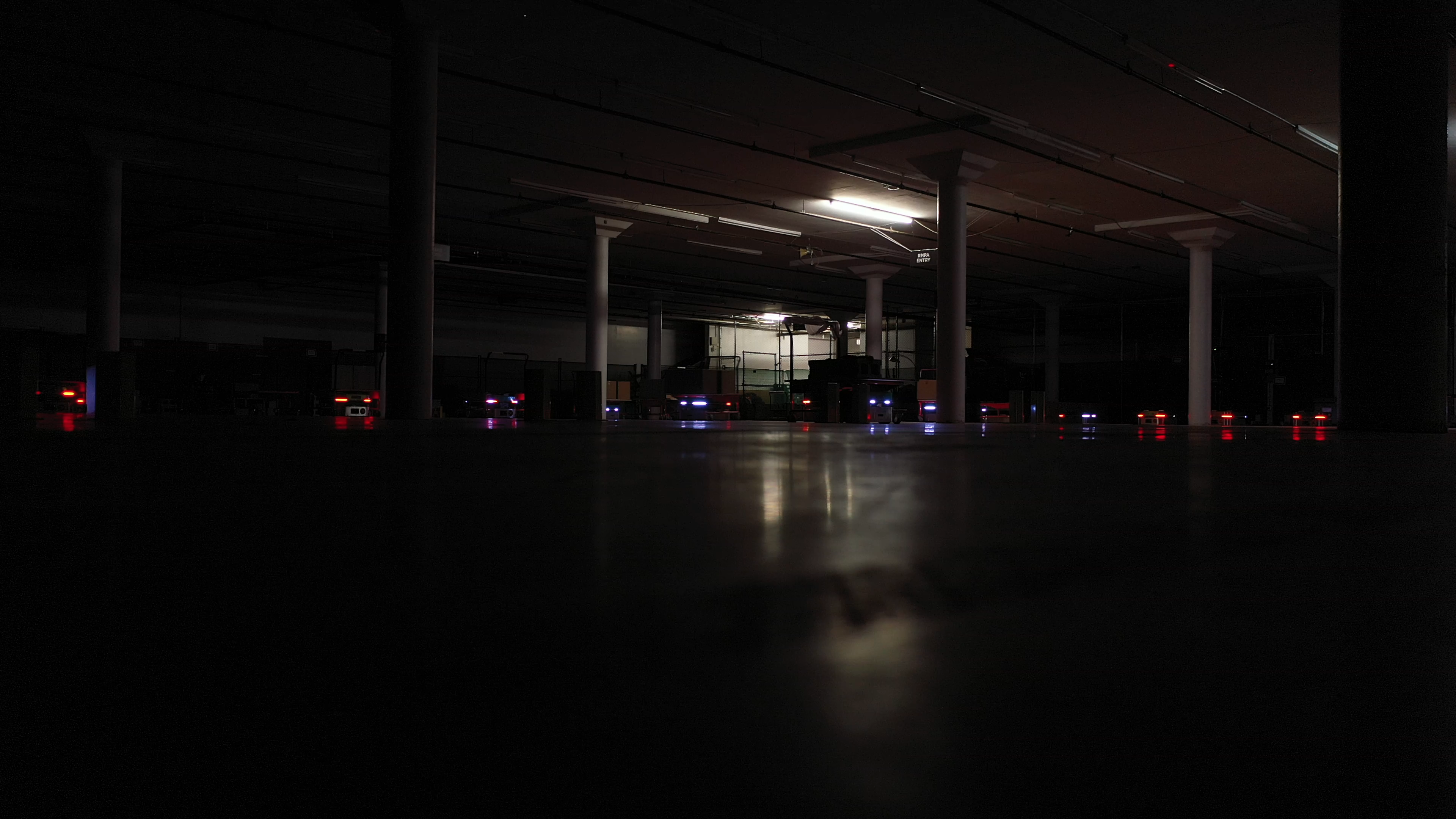
Image 1: We worked hard testing the deployment in the rented basement, and had some fun with the lights too!
We set up endpoints, aisles, robots, attachments and different payloads to replicate the actual deployment in a 24/7 operation. We wanted to test strategic points in the factory, such as intersections, parking density, and the staging area, so we could make the transition to deployment as seamless as possible. I remember one day when our CTO and Co-Founder, Ryan Gariepy, came down to the basement and his eyes circled the room, with a look on his face that can only be described as confusion with a hint of intrigue. Although he had no idea of the depth and scale of the testing space, he was extremely impressed, and he wasn’t the only one.
When the customer came by our basement testing center for their Factory Acceptance Test (FAT), their jaws hit the floor. That is one of my favorite memories working at OTTO; you never forget a customer’s face when you blow them away.
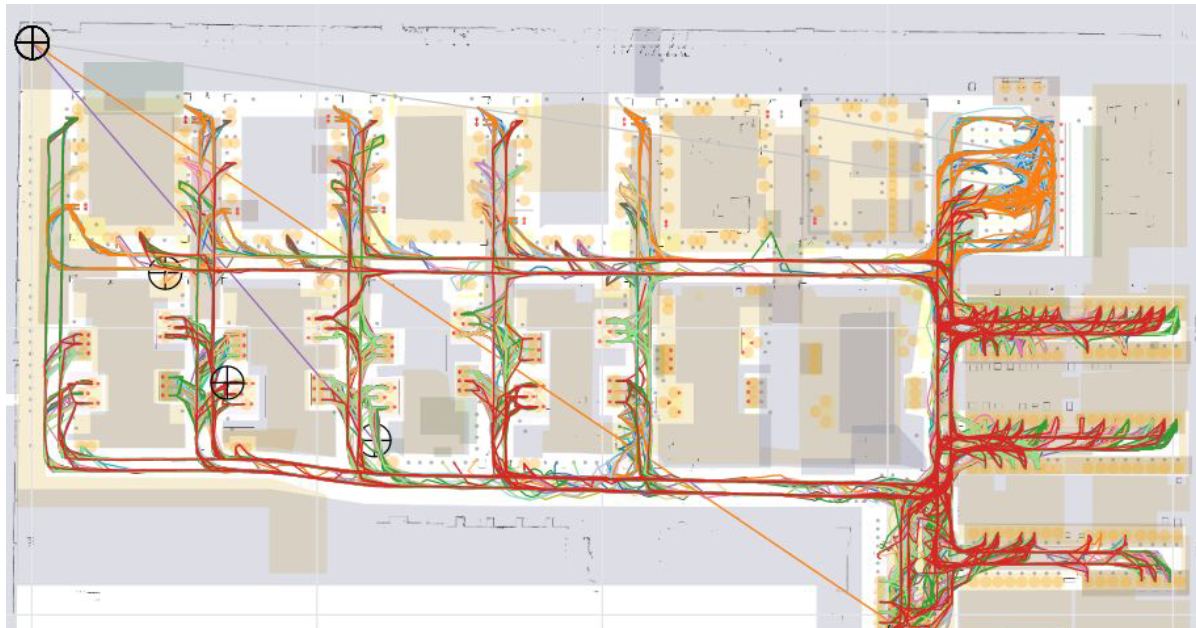
Image 2: A heatmap from the SAT, validating the traffic density of planned routes and ensuring consistency of AMR travel along the planned route.
Another challenge we faced was integrating with a custom middleware solution, which our systems integrator partner, PULSE Integration (now KPI), coordinated. While the robot’s mission was controlled with OTTO’s fleet management software, its interactions at endpoints and strategic decision making was managed by the middleware software. We had to ensure that PULSE’s middleware integrated seamlessly with both OTTO’s software and the facility’s higher systems applications and products (SAP) software.
Deploying the world’s largest AMR fleets, remotely
It was ultimately our relationship with PULSE that made the project as successful as it was. Together, PULSE and OTTO had an extremely strong desire to deliver a productive 83-robot fleet for the customer. There were no challenges we couldn’t overcome, and no opportunities we weren’t excited to explore. We listened to each other’s expertise in certain areas and kept the customer’s deployment, facility, and people at the forefront, ultimately achieving a successful, productive launch.
The success of the launch did not come without setbacks, however. When the COVID-19 pandemic changed the world, the deployment was only a quarter complete. OTTO had to remotely coach a single field service technician from PULSE through deploying this large fleet on site. While this was certainly an interesting experience, everyone involved was relaxed. We trusted our relationship with PULSE and had confidence in each other, and so did the customer.
Together, PULSE and OTTO deployed the large fleet of AMRs across a brownfield and greenfield facility of over 1.7 million square feet, where the robots traveled over 1,100 miles and executed more than 5,200 missions per day. The AMRs mitigated labor shortages amid COVID-19 and helped the manufacturer continue to meet rising customer demands while keeping workers safe. To this day, the customer is 100% reliant on OTTO technology for their material transport.
Video 1: A drone video capturing the Site Acceptance Test (SAT), which demonstrated the 83-robot system.
Evolving the North American material handling industry
This deployment unlocked OTTO’s unique ability to be highly productive at scale, ensuring over 100 robots will remain working and not congested in traffic jams, running out of battery, blocked from reaching endpoints or starving for work. This capability is the result of months of testing and hard work from the entire OTTO team. Thorough, clear documentation allowed us to seamlessly replicate scaled deployments for other large customers.
Throughout my many years with OTTO, I saw us transition from a mature solution to truly enterprise-scale.
Not only did this deployment change the future of OTTO, but it evolved the material handling industry in North America as well. Now, manufacturers across all industries have a scaled and productive fleet to reference when considering autonomous material handling solutions. This deployment proved that even the largest facilities with the deepest integrations can be automated, and I am so grateful to have been a part of this industry transformation.
Interested in a career at OTTO? Apply today.
Subscribe to our newsletter
Stay in the loop on product news, case studies, upcoming events and more.