Article
From market insights to customer experiences: Our take on MODEX 2020
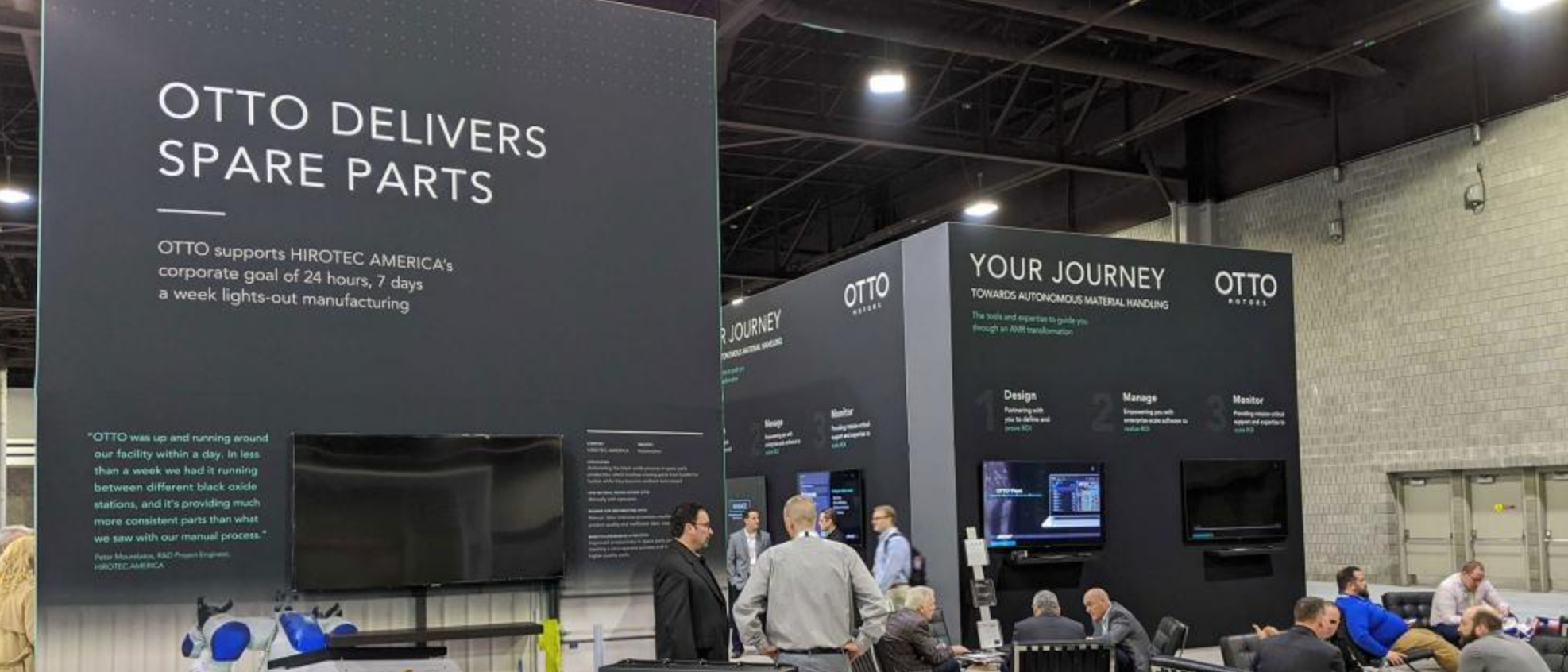
MODEX 2020 was certainly a different experience for attendees and exhibitors this year. On March 11th, while MODEX was in full swing, the World Health Organization announced that COVID-19 had become a global pandemic. Indeed, COVID became the backdrop of many of the conversations we had in the OTTO Motors booth but despite the circumstances, we had the opportunity to engage in many worthwhile conversations. Below are our top observations following MODEX:
The manufacturing market’s top challenges remain the same
At MODEX, the Material Handling Institute (MHI) — MODEX’s sponsor — released its latest Annual Industry Report. Not surprisingly, all five of the top company challenges remain the same since 2019’s report, with “hiring and retaining qualified workers” leading, as 56% of those surveyed listed it as a top concern. Other top concerns included:
- Customer demands for lower costs (51%)
- Customer demands on response times (48%)
- Rising customer service expectations (47%)
- Forecasting (46%)
Customer demands for customization have also been added to the list this year, with 41% of respondents citing it as a top concern.
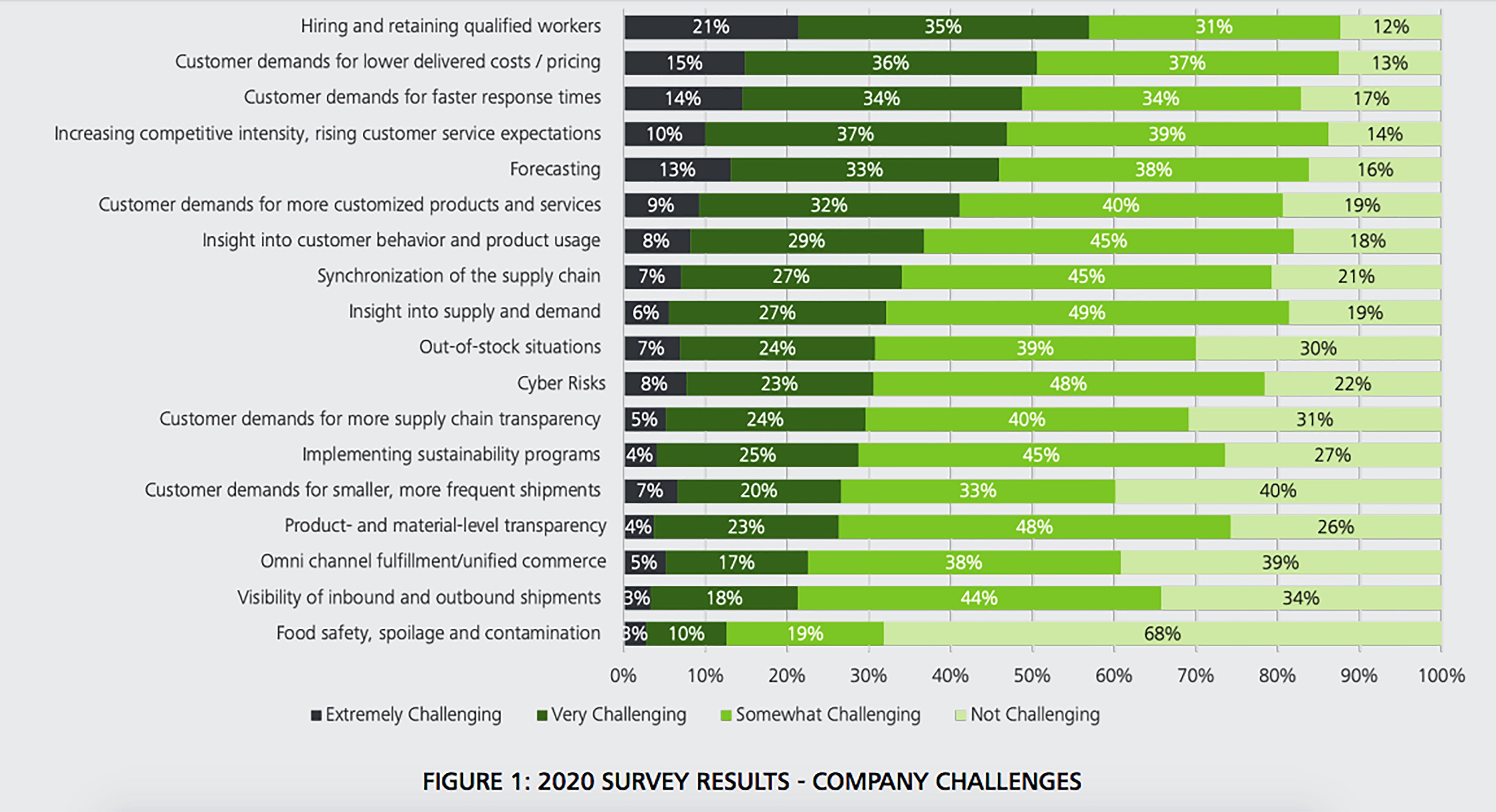
Chart 1: The full list of MHI's 2020 Top Company Challenges, with "hiring and retaining qualified workers" as the top challenge again this year.
Every single choice a customer makes when designing their product means a change to our manufacturing flow. This must be accounted for in the process layout, which makes it very complex to manage. Sometimes conveyorized flow just doesn’t work. We knew this complex logistical challenge could only be solved with autonomous mobile robots.
Kurt Oberparleiter
VP of Operations, Sunview Patio Doors
The top challenges mentioned in the MHI Report all reflect the market’s need for flexible and efficient material handling technology. By switching from manual to autonomous material handling, companies are able to create a more flexible supply chain because they can deliver different material to production lines without having to adjust any physical infrastructure. Autonomous Mobile Robot’s (AMR) ability to quickly adapt on the facility floor can help manufacturers meet their customer’s increasing expectations for customization.
Unlike manual material movement, via forklift, for example, Autonomous Mobile Robots (AMRs) collect and analyze data in order to help manufacturers forecast and adjust operations where needed.
Data is the life’s blood of the emerging digital supply chain. Companies that recognize the value of this data and engineer approaches to collect, filter and synthesize it into customer and market insights will flourish. Those who do not will drown in the wave of exponential data proliferation.
Thomas Boykin
Deloitte Consulting LLP
Autonomous material handling also reduces costs, a valuable factor as North America is facing an unprecedented skilled labor shortage. According to a study by Deloitte and The Manufacturing Institute, 4.6 million new manufacturing jobs are projected to be created by 2028, but 2.4 million of them could go unfilled because of a skilled-labor shortage. Deploying mobile robots can help retain workers by enabling them to focus on more complex, value-added tasks. The cost of turnover is roughly 33% of a salary and the main reason for the turnover is a lack of career development; your future engineer doesn’t want to push a cart all day.
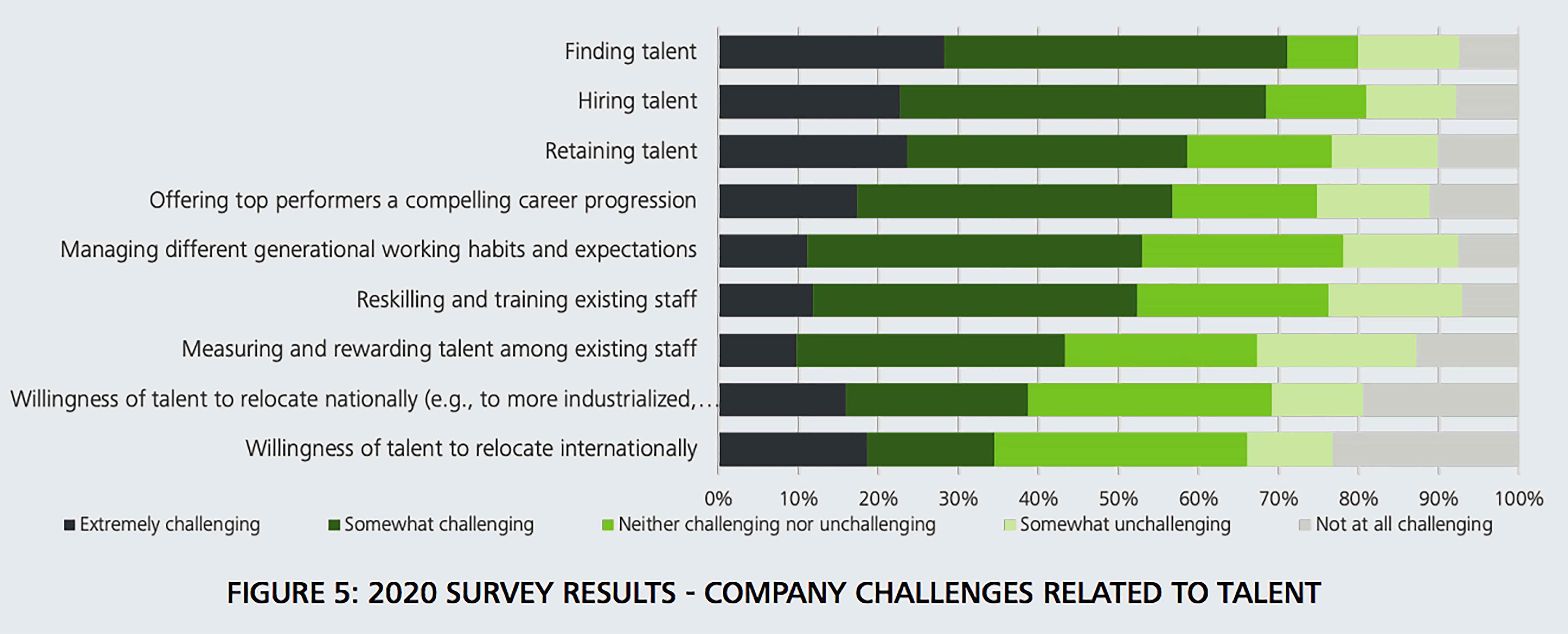
Chart 2: MHI’s 2020 Industry Report displays the top 9 company challenges related to talent, with finding, hiring and retaining talent being the most difficult.
AMR deployments are scaling
While the manufacturing industry’s challenges have not changed much since last year’s MHI Annual Industry Report, it was evident at MODEX 2020 that the AMR market has matured. Increasingly, manufacturers are implementing AMRs across their facilities, with 34% of manufacturing companies planning to adopt robotics and automation within the next five years, in addition to the 39% who have the technology in-use today. Manufacturers have moved past pilots and are now realizing the value of safe, efficient, and flexible autonomous material handling.
At MODEX, we showcased the journey that one of our Fortune 500 enterprise customers is taking to scale their AMR fleet. From working collaboratively with our automation experts and engineers to design the right material flow processes, to actually deploying their large fleet (60+ robots), and then monitoring and improving their operations, this global manufacturer is taking the next, important step towards improving their operation on a facility-wide scale.
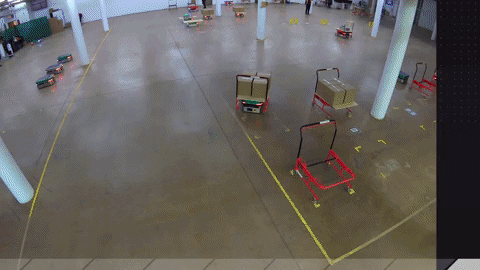
This shift toward scaling AMR deployments is partly due to the industry’s focus on software, rather than hardware, with cloud computing, machine learning and more sophisticated fleet management solutions all taking center stage.
The focus on these software-based technologies provides companies with easier collection and analysis of data. Many AMRs are also being designed to create an internal map of the facility's environment, so the robots learn different ‘rules of the road’, including speed limits, stopping at particular intersections, optimal charging and which aisles can only be driven down one way, for example.
Customer stories showcase end-to-end workflows
At MODEX 2020, many attendees were searching for examples of how AMRs are delivering business value in specific applications. At OTTO Motors’ booth, we showcased three customers in different industries using AMRs to drive value in their facilities.
1. OTTO delivers paper
Cober Solutions is a modern printing company thriving in the commercial printing business, where each customer order is unique. For years, Cober had been using skilled technicians and operators to manually move material from one location to the next, wasting time and resources. With OTTO, Cober has seen improved employee productivity and engagement with work, because skilled technicians are able to keep their machines running longer and stay focused on their value-added tasks, instead of spending a large portion of their shift manually pushing carts of materials to the next workcell.
2. OTTO delivers spare parts
HIROTEC AMERICA provides weld assembly equipment for original equipment manufacturers (OEM) including GM, Ford, and Toyota. Under their philosophy of continuous innovation, HIROTEC has worked towards 24/7 lights-out manufacturing and wanted to fully automate the black oxide process in their spare parts production. Before OTTO, this manual and labour-intensive process resulted in inconsistent product quality and inefficient labour usage. Through the integration of an OTTO AMR and a dual-arm manipulator, HIROTEC has not only increased their production by reaching a zero operator process but has also begun their journey toward becoming a connected factory capable of lights-out manufacturing.
3. OTTO delivers patio doors
Sunview Patio Doors manufactures doors for commercial use, and has certainly felt the effects of customers' increasing demands for customization - one of MHI’s top company challenges. The company needed a solution that was flexible, safe around workers, and efficient in order to remain competitive in their evolving industry. After implementing OTTO AMR technology, Sunview has moved 2.5+ million pounds of material with zero safety incidents, while achieving a 16-month ROI.
OTTO is the safest and smartest material handling automation that I’ve worked with ensuring the right materials are delivered to the right spot, at the right time, every time. OTTO has exceeded our expectations and phase two of implementation is already underway to expand our fleet.
Tony Margiotta
President, Sunview Patio Doors
At our MODEX booth, we brought Sunview’s facility to life through a 360-degree virtual reality tour of their warehouse floor.